Developments in Anti-loosening Features of Flat Washers
Table of Contents
Flat washers are fundamental components in mechanical assemblies, enhancing the load distribution of fasteners and preventing surface damage. Over time, however, as engineering demands have evolved, traditional flat washers have shown limitations, especially in environments with high vibrations or load variations. Recent developments have aimed to improve the anti-loosening capabilities of flat washers, integrating advanced features that meet the rigorous demands of modern industries.
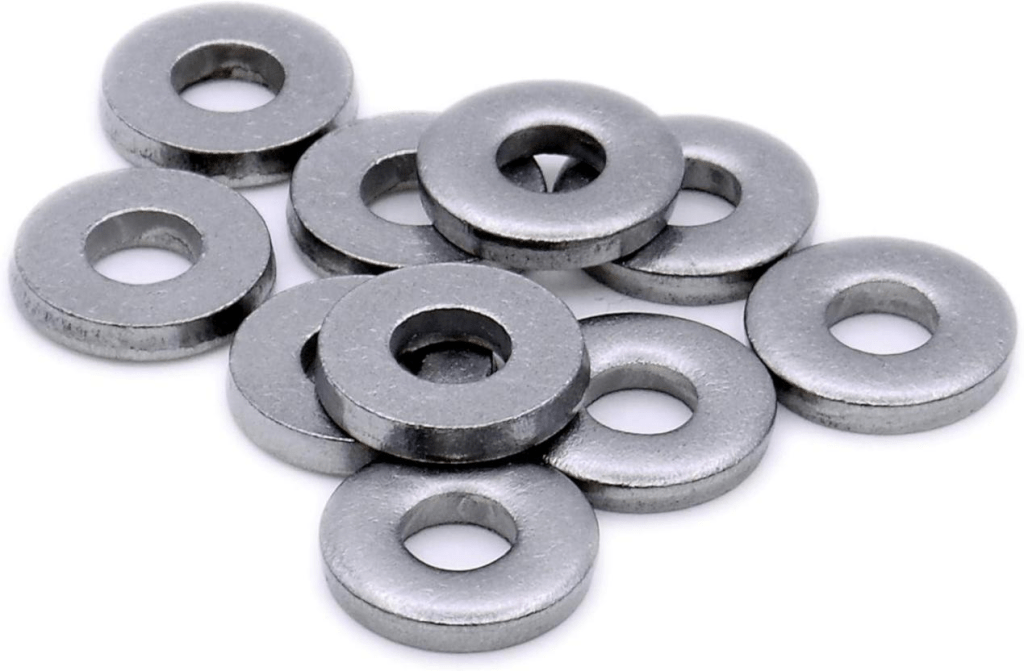
Why Anti-Loosening Features are Essential for Flat Washers
In applications where loosening can compromise safety and performance, such as automotive, aerospace, and heavy machinery, anti-loosening features in washers are critical. Loosening can result from dynamic stresses, temperature fluctuations, and vibrations, leading to costly maintenance and safety risks. Flat washers with anti-loosening developments now ensure assemblies remain stable, reducing downtime and increasing reliability.
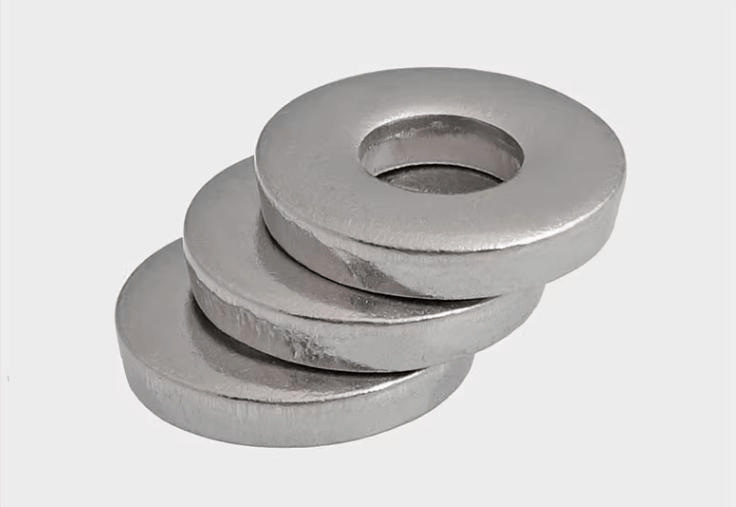
Innovations in Anti-Loosening Features of Flat Washers
Advancements in materials science and manufacturing techniques have enabled several notable improvements in the anti-loosening performance of flat washers
1. Micro-Serration Patterns
New manufacturing processes have enabled the precise formation of micro-serrations on washer surfaces. Unlike traditional serrations, micro-serrations provide a stronger grip on both the bolt and surface, creating a higher level of resistance to loosening. These micro-patterns are specifically effective in applications that experience moderate to high vibrations, such as in industrial equipment and automotive components, without damaging the surface material.
