CNC Threading vs. Traditional Threading: Which Method to Choose
Threading is a crucial machining process used to create helical grooves on screws, bolts, pipes, and other cylindrical components. Over the years, threading methods have evolved from manual techniques to advanced CNC machining. When choosing between CNC threading vs. traditional threading methods. Each has its own advantages, limitations, and ideal applications. This article dives into the key differences between CNC threading vs. traditional threading and helps identify the right threading solution based on production needs.
Table of Contents
Overview of CNC Threading
CNC threading is a precise and automated method of creating screw threads using CNC machines. It eliminates much of the manual effort found in traditional threading by relying on pre-programmed code (G-code) to control the motion of cutting tools. CNC threading is commonly used in industries that demand tight tolerances and high-volume production.
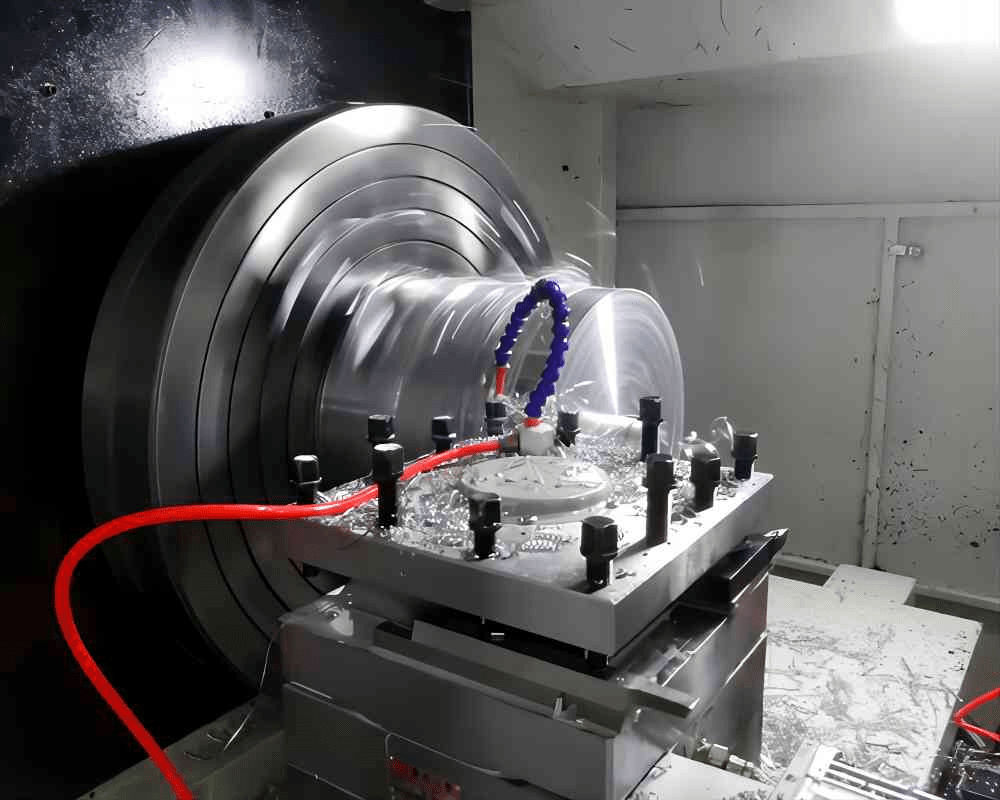
Common CNC Threading Methods
- Single-point threading: Tool moves along the axis of rotation to cut the thread one pass at a time.
- Thread milling: A rotating tool cuts the thread in a helical path—suitable for both internal and external threads.
- Tapping with CNC: For internal threads, using powered taps within CNC programs.
