CNC vs 3D Printing: Which is Right for Your Parts
As manufacturing technologies continue to evolve, CNC machining (Computer Numerical Control) and 3D printing (Additive Manufacturing) have emerged as two of the most prominent production methods today.
Whether for custom parts, rapid prototyping, or batch production, businesses and engineers often find themselves torn between these two technologies. So, what are the key differences between CNC vs 3D printing? How should you choose the right one for different scenarios? In this post, we will provide all the answers you need. Let’s get started!
Table of Contents
Part 1. What is CNC Machining?
CNC (Computer Numerical Control) machining is a subtractive manufacturing process that removes material from a solid block—typically metal or plastic—using computer-controlled cutting tools.
The process involves programming instructions (G-code) into CNC machines, which then operate automatically with high precision to produce parts with complex geometries.
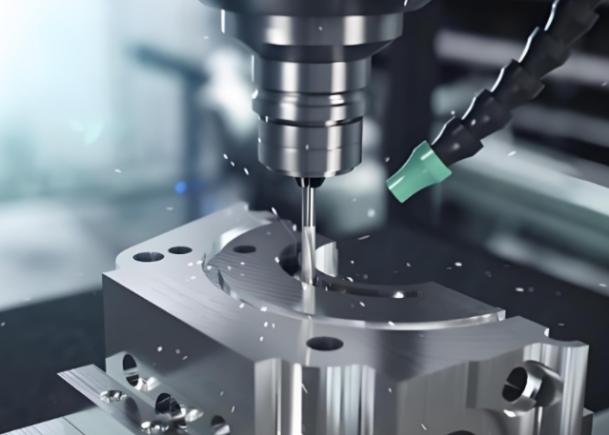
Common types of CNC machines include:
- CNC milling machines – for cutting and shaping in multiple axes
- CNC lathes – for turning cylindrical parts
- CNC drilling machines – for precise hole placement
- CNC routers – for woodworking and lighter materials
Key Features of CNC Machining:
High Precision:
CNC machining delivers extremely tight tolerances, making it ideal for producing complex and highly accurate components.
Wide Material Compatibility:
Supports a broad range of materials including metals (aluminum, steel, titanium), plastics (ABS, POM, PC), wood, and composites.
Excellent Repeatability and Stability:
Once the program is set, CNC machines can reproduce parts consistently, making them suitable for medium to large-scale production runs.
Superior Surface Finish:
Parts typically come off the machine with a smooth surface and often require minimal post-processing, especially when compared to 3D-printed parts.
Ideal Applications of CNC Machining:
Automotive Parts:
Engine components, transmission housings, custom brackets, and suspension elements requiring durability and accuracy.
Aerospace Components:
Critical parts such as turbine blades, aircraft structural frames, and landing gear elements where strength, weight, and precision are crucial.
Industrial Molds and Tooling:
CNC machining is widely used to manufacture injection molds, die-casting molds, and precision tools due to its accuracy and repeatability.
High-Strength Structural Parts:
Suitable for components that need to withstand mechanical stress, including frames, supports, and load-bearing mechanisms.
Part 2. What is 3D Printing?
3D printing, also known as Additive Manufacturing, is a process that creates three-dimensional objects by building them layer by layer from digital models. Unlike subtractive methods like CNC machining, 3D printing adds material only where needed, making it highly efficient and versatile for modern prototyping and manufacturing.
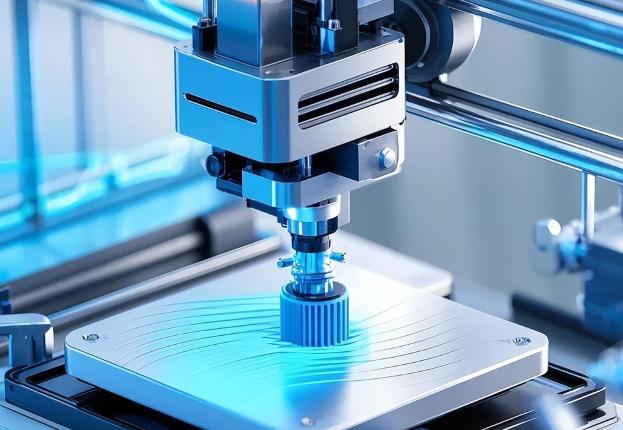
Common types of 3D printing technologies include:
FDM (Fused Deposition Modeling):
Melts and extrudes thermoplastic filament to form layers; widely used for functional prototypes and low-cost models.
