How Rapid CNC Prototyping Changes the Prototypes Produce
In the fast-paced world of manufacturing and product development, the ability to quickly produce accurate prototypes is crucial. Rapid CNC prototyping has emerged as a critical technique, enabling designers and engineers to create high-precision prototypes swiftly. This article delves into the various rapid CNC prototyping techniques, their benefits, and their applications in modern industry.
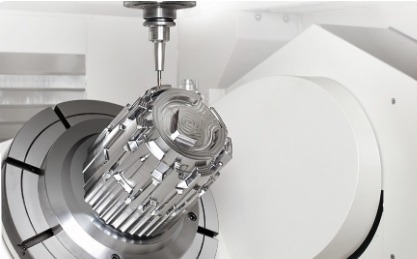
What is Rapid CNC Prototyping
Here’s a chart summarizing the basics of Rapid CNC Prototyping
Aspect | Description |
Definition | CNC prototyping involves using computer-controlled machines to create precise prototypes from digital designs rapidly. |
Process | Digital Design: Create a 3D model using CAD (Computer-Aided Design) software. |
Programming: Convert the CAD model into CNC machine instructions using CAM (Computer-Aided Manufacturing) software. | |
Machining: CNC machines execute the programmed instructions to cut, shape, and form the prototype from raw material. | |
Materials | Metals: Aluminum, steel, titanium, etc. |
Plastics: ABS, polycarbonate, nylon, etc. | |
Composites: Carbon fiber, fiberglass, etc. | |
Advantages | High Precision: Produces prototypes with tight tolerances and fine details. |
Speed: Rapidly transforms designs into physical models. | |
Repeatability: Ensures consistent production of multiple prototypes. | |
Versatility: Works with a variety of materials and complex designs. |
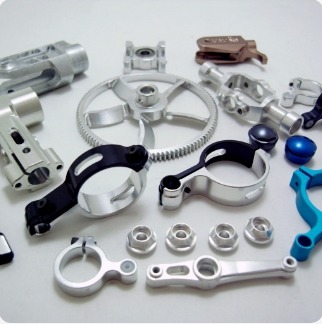
Key Rapid CNC Prototyping Techniques
1. High-Speed Machining (HSM)
- Overview: High-Speed Machining involves using higher spindle speeds and feed rates to significantly increase material removal rates. This technique reduces machining time while maintaining precision.
- Benefits: HSM reduces cycle times, minimizes tool wear, and improves surface finish, making it ideal for prototypes requiring fine details and smooth surfaces.
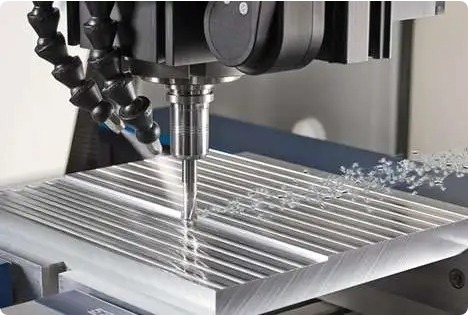
2. Multi-Axis Machining
Overview: Multi-axis CNC machines, such as 4-axis and 5-axis CNC machines, can move the cutting tool and the workpiece simultaneously along multiple axes. This capability allows for the creation of complex geometries and intricate parts that are challenging or impossible with traditional 3-axis machines.
Benefits: Multi-axis machining reduces the need for multiple setups and fixtures, enhancing speed and accuracy. It is particularly useful for producing parts with complex shapes and undercuts.

3. Adaptive Machining
- Overview: Adaptive machining uses real-time feedback and adjustments to optimize the cutting process. By monitoring tool wear, cutting forces, and other parameters, adaptive machining can dynamically adjust the toolpath and cutting conditions.
- Benefits: This technique enhances efficiency, prolongs tool life, and ensures consistent quality, making it ideal for rapid prototyping where precision and reliability are critical.
4. Trochoidal Milling
- Overview: Trochoidal milling involves using a circular toolpath to maintain a consistent cutting load on the tool. This technique allows for higher cutting speeds and deeper cuts without overloading the tool.