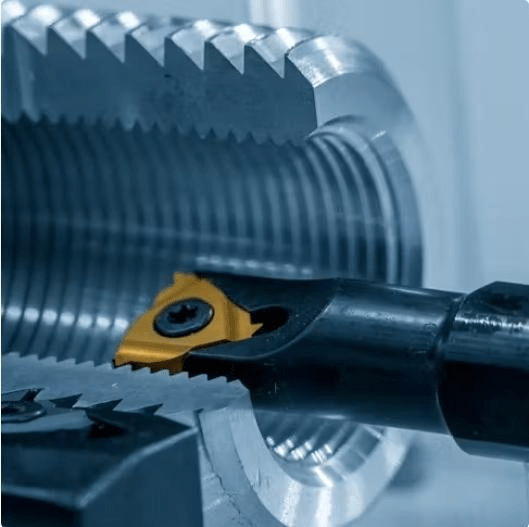
Advantages
High Precision and Repeatability: CNC machines can consistently reproduce thread forms with minimal deviation, even across large production batches.
Efficient for Complex Threads: Capable of producing custom or complex thread profiles such as ACME, buttress, multi-start, or tapered threads with ease.
Fast Production Speeds: Once a program is set up, the threading process is quick and requires minimal human intervention, boosting productivity.
Supports Various Materials: CNC machines can cut threads into tough materials like titanium, stainless steel, and hardened alloys with optimized tooling.
Reduces Human Error: Automation reduces the possibility of operator error, improving product quality and reducing rework or waste.
Limitations
- High Initial Investment: CNC machines and their supporting software can be expensive to purchase and maintain, making them less suitable for small shops with limited budgets.
- Programming Required: CNC threading requires skilled programming (usually G-code or CAM software), which can be a barrier for facilities without trained staff.
- Not Ideal for Quick, One-Off Jobs: For small or emergency jobs, traditional threading methods are often faster due to the setup time CNC requires.
- Machine Downtime During Setup: Complex thread profiles or small batch runs may lead to longer setup and calibration times, affecting efficiency for low-volume production.
- Tool Wear and Breakage: Though precise, CNC tools are not immune to wear, especially when cutting threads in abrasive or very hard materials. Tool monitoring and replacement add to operational complexity.
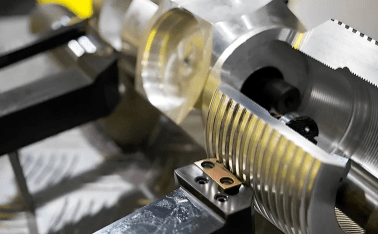
Overview of Traditional Threading
Traditional threading is the process of creating threaded features (such as screws, bolts, and other fasteners) on a workpiece using manual tools or mechanical machines like lathes, taps, and dies. Unlike CNC threading, which relies on automated machines controlled by programming, traditional threading is performed manually or semi-automatically, relying heavily on the operator’s skill and experience.
Key Features
Manual or Semi-Automatic Operation
Traditional threading typically involves tools such as taps, dies, or lathe machines where the operator manually feeds the tool into the material or adjusts the machine to create the thread. Some machines may provide partial automation, such as automatic threading lathes, but they still require operator control for setup.
Basic Equipment
The equipment for traditional threading is simpler and more affordable compared to CNC machines. Common tools include:
- Hand Taps and Dies: Used for threading holes or rods by hand or with basic machine setups.
- Lathe Machines: Manually controlled machines that create threads by rotating the workpiece against a cutting tool.
Flexibility
One of the main advantages of traditional threading is its flexibility. It allows operators to quickly switch between different thread types or sizes, adjust threading parameters during the process, and easily modify setups for small, custom jobs.
Short Setup Time
Traditional threading methods generally have shorter setup times compared to CNC, especially when producing small quantities or single parts. The operator can manually adjust tools and settings without having to program a machine or load complex software.