SLA (Stereolithography):
Uses a UV laser to cure liquid resin layer by layer; offers high-resolution parts with smooth surfaces, ideal for fine details.
SLS (Selective Laser Sintering):
Fuses powdered materials (usually nylon or polymer) with a laser; creates strong, functional parts without the need for support structures.
Key Features of 3D Printing:
High Design Freedom:
3D printing can produce complex geometries that are difficult or even impossible to achieve with traditional manufacturing—such as internal channels, lattice structures, or organic shapes.
Rapid Prototyping:
Ideal for speeding up the product development cycle—from CAD model to physical prototype in hours or days, enabling quick design validation and iteration.
High Material Efficiency:
Because it only deposits material where needed, 3D printing generates minimal waste, making it more environmentally friendly compared to subtractive methods.
Ideal for Small-Batch, Custom, or On-Demand Production:
No need for molds or tooling, making it cost-effective for short runs or mass customization of parts.
Ideal Applications of 3D Printing:
Product Appearance Prototypes:
Used in early design stages to visualize and test the look and feel of a product, from consumer electronics to home appliances.
Medical Models & Custom Implants:
Enables the creation of patient-specific anatomical models, surgical guides, and even bio-compatible implants tailored to individual needs.
Architectural and Design Models:
Architects and designers use 3D printing to create precise, scaled models of buildings, interiors, and structural designs for presentation and testing.
Educational and Research Prototypes:
Ideal for schools, universities, and research institutions to explore concepts, demonstrate theories, or build experimental components with ease.
Part 3. Core Comparison: CNC vs 3D Printing
What’s the key difference between 3D printing and CNC machining? Understanding the fundamental differences between these two manufacturing methods is crucial for making the right choice. Here’s a closer look at their core distinctions to help you decide which one best suits your needs.
1. Manufacturing Method
CNC machining is a subtractive process, which means it starts with a solid block of material and removes excess parts using cutting tools.
In contrast, 3D printing is an additive process that builds objects layer by layer, depositing material only where needed.
2. Material Range
CNC machines are compatible with a wide variety of materials, including metals (such as aluminum, steel, and titanium), plastics (like ABS and nylon), wood, and composite materials.
3D printing, while versatile, typically works with plastics, resins, and metal powders, depending on the printing technology used. Some high-end printers can process advanced engineering materials, but overall, the material range is still narrower than CNC.
3. Precision and Surface Finish
CNC machining offers exceptional accuracy and fine surface quality, often suitable for end-use parts without extensive post-processing.
3D printing, although improving rapidly, generally offers lower dimensional accuracy and often requires additional post-processing like sanding, polishing, or curing to achieve a smooth surface, especially for consumer-facing products.
4. Ability to Handle Complex Geometries
CNC machining struggles with very intricate or internal geometries, especially if they’re hard to reach with cutting tools.
3D printing excels here as it can easily create complex shapes, internal channels, and lattice structures that would be impossible or cost-prohibitive with traditional methods.
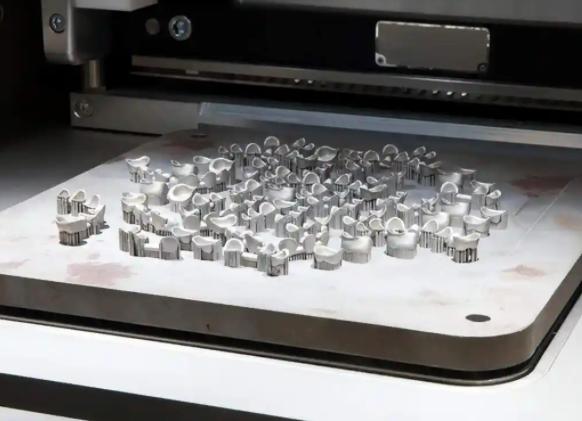
5. Production Speed
CNC machining is generally fast for actual production, especially for parts requiring tight tolerances. However, the setup time is longer due to the need for programming, tool selection, and fixture preparation.