- Benefits: Trochoidal milling reduces heat buildup and tool wear, enabling faster material removal and improved surface finish. It is particularly effective for hard materials and deep pocket machining.
5. Peck Drilling
- Overview: Peck drilling is a technique where the drill bit is periodically retracted to clear chips and reduce heat buildup. This intermittent drilling process prevents the tool from overheating and breaking.
- Benefits: Peck drilling enhances drilling speed and precision, particularly in deep-hole drilling applications. It is useful for creating accurate and clean holes in prototypes.
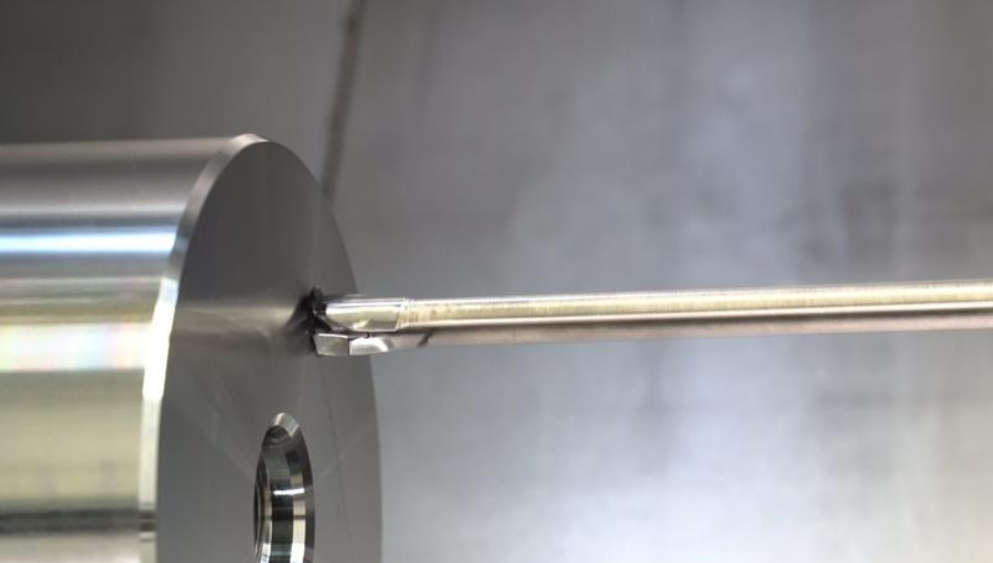
6. CNC Turning with Live Tooling
- Overview: CNC turning with live tooling allows for the integration of milling, drilling, and tapping operations into a single setup. The live tooling feature enables the machine to perform additional machining tasks while the workpiece is rotating.
- Benefits: This technique reduces the need for multiple setups and transfers between machines, significantly speeding up the prototyping process and improving overall efficiency.
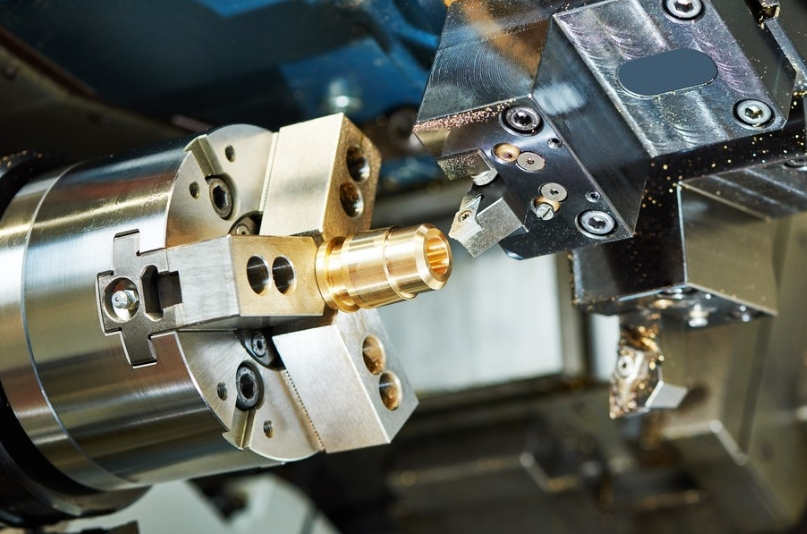
7. Micromachining
- Overview: Micromachining involves using CNC machines to create extremely small and precise features. It utilizes specialized tools and techniques to achieve high accuracy at microscopic scales.
