High-temperature Bolts: Materials and How to Select
In engineering and industrial settings, bolts play a pivotal role in ensuring the structural integrity and reliability of assemblies. When it comes to high-temperature bolts, the choice becomes even more critical due to the demanding conditions that these fasteners must endure. These environments, typically found in industries such as aerospace, automotive, power generation, and manufacturing, require bolts that can withstand extreme heat without compromising their mechanical properties. This article explores the types of high-temperature bolts , the materials used, and key considerations for selecting the appropriate fasteners.
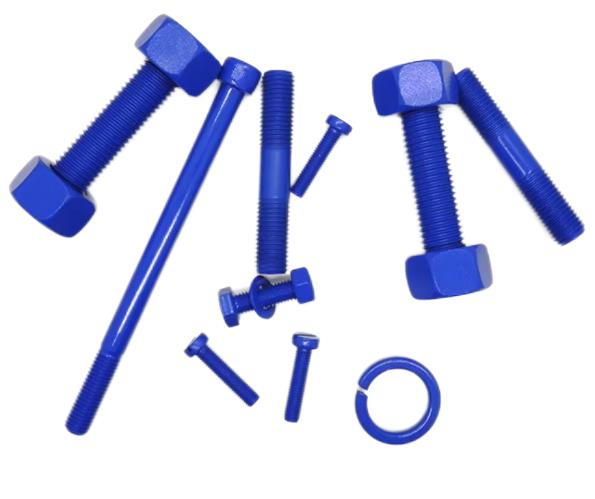
Understanding High-Temperature Environments
High-temperature environments are defined by operating temperatures that exceed 200°C (392°F), which can significantly affect the mechanical properties of materials. At elevated temperatures, metals can experience:
- Reduced tensile strength: Metals can become weaker and more prone to deformation.
- Oxidation and corrosion: High temperatures can accelerate these processes, leading to material degradation.
- Thermal expansion: Different materials expand at different rates, which can cause stress and potential failure if not properly accounted for.
- Creep: Prolonged exposure to high stress and temperature can cause permanent deformation over time.
Various Materials Used for High-temperature Bolts
1. Stainless Steels
Types and Properties
- 304 Stainless Steel: Known for its good corrosion resistance and moderate strength, 304 stainless steel can handle temperatures up to about 870°C (1600°F).
- 316 Stainless Steel: Offers better corrosion resistance, particularly against chlorides, and can withstand temperatures up to 800°C (1472°F).
- 321 Stainless Steel: Stabilized with titanium to improve resistance to intergranular corrosion, 321 stainless steel is suitable for temperatures up to 870°C (1600°F).
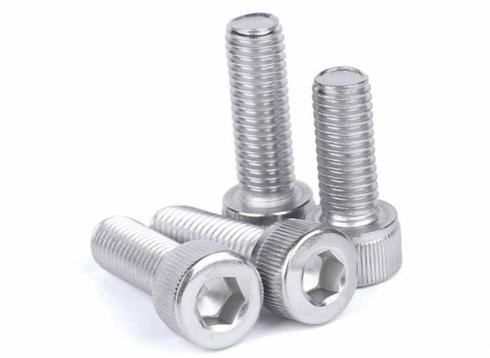
Advantages
- Excellent resistance to oxidation and corrosion.
- Readily available and relatively cost-effective.
- Good mechanical properties at moderate temperatures.
Applications
- Exhaust systems.
- Heat exchangers.
- Furnaces and boilers.
2. Alloy Steels
Types and Properties
- Inconel 718: A nickel-chromium alloy known for its high strength and resistance to oxidation and creep. It can operate at temperatures up to 700°C (1292°F).
- Incoloy 800: Another nickel-iron-chromium alloy, capable of withstanding temperatures up to 870°C (1600°F) while maintaining good strength and corrosion resistance.
Advantages
- Exceptional strength at high temperatures.
- Excellent resistance to oxidation, corrosion, and thermal fatigue.
- Maintains mechanical properties under extreme conditions.
Applications
- Gas turbines.
- Jet engines.
- Chemical processing equipment.
3. Titanium Alloys
Types and Properties
- Grade 5 Titanium (Ti-6Al-4V): The most commonly used titanium alloy, known for its high strength-to-weight ratio and ability to withstand temperatures up to 400°C (752°F).
- Grade 2 Titanium: While not as strong as Grade 5, it offers excellent corrosion resistance and can handle temperatures up to 315°C (600°F).
Advantages
- High strength-to-weight ratio.
- Excellent corrosion resistance.
- Good mechanical properties at elevated temperatures.
Applications
- Aerospace fasteners.
- Automotive performance parts.
- Marine environments.
4. Nickel-Based Alloys
Types and Properties
- Hastelloy X: Known for its outstanding high-temperature strength and oxidation resistance, suitable for temperatures up to 1200°C (2192°F).
- Nimonic 80A: A nickel-chromium alloy with excellent high-temperature strength and creep resistance, used up to 815°C (1500°F).
Advantages
- Superior performance in extreme temperatures.
- High resistance to oxidation and corrosion.
- Maintains mechanical integrity under thermal stress.
Applications
- Aerospace engines.
- Industrial furnace components.
- Nuclear reactors.
5. Ceramic and Composite Materials
Types and Properties
- Silicon Carbide (SiC): Known for its high thermal conductivity, low thermal expansion, and ability to withstand temperatures up to 1600°C (2912°F).
- Carbon-Carbon Composites: Extremely high strength and thermal stability, suitable for temperatures exceeding 2000°C (3632°F).
Advantages
- Can withstand ultra-high temperatures.
- Excellent thermal stability.