3D printing offers rapid turnaround from design to part, particularly advantageous for prototyping and small-run custom parts.
6. Batch Suitability
CNC machining is more cost-effective for medium to large production runs, where the initial setup costs can be spread across many units.
3D printing shines in small-batch and on-demand production, especially when customization or multiple design variations are required.
7. Production Cost
CNC machining tends to be more expensive, especially for parts with complex geometries that require longer machining times and tool wear.
3D printing, on the other hand, offers lower entry costs, particularly when producing one-off pieces or varied designs, as it eliminates tooling and minimizes material waste.
Clean comparison table between 3D Printing and CNC Machining
Comparison Criteria | CNC Machining | 3D Printing |
Manufacturing Method | Subtractive – removes material | Additive – builds objects layer by layer |
Material Range | Metals, plastics, wood, etc. | Plastics, resins, metal powders, etc. |
Precision & Surface Finish | High precision, smooth surface finish | Moderate precision, post-processing often needed |
Complex Geometry Capability | Limited ability for complex internal shapes | Easily creates intricate and complex structures |
Processing Speed | Fast machining, longer setup time | Fast prototyping, short lead time |
Batch Suitability | More cost-effective for medium to large batches | More economical for small and varied batches |
Production Cost | Higher cost, especially for complex parts | Lower cost, ideal for diverse, low-volume needs |
Part 4. CNC vs 3D Printing: Which is One is Better?
Actually, there’s no one-size-fits-all answer when it comes to choosing between CNC machining and 3D printing. Each method has unique strengths and is suited for different applications. The “better” option ultimately depends on your specific project goals, material requirements, budget, and production volume.
1. Choose CNC Machining if you need:
- High precision and tight tolerances: Ideal for functional and mechanical parts.
- Superior surface finish: Perfect for applications that demand a polished look or minimal post-processing.
- Strong and durable materials: Works well with metals and engineering plastics.
- Medium to large batch production: Economical for scaling up manufacturing.
2. Choose 3D Printing if you need:
- Rapid prototyping: Great for fast iteration and concept validation.
- Complex geometries: Excellent for producing intricate shapes, internal channels, or lightweight lattice structures.
- Low-volume or one-off production: No tooling or setup costs make it cost-effective.
- Design flexibility: Perfect for custom or constantly evolving designs.
In many cases, CNC and 3D printing can complement each other. For instance, you might use 3D printing to quickly prototype a concept and CNC machining for the final production. By understanding the strengths of both, you can build a more efficient and flexible manufacturing workflow.
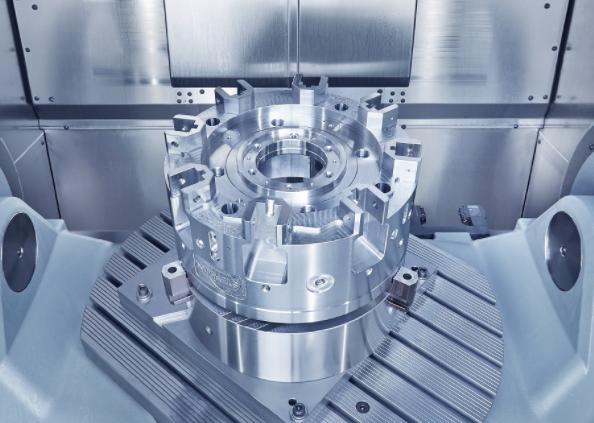
Final Words
CNC machining and 3D printing each offer distinct advantages. CNC is best for precision, durability, and large-scale production, while 3D printing excels in design flexibility and quick prototyping.
The right choice depends on your specific project needs. In many cases, using both methods together can provide the best results.