CNC Thread Milling and CNC Thread Tapping: A Comparative Analysis
Creating threads in a workpiece is a critical aspect of precision machining, with CNC thread milling and CNC thread tapping being the two predominant methods. Each has its unique advantages, applications, and challenges. Understanding these differences can help manufacturers choose the most suitable method for their specific needs.
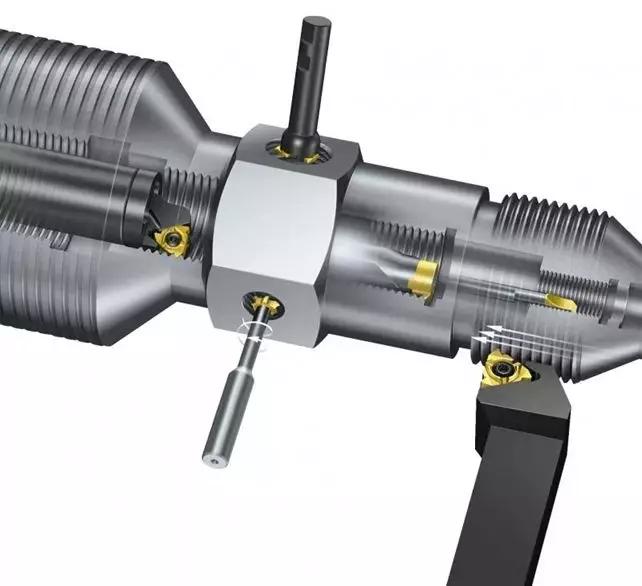
What is CNC Thread Milling
Definition
CNC thread milling is a CNC machining process used to create internal or external threads on a workpiece. This process involves the use of a rotating, multi-point cutting tool (thread mill) that moves along a helical path to form threads. Unlike tapping, thread milling can produce both right-hand and left-hand threads using the same tool.
Process
1. Preparation
- Workpiece Setup: Secure the workpiece in the CNC machine’s workholding device.
- Tool Selection: Choose the appropriate thread mill cutter based on the desired thread size, pitch, and material.
2. Programming
- CNC Programming: Create a CNC program that defines the helical tool path required to cut the threads. This includes specifying the start and end points, depth of cut, and feed rate.
- G-Code Generation: Convert the tool path into G-code, the language used by CNC machines to control movements and operations.
3. Toolpath Execution
- Initial Positioning: Position the thread mill at the starting point of the thread path.
- Cutting Path: The thread mill begins rotating and moves along the programmed helical path. The cutter gradually engages the material, removing it in a controlled manner to form the thread profile.
- Helical Motion: The tool moves in a helical pattern, which is a combination of linear and rotational movements. This creates the thread’s spiral shape.
4. Depth Control
- Incremental Cuts: For deep threads, the process may require multiple passes, each taking a small amount of material. This minimizes tool wear and prevents excessive force on the workpiece.
- Final Depth: The tool continues cutting until the final thread depth is reached.
5. Finishing
- Surface Finish: Thread milling generally provides a high-quality surface finish. If necessary, additional finishing operations can be performed.
- Inspection: Check the threads for accuracy using appropriate measuring tools, such as thread gauges or micrometers.
6. Completion
- Tool Retraction: Retract the tool from the workpiece.
- Workpiece Removal: Remove the finished workpiece from the machine.
Applications
CNC thread milling is ideal for industries requiring high precision and superior surface finishes, such as aerospace, medical devices, and high-performance automotive components. It’s particularly beneficial for complex or custom thread forms and when working with difficult-to-machine materials.