- Benefits: Micromachining is essential for industries such as medical devices and microelectronics, where small and intricate components are required. It allows for rapid production of detailed prototypes with high precision.
8. Hybrid Manufacturing
- Overview: Hybrid manufacturing combines additive and subtractive processes in a single machine. CNC machines integrated with 3D printing technologies can build up a part layer by layer and then machine it to final specifications.
- Benefits: This approach leverages the strengths of both technologies, offering flexibility and precision in creating complex prototypes. It reduces lead times and material waste.
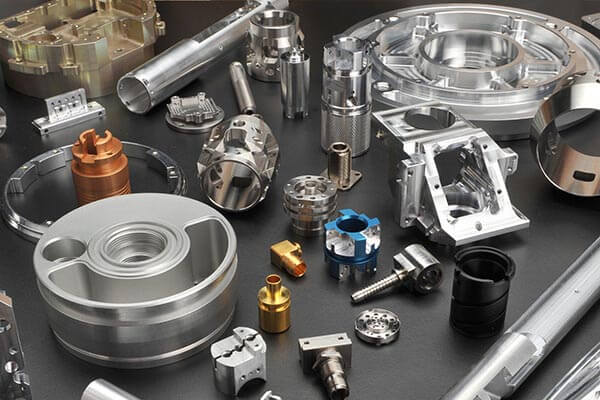
Applications of Rapid CNC Prototyping
1. Product Development and Design Validation
- Concept Models: Creating physical models from CAD designs to validate and refine concepts.
- Fit and Function Testing: Ensuring parts fit together and function as intended before mass production.
- Iterative Design: Quickly producing multiple iterations of a design to refine and improve products.
2. Custom Tooling and Fixtures
- Specialized Tools: Producing custom tools tailored to specific manufacturing processes.
- Jigs and Fixtures: Creating fixtures to hold parts in place during machining or assembly.
3. End-Use Parts Production
- Low-Volume Production: Manufacturing small batches of parts for niche markets or custom orders.
- Replacement Parts: Producing spare or replacement parts quickly without the need for mass production setups.
4. Aerospace and Automotive Industries
- Prototyping Complex Components: Creating prototypes of complex parts like turbine blades, engine components, and structural elements.
- Lightweight Structures: Producing lightweight and high-strength parts using advanced materials.
5. Medical and Healthcare
- Custom Implants: Manufacturing patient-specific implants and prosthetics.
- Surgical Tools: Produce custom surgical instruments tailored to specific procedures.
6. Consumer Electronics
- Device Enclosures: Rapidly prototyping housings for electronic devices.
- Component Prototyping: Testing the fit and functionality of components like buttons, connectors, and screens.
7. Robotics and Automation
- Custom Robot Parts: Manufacturing unique parts for robotic systems.
- End Effectors: Creating custom grippers and tools for robotic arms.
8. Architecture and Construction
- Scale Models: Producing detailed architectural models to visualize and plan construction projects.
- Custom Building Components: Fabricating unique elements like decorative panels, moldings, and structural supports.
9. Education and Research
- Educational Tools: Creating models and parts for educational purposes and research projects.
- Prototyping New Technologies: Enabling the development and testing of innovative technologies and materials.
10. Industrial Equipment
- Machine Components: Rapidly producing parts for industrial machinery and equipment.
- Maintenance Tools: Creating specialized tools for maintaining and repairing industrial systems.
Conclusion
Rapid CNC prototyping techniques are revolutionizing the way prototypes are developed and refined. By leveraging the precision, speed, and versatility of CNC machines, manufacturers can accelerate product development, reduce costs, and enhance the quality of their prototypes.