- High resistance to wear and chemical attack.
Applications
- Spacecraft heat shields.
- High-temperature furnaces.
- Aerospace structural components.
By understanding these materials and their applications, engineers and designers can make informed choices to enhance the reliability and durability of their high-temperature systems.
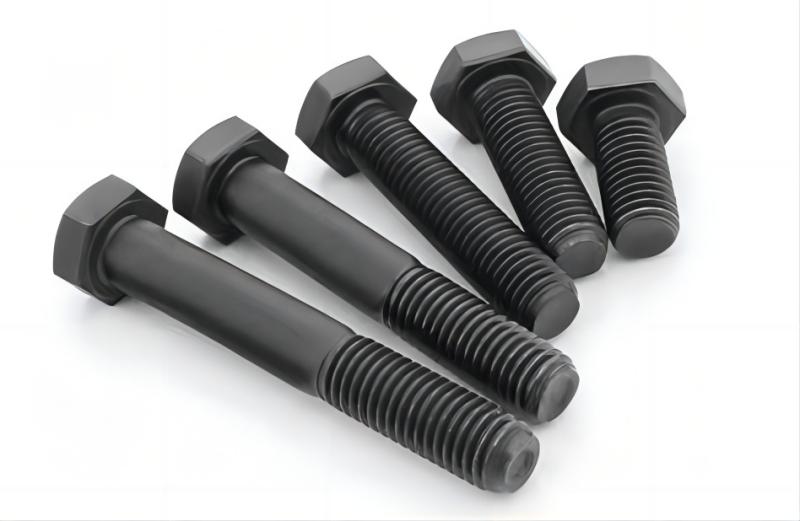
Key Considerations for Selecting High-temperature Bolts
Bolts used in high-temperature applications must meet stringent requirements to ensure the safety, performance, and longevity of the assemblies they secure. The selection process involves evaluating several key factors that influence the bolt’s ability to withstand extreme conditions without compromising its integrity.
1. Operating Temperature
- Maximum and Minimum Temperatures
- Maximum Temperature: Determine the highest temperature the bolt will be exposed to. This will guide the selection of materials capable of retaining their mechanical properties at these elevated temperatures.
- Minimum Temperature: In some applications, bolts must also perform well at low temperatures, where brittleness could be a concern.
- Temperature Fluctuations: Consider the range and frequency of temperature changes. Bolts must be able to endure thermal cycling without losing strength or suffering from fatigue.
2. Mechanical Properties
- Tensile Strength: The bolt material must have sufficient tensile strength to withstand the forces applied without failing, even at high temperatures where metals tend to weaken.
- Yield Strength: Ensure the bolt material has a high yield strength to prevent permanent deformation under load.
- Creep Resistance: In high-temperature applications, bolts are often subjected to continuous stress. Materials with good creep resistance will deform minimally over time, maintaining the assembly’s integrity.
- Toughness: The ability of a material to absorb energy and plastically deform without fracturing is crucial, especially if the bolts are subject to sudden impacts or dynamic loads.
3. Thermal Expansion
- Coefficient of Thermal Expansion (CTE): Different materials expand at different rates when heated. It’s essential to match the CTE of the bolt material with that of the components being joined to minimize thermal stress and potential failure.
- Joint Design Considerations: Account for differential thermal expansion in the design of the joint to prevent loosening or overstressing the bolts.
4. Corrosion and Oxidation Resistance
- Environmental Conditions: Evaluate the presence of corrosive elements like chemicals, moisture, or salt. Bolts in high-temperature applications often face accelerated oxidation and corrosion.
- Protective Coatings: Consider using bolts with protective coatings or selecting inherently corrosion-resistant materials (e.g., stainless steel, nickel alloys) to enhance longevity.
5. Manufacturing and Installation
- Fabrication Processes: Ensure the chosen material can be manufactured to the required specifications, including threading and heat treatments, without compromising its properties.
- Installation Procedures: Consider the ease of installation and any special requirements (e.g., torque settings, pre-loads) that ensure the bolt performs optimally in its high-temperature environment.
6. Cost and Availability
- Material Cost: High-performance materials like nickel alloys and titanium can be expensive. Assess the cost-benefit ratio considering the application’s demands and the criticality of bolt performance.
- Supply Chain: Ensure that the selected materials and bolts are readily available and that supply chain constraints will not impact the project timeline or maintenance schedules.
7. Standards and Certifications
- Industry Standards: Adhere to relevant industry standards and specifications (e.g., ASTM, ISO) for high-temperature bolts to ensure quality and performance.
- Certification Requirements: Some applications, particularly in aerospace and nuclear industries, may require bolts to meet specific certification requirements for safety and reliability.
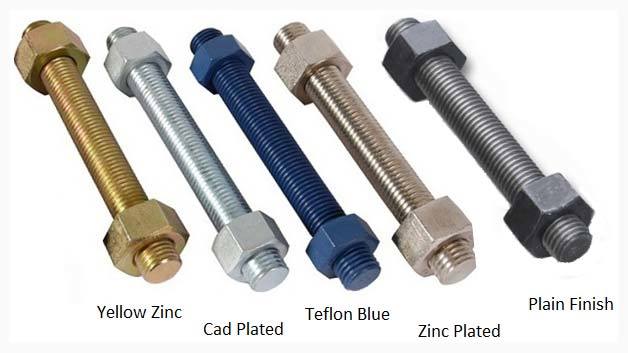
Conclusion
Understanding the operating environment, choosing the appropriate materials, and considering key mechanical properties are essential steps in ensuring the success of high-temperature bolts. By making informed choices, engineers and designers can enhance the performance and durability of their high-temperature applications.