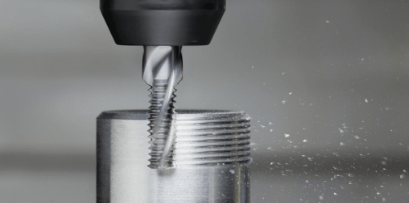
Advantages
- Lower Initial Investment: Traditional threading tools and machines are much less expensive to acquire and maintain compared to CNC machines, making it a more affordable option for small workshops or businesses with a limited budget.
- Quick for Low-Volume or One-Off Jobs: If you only need a few parts or a one-off threaded component, traditional threading is ideal. The operator can quickly set up and start the process without needing to write or load a program.
- No Programming Needed: Traditional threading doesn’t require programming, so it’s more accessible for those without experience in CNC programming. This can be advantageous for small shops that may not have access to specialized CNC operators.
- Simplicity in Design: Traditional threading is often well-suited for standard, straightforward threads (such as common bolt threads) that don’t require intricate or custom designs.
Limitations
- Dependence on Operator Skill: The quality of the thread is largely dependent on the skill and consistency of the operator. Variations in manual control can result in inconsistent threads, which can lead to defects or the need for rework.
- Lower Precision and Repeatability: While manual threading can be precise, it’s less consistent than CNC threading, especially in high-volume production. Small variations between parts are common due to human error, tool wear, or slight changes in operator technique.
- Not Ideal for Complex Thread Designs: Traditional threading tools are best suited for basic thread profiles like standard single-start threads. It becomes more challenging and time-consuming to create complex, multi-start, or custom thread forms manually.
- Time-Consuming for High Volumes: For large production runs, traditional threading can become slower compared to CNC machines, as each part requires manual setup, adjustment, and cutting.
- Limited Material Handling: Traditional methods may struggle with tougher or more complex materials, as manual tools don’t provide the fine control or power needed to handle harder metals as efficiently as CNC machines.
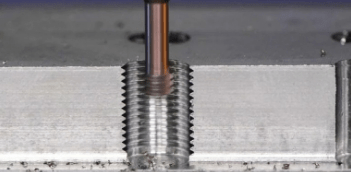
Key Differences Between CNC vs. Traditional Threading
Feature | CNC Threading | Traditional Threading |
Operation Type | Automated via programmed CNC machines | Manual operation using lathes, taps, or dies |
Precision & Accuracy | High precision with excellent repeatability | Operator-dependent; variable accuracy |
Speed & Efficiency | Fast for batch production; minimal downtime | Slower, especially for high-volume tasks |
Thread Complexity | Easily handles complex and custom thread profiles | Limited to simpler, standard thread types |
Consistency in Output | Uniform results across all parts | Inconsistent results in batch production |
Setup Time | Longer initial setup/programming, but faster production | Quicker to start single jobs, longer per-piece processing |
Skill Requirement | Requires CNC programming knowledge | Requires manual machining skills |
Cost (Initial Investment) | High due to machine and software costs | Low, suitable for small workshops or repairs |
Cost (Long-Term) | More cost-effective for large-scale production | More costly over time for mass production due to labor |
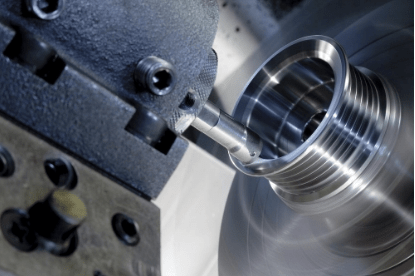
Which Method to Choose Between CNC Threading vs. Traditional Threading
When to Choose CNC Threading
High Production Volume
CNC threading is ideal when you need to produce a large number of parts with identical thread patterns. Once the program is set up, CNC machines can operate continuously, allowing for fast production with minimal manual input.
High Precision and Accuracy
If you require high precision, tight tolerances, and consistency across many parts, CNC threading is the best option. The automated process ensures repeatable results without variation from one part to the next.
Complex Thread Profiles
CNC threading is capable of creating more complex or non-standard thread types, such as multi-start, tapered, or custom thread forms. The flexibility of the machine allows for intricate geometries that would be difficult or time-consuming to achieve manually.
