Advancements in CNC Threading Tools and Inserts
CNC threading is a critical process in modern manufacturing, enabling the creation of precise and consistent threads for a variety of applications. The evolution of tools and inserts used in CNC threading has significantly improved the efficiency, accuracy, and versatility of these operations.
This article explores the recent advancements in CNC threading tools and inserts and their impact on the manufacturing industry.
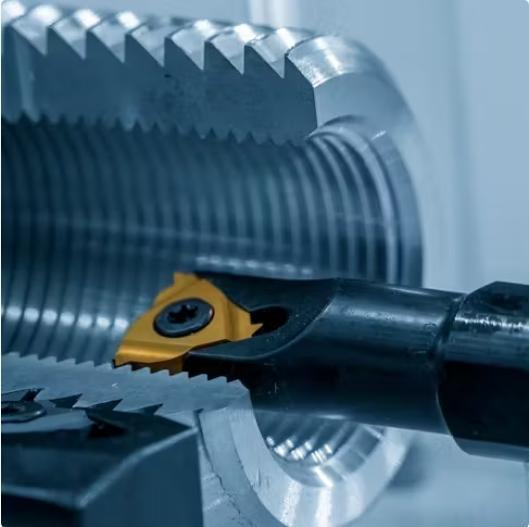
Evolution of Tools and Inserts Used in CNC Threading
Traditionally, threading was a labor-intensive process requiring skilled operators to manually cut threads using taps and dies. The introduction of CNC technology brought automation and precision for threading machining, but recent advancements have taken CNC threading to new heights.
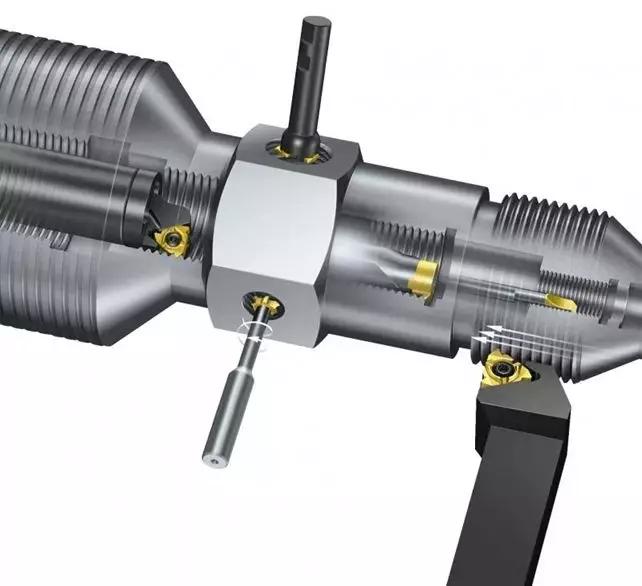
1. Advanced Materials
- Carbide: Known for its hardness and wear resistance, carbide is widely used in threading tools and inserts, offering excellent performance and durability.
- Cermet: A composite material combining ceramic and metallic components, cermet provides superior wear resistance and is ideal for high-speed machining.
- Polycrystalline Diamond (PCD): PCD is extremely hard and wear-resistant, making it suitable for high-precision threading in non-ferrous metals and composites.
2. Coatings
- Titanium Nitride (TiN): TiN coatings reduce friction, enhance wear resistance, and improve heat dissipation, leading to longer tool life and better surface finishes.
- Aluminum Titanium Nitride (AlTiN): AlTiN offers excellent thermal stability and oxidation resistance, allowing for higher cutting speeds and improved performance in tough materials.
- Diamond-like Carbon (DLC): DLC coatings provide exceptional hardness and low friction, making them ideal for high-precision applications.
3. Innovative Geometries
- Variable Helix Angles: These help reduce vibrations and chatter during threading, resulting in smoother finishes and longer tool life.
- Optimized Rake Angles: Improved rake angles enhance chip evacuation and reduce cutting forces, leading to better performance and reduced tool wear.
4. Precision Engineering
- Micro-Finishing: Advanced manufacturing techniques enable the production of threading tools and inserts with micro-finished surfaces, improving accuracy and performance.
- Tighter Tolerances: Modern machining technologies allow for the creation of tools and inserts with tighter tolerances, ensuring consistent thread quality and fit.
5. Modular Tooling Systems
- Quick-Change Inserts: Modular systems with quick-change inserts reduce downtime and increase productivity by allowing for rapid tool changes without the need for re-calibration.
- Multi-Functional Tools: Tools designed for multiple operations, such as turning and threading, streamline the machining process and reduce tool inventory.
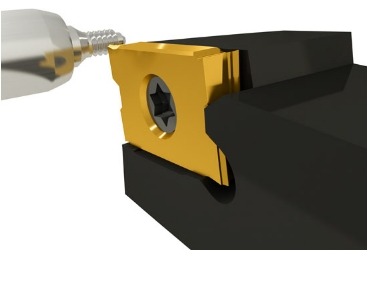
Benefits of Advanced CNC Threading Tools and Inserts
- Increased Productivity: Enhanced materials and coatings allow for higher cutting speeds and feed rates, reducing cycle times and boosting overall productivity.
- Improved Thread Quality: Precision engineering and innovative geometries result in higher thread accuracy, better surface finishes, and consistent thread profiles.
- Extended Tool Life: Durable materials and advanced coatings extend the life of threading tools and inserts, reducing replacement costs and minimizing downtime.