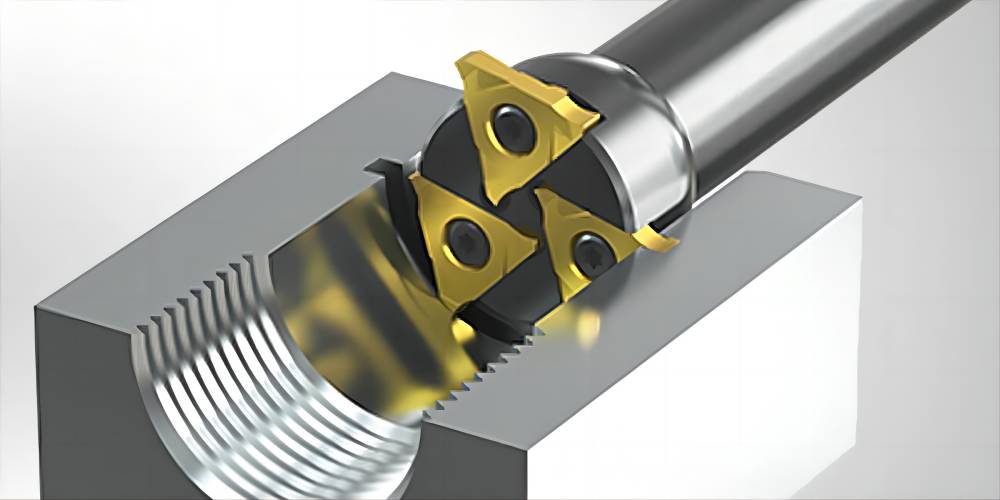
What is CNC Thread Tapping
Definition
CNC thread tapping is a machining process used to create internal threads within a pre-drilled hole. This process employs a specialized tool called a tap, which is driven into the hole to cut threads. CNC machines automate this process, ensuring consistency and precision in threading operations.
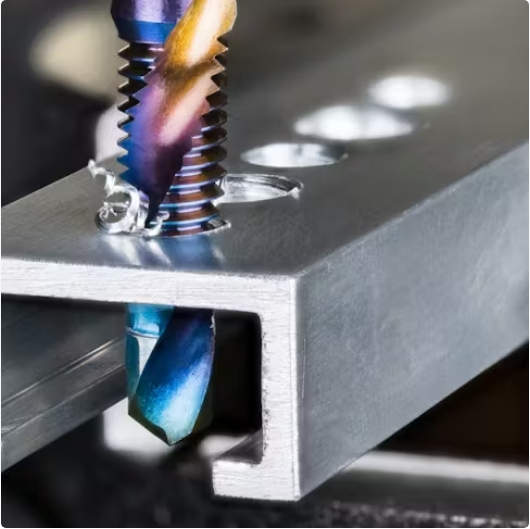
Process
1. Preparation
- Workpiece Setup: Secure the workpiece in the CNC machine’s workholding device.
- Tool Selection: Choose the appropriate tap based on the desired thread size, pitch, and material of the workpiece. Taps come in various forms, including taper, plug, and bottoming taps.
2. Programming
- CNC Programming: Create a CNC program that defines the toolpath for the tapping operation. This includes specifying the depth of the hole, the rotation speed, and the feed rate.
- G-Code Generation: Convert the toolpath into G-code, the language used by CNC machines to control movements and operations.
3. Drilling the Hole
- Pre-Drilling: Before tapping, a hole is drilled into the workpiece. The diameter of this hole is slightly smaller than the desired thread size.
- Positioning: Position the drill bit at the starting point and drill to the specified depth.
4. Tapping
- Initial Positioning: Position the tap above the pre-drilled hole.
- Engagement: The CNC machine aligns the tap with the hole and begins rotating it while feeding it into the hole.
- Cutting Threads: As the tap rotates and advances into the hole, its cutting edges remove material to form the threads. The process continues until the tap reaches the programmed depth.
- Chip Evacuation: Taps often have flutes to evacuate chips from the hole, preventing clogging and ensuring smooth thread formation.
5. Retraction
- Reverse Rotation: Once the threads are cut to the desired depth, the CNC machine reverses the rotation of the tap.
- Tool Withdrawal: The tap is then withdrawn from the hole while continuing to rotate in the reverse direction. This prevents damage to the newly formed threads.
6. Finishing
- Surface Finish: Tapping generally provides a good surface finish, although it may not be as high-quality as thread milling.
- Inspection: Inspect the threads for accuracy and conformity to specifications using appropriate measuring tools, such as thread gauges.
7. Completion
- Tool Retraction: Fully retract the tap from the workpiece.
- Workpiece Removal: Remove the finished workpiece from the machine.
Applications
CNC thread tapping is commonly used in general manufacturing, consumer goods production, and other applications where speed and cost efficiency are critical. It is particularly suitable for creating internal threads in a wide variety of parts, ranging from small screws to large industrial components.