Hard or Exotic Materials
CNC threading excels when working with tough materials like hardened steels, titanium, or specialized alloys. The machine can handle these materials effectively with precise control over cutting speed and tool pressure.
Labor Efficiency and Automation
If you want to reduce human error and the need for skilled operators on each part, CNC threading is a great choice. The process is automated and requires less operator intervention, which also reduces labor costs over time.
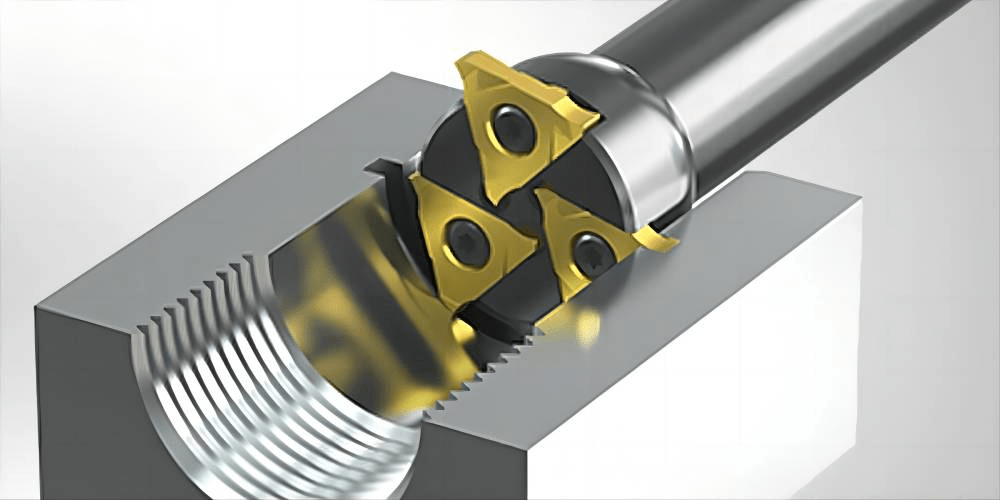
When to Choose Traditional Threading
Low-Volume or One-Off Jobs
If you are working on a small batch, prototype, or repair job where the need for mass production is not essential, traditional threading is often more practical. It offers quicker setup and allows for more flexibility when dealing with a variety of parts.
Lower Initial Investment
Traditional threading involves simpler tools and machines, which makes it more cost-effective in the short term. Small workshops or businesses with limited budgets may find manual threading tools like taps, dies, and lathes more accessible.
Simplicity and Custom Work
If your project requires a simple or common thread form and you need the flexibility to make adjustments on the fly, traditional threading allows operators to exercise more control. It is particularly useful for jobs where threads are straightforward and don’t require high precision or complexity.
Shorter Setup Time for Small Jobs
For quick turnarounds on smaller jobs, traditional threading can be more efficient, as the setup time for manual threading is typically shorter than setting up a CNC program, especially if it’s a one-off task.
Summary
- Choose CNC Threading if you need high-volume production, precise threads, complex designs, or are working with difficult materials.
- Choose Traditional Threading if you’re handling small batches, one-off jobs, or need cost-effective solutions for simpler, common threading tasks.
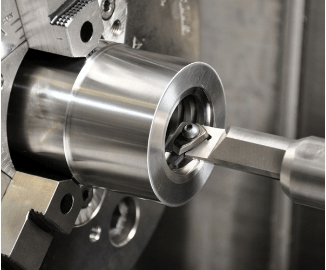
Final Thoughts
For businesses aiming to scale, improve quality and reduce production time, CNC threading is the preferred choice. However, traditional threading methods still hold value where manual craftsmanship and low-cost equipment suffice. Through aligning your specific needs with the strengths of each method, you can determine the most suitable approach for your threading tasks.