- Versatility: Modern tools and inserts are designed to handle a wide range of materials, from soft metals to hard alloys and composites, providing flexibility in manufacturing.
- Cost Savings: The combination of increased tool life, higher productivity, and improved thread quality leads to lower overall production costs.
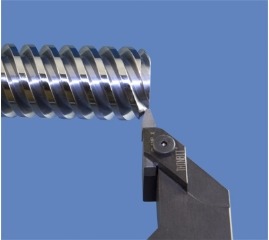
Applications of Advanced CNC Threading Tools and Inserts
The advancements in CNC threading tools and inserts have broadened their applications across various industries.
Industry | Application |
Automotive | Precision threading for engine components, transmission parts, and fasteners, ensuring reliable performance and safety. |
Aerospace | High-performance threading for critical components such as turbine blades, landing gear, and structural parts, where precision and reliability are paramount. |
Oil and Gas | Threading tools for producing drilling equipment, pipelines, and valve components capable of handling tough materials and harsh environments. |
Medical | Precision threading for orthopedic implants, surgical instruments, and dental tools, where accuracy and biocompatibility are essential. |
General Manufacturing | Threading tools and inserts for producing a wide range of threaded components in consumer electronics, industrial machinery, and other applications requiring high precision and efficiency. |
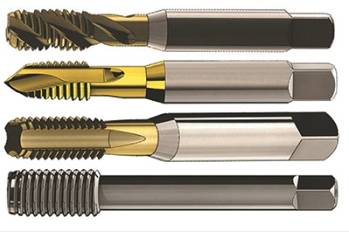
Future Trends of Tools and Inserts Used in CNC Threading
The next generation of tools and inserts used in CNC thread will push the boundaries of what is possible, paving the way for more innovative and sustainable manufacturing solutions.
1. Integration of Smart Technologies
- Smart Tools: The integration of sensors and IoT (Internet of Things) technology in CNC threading tools allows for real-time monitoring of tool condition, wear, and performance. This enables predictive maintenance, reducing unexpected downtime and extending tool life.
- Data-Driven Optimization: Using big data and analytics, manufacturers can optimize cutting parameters, improve process efficiency, and ensure consistent quality. AI and machine learning algorithms can analyze performance data to predict tool wear and optimize machining strategies.
2. Additive Manufacturing
- Hybrid Tools: Combining CNC machining with additive manufacturing (AM) techniques can create hybrid tools with complex geometries and enhanced performance characteristics. This allows for the production of custom-designed threading tools with tailored properties for specific applications.
- Rapid Prototyping: Additive manufacturing enables rapid prototyping of new tool designs, allowing for faster development cycles and more innovative solutions. This accelerates the introduction of new threading tools and inserts to the market.
3. Advanced Materials and Coatings
- Nanostructured Coatings: The development of nanostructured coatings can provide superior hardness, wear resistance, and thermal stability. These coatings improve tool performance and longevity, enabling higher cutting speeds and better surface finishes.
- Eco-Friendly Materials: Sustainable manufacturing practices are driving the development of eco-friendly materials and coatings. These innovations aim to reduce the environmental impact of CNC machining operations while maintaining or enhancing tool performance.
4. Enhanced Geometries and Designs
- Complex Geometries: Advances in manufacturing technologies, such as multi-axis CNC machines, allow for the creation of threading tools and inserts with complex geometries. These designs can improve chip control, reduce cutting forces, and enhance surface finishes.
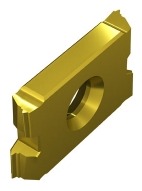
5. Sustainable Machining
- Energy-Efficient Processes: The focus on sustainability is leading to the development of energy-efficient machining processes. Innovations in tool design and materials aim to reduce energy consumption while maintaining high levels of productivity and precision.
- Waste Reduction: Advanced tool designs and manufacturing techniques are being developed to minimize waste generation. This includes optimizing tool paths, improving material utilization, and recycling worn tools and inserts.
6. Customized Solutions
- Tailored Tooling: The demand for customized tooling solutions is growing, driven by the need for precision in specialized applications. Advanced manufacturing techniques and materials enable the production of bespoke threading tools that meet specific customer requirements.
- Industry-Specific Innovations: Different industries have unique threading requirements. Future advancements will likely focus on developing industry-specific tools and inserts used in CNC threading that address the challenges and demands of sectors such as aerospace, medical, and oil and gas.
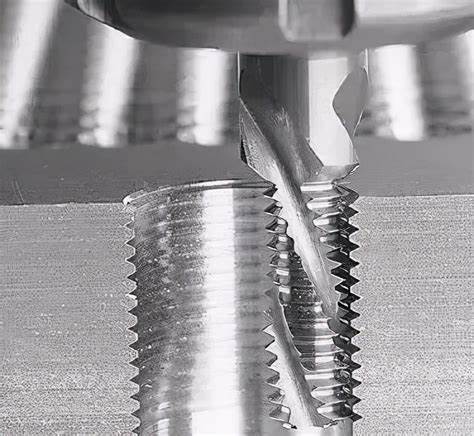
Conclusion
Advancements in CNC threading tools and inserts have significantly transformed the manufacturing landscape. The use of advanced materials, innovative geometries, precision engineering, and smart technologies has greatly enhanced the efficiency, accuracy, and versatility of CNC threading operations.