2. Dual-Layer Coatings for Added Friction
Enhanced coating techniques are now available to increase friction without the need for physical deformation. Dual-layer coatings, often combining zinc and a friction-enhancing polymer, significantly increase friction between the washer, fastener, and mating surface. These coatings are beneficial in environments where washers are exposed to moisture, chemicals, or corrosive agents, making them ideal for applications in marine, aerospace, and renewable energy sectors.
3. Integrated Spring Design
A unique innovation in flat washers is the development of washers with integrated spring features, known as wave or Belleville washers. These washers are designed with a slight wave shape that creates tension against the fastener. The spring design provides constant pressure, accommodating expansions and contractions due to temperature changes while maintaining a secure hold. Such washers are effective in preventing loosening over time, especially in environments subject to thermal cycling, such as electronics and aerospace applications.
4. Advanced Locking Tabs and Mechanical Interlocks
Mechanical interlock designs have been refined for use in demanding settings. Recent developments allow for multi-point locking tabs, where the washer securely grips the bolt and nut head in several positions, making it almost impossible for the assembly to loosen. This approach is especially valuable in heavy machinery and equipment exposed to strong impacts and vibrations, like mining and construction industries.
5. Composite Material Innovations
The adoption of composite materials in washer manufacturing has led to washers that are both lightweight and highly durable. Composite washers can be molded with friction-enhancing features directly into their structure, eliminating the need for additional coatings or treatments. These washers offer high anti-loosening performance without the added weight, making them popular in automotive and aerospace applications where reducing weight without compromising strength is crucial.
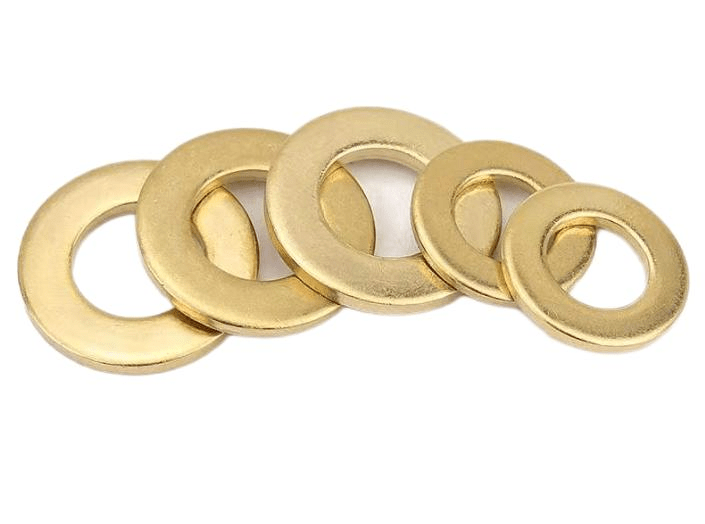
Applications of Advanced Anti-Loosening Flat Washers
This chart outlines where advanced anti-loosening flat washers are most effectively applied, along with the specific benefits they bring to each application.
Industry | Type of Anti-Loosening Flat Washer | Key Benefits | Example Use Cases |
Automotive | Micro-serration flat washers, dual-coated washers | Resists vibration loosening, corrosion protection | Engine mounts, suspension systems |
Aerospace | Lightweight composite flat washers, wave spring washers | Reduces weight, maintains tension in extreme conditions | Aircraft fasteners, avionics equipment |
Heavy Machinery & Construction | Mechanical locking tab flat washers, high-friction coatings | Enhances vibration resistance, easy installation | Excavators, cranes, mining equipment |
Marine | Dual-coated flat washers, corrosion-resistant composite washers | Withstands high moisture, salt, and corrosion | Ship decks, offshore platforms |
Electronics | Wave spring washers, micro-serrated washers | Maintains stable tension, handles temperature changes | Circuit boards, power supply assemblies |
Renewable Energy (Wind, Solar) | High-strength composite washers, locking tab washers | High durability, vibration resistance in dynamic environments | Wind turbine structures, solar panel mounts |
Oil & Gas | Corrosion-resistant and dual-coated flat washers | Maintains integrity under harsh environmental conditions | Pipeline fittings, offshore drilling rigs |
Medical Equipment | Lightweight, corrosion-resistant composite washers | Ensures long-term reliability in sensitive applications | Imaging devices, hospital bed assemblies |
Railway & Transportation | High-friction coated flat washers, locking tab washers | Maintains fastener security under constant motion | Rail tracks, train chassis connections |
Infrastructure & Bridges | Heavy-duty wave spring washers, high-friction coatings | Provides lasting stability, withstands environmental wear | Bridge joints, structural bolts |
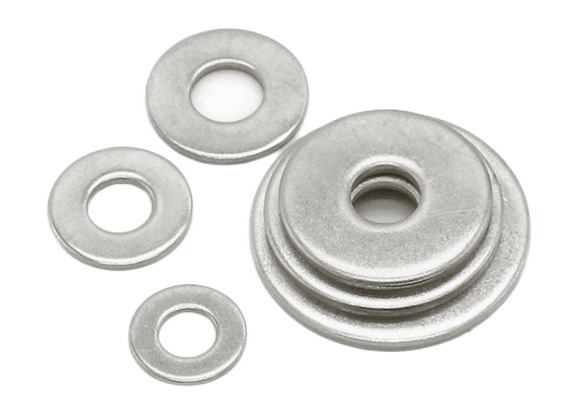
Key Considerations to Choose the Right Anti-loosening Flat Washers
This chart can serve as a quick reference guide to help select the right anti-loosening flat washers based on specific application requirements.