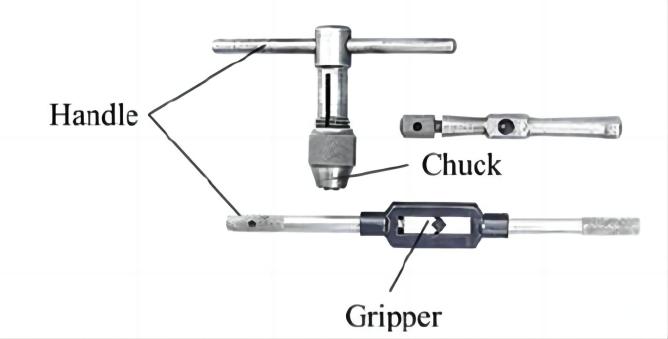
Key Comparisons in CNC Thread Milling and CNC Thread Tapping
Aspect | CNC Thread Milling | CNC Thread Tapping |
Precision and Quality | High precision with tight tolerances Excellent surface finish | Adequate precision for most applications Good surface finish |
Tool Flexibility | One tool can handle various sizes and pitches Easy diameter adjustments | Each tap specific to one size and pitch Limited flexibility |
Material Suitability | Effective on a wide range of materials Ideal for hard-to-machine alloys | Best suited for softer materials Challenges with harder materials |
Speed and Efficiency | Generally slower process Longer cycle times | Faster process Shorter cycle times Efficient for high-volume production |
Tool Life and Cost | Higher initial tool cost Longer tool life Less frequent replacements | Lower tool cost Higher wear rate More frequent replacements |
Setup and Programming | Requires complex setup and skilled operators Advanced programming needed | Simpler setup Less complex programming Less training required |
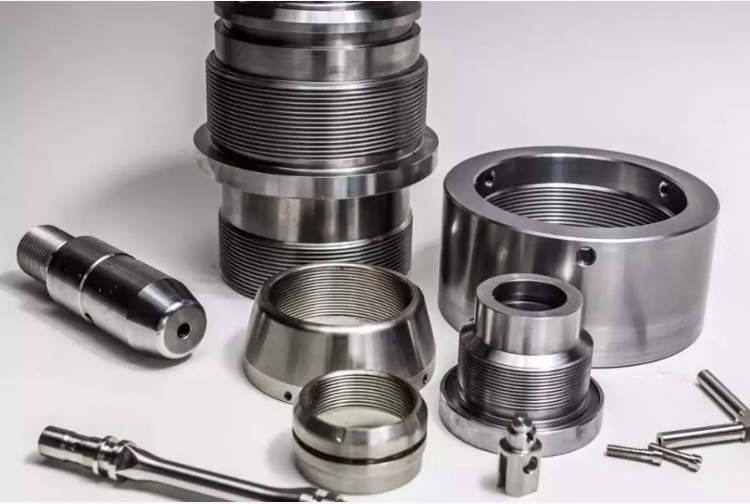
How to Choose Between CNC Thread Milling and CNC Thread Tapping
When choosing between CNC thread milling and CNC thread tapping, consider the following:
- High precision and excellent surface finish: CNC thread milling.
- Working with hard materials or minimizing tool pressure: CNC thread milling.
- High-volume production with faster cycle times: CNC thread tapping.
- Flexibility in thread sizes and long-term cost efficiency: CNC thread milling.
- Simpler setup and programming: CNC thread tapping.
- Standard thread forms in general manufacturing: CNC thread tapping.
By evaluating these factors based on your specific needs, you can determine the most suitable CNC threading method for your machining operations.
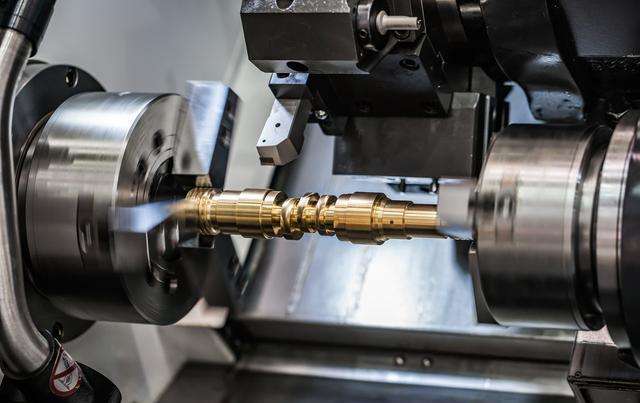
Conclusion
CNC thread milling excels in precision, flexibility, and material versatility, making it ideal for high-precision applications. CNC thread tapping, however, offers speed, simplicity, and cost-efficiency, making it suitable for high-volume production. Understanding the strengths and limitations of each method enables manufacturers to optimize their processes for better efficiency, quality, and cost management.