Key Consideration | Description | Best Applications |
Vibration Resistance | High-friction or micro-serration washers to prevent rotational loosening in environments with constant vibration. | Automotive, Machinery, Construction |
Corrosion Resistance | Coated or composite washers to withstand moisture, chemicals, or salt exposure. | Marine, Outdoor, Chemical Processing |
Load-bearing Capacity | Materials and design (e.g., wave shape) that maintain tension under varying load conditions. | Aerospace, Heavy Equipment, Industrial |
Temperature Stability | Wave spring or composite materials for environments with significant thermal expansion and contraction. | Electronics, Aerospace, Automotive |
Ease of Installation | Mechanical locking tabs or flexible designs for easy setup and secure fitting across different bolt sizes. | General Assembly, Heavy Machinery |
Material Compatibility | Choose materials that match or complement the surrounding assembly to avoid wear, galvanic corrosion, or damage. | Sensitive Assemblies, Precision Equipment |
Weight Requirements | Lightweight composite materials for applications where reducing weight is crucial without compromising anti-loosening features. | Aerospace, High-Performance Automotive |
Cost-Effectiveness | Balancing cost with essential features like coatings or serrations for the desired anti-loosening performance. | Mass Production, General Manufacturing |
Environmental Conditions | Selecting appropriate coatings, materials, or designs that can endure specific environmental factors (e.g., high humidity, extreme temperatures). | Marine, Outdoor Installations |
Long-term Durability | Washers with enhanced corrosion resistance, friction coatings, or adaptable designs to reduce maintenance needs. | Industrial Equipment, Infrastructure |
Future Directions in Anti-Loosening Flat Washer Technology
As technology advances, new directions are emerging for anti-loosening flat washers.
- Embedded Sensors for Tension Monitoring: With the integration of IoT, flat washers with embedded sensors could continuously monitor tension, alerting engineers to potential loosening in real-time.
- Self-Adjusting Designs: Development of materials that adapt to changing loads by altering their frictional or tension properties could make washers capable of adjusting to various stress levels without manual intervention.
- Additive Manufacturing for Custom Features: 3D printing enables the customization of washer geometry, creating application-specific customized washers that maximize anti-loosening features for high-stakes engineering projects.
These advancements point to a future where flat washers are not just static components but intelligent, adaptable, and optimized to meet the specific needs of their environments.
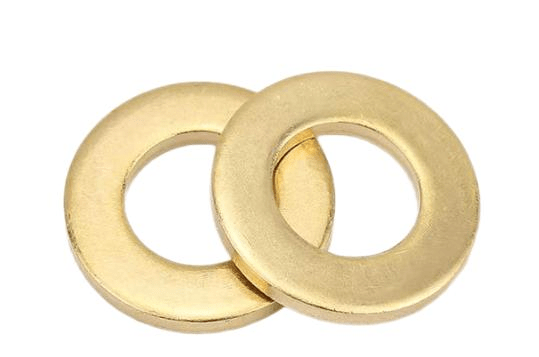
In summary, anti-loosening features in flat washers are a crucial innovation in modern engineering, enabling mechanical assemblies to withstand increasingly challenging environments. From micro-serrations and dual-layer coatings to integrated locking mechanisms and advanced materials, these advancements have expanded the applications of flat washers, making them essential in industries with stringent safety and durability standards.