How to Do A Good Job In Metal Stamping Parts Quality Control
Metal stamping parts are a critical component of many industrial products, from automobiles and appliances to aerospace and medical devices.So ensuring the performance and reliability of metal stamping parts is essential. This is where metal stamping parts quality control comes in, a process that involves a range of measures designed to verify the quality of these parts and identify and resolve any issues that could affect their performance.
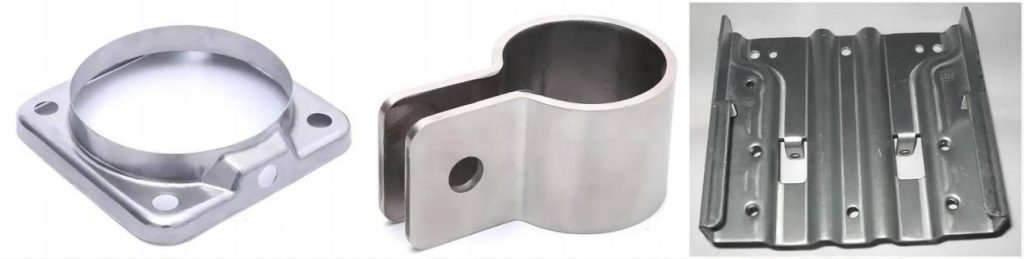
Common Quality Control Methods for Metal Stamping Parts
To ensure the quality of metal stamping parts, a variety of quality control methods are typically employed. These measures include inspection methods, testing methods, and certification and compliance requirements.
Inspection methods for metal stamping parts involve visually inspecting for defects or imperfections. This can include checking for surface flaws, dimensional deviations, or other anomalies that could affect the performance of the part. Dimensional inspection, in particular, is a critical component of metal stamping parts quality control, as even minor deviations from the required specifications can result in significant performance issues or failures.
Testing methods are used to verify the mechanical properties and characteristics of metal stamping parts, such as their tensile strength, hardness, or corrosion resistance. Common testing methods include tensile testing, which measures the amount of force a part can withstand before breaking, hardness testing, which measures a part’s resistance to indentation, and corrosion testing, which measures a part’s resistance to corrosion and degradation over time.
Certification and compliance requirements are also an important aspect of metal stamping parts quality control. Many industries have specific quality standards or regulatory requirements that must be met to ensure the safety and performance of products. For example, ISO 9001 is a widely recognized quality management standard that requires companies to establish and maintain a quality management system, while AS9100 is a standard specifically designed for the aerospace industry. Other compliance requirements may include RoHS, a directive that restricts the use of certain hazardous substances in electrical and electronic equipment.
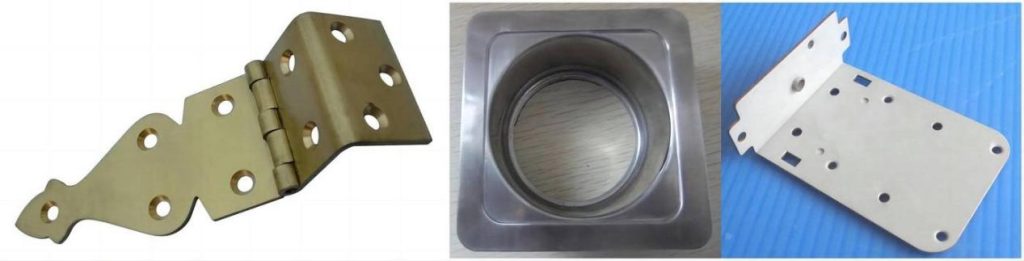
Factors Affecting Quality Control of Metal Stamping Parts
There are a number of factors that can affect metal stamping parts quality control. These factors include material selection and characterization, manufacturing processes and equipment, and design considerations.
Material selection and characterization is critical to ensuring the performance and reliability of metal stamping parts. The material used for a metal stamping part must be selected based on its properties, such as its strength, ductility, and corrosion resistance, and must be verified to meet these specifications. This can involve testing the material for mechanical properties, as well as conducting chemical analysis to verify its composition.
Manufacturing processes and equipment are also important considerations in metal stamping parts quality control. Manufacturing processes must be carefully monitored and controlled to ensure consistent quality, and equipment must be calibrated and maintained to ensure accurate results. This can involve implementing statistical process control techniques, such as control charts and process capability analysis, to identify and control variation in the manufacturing process.
Design considerations are also critical to ensuring stamping parts quality control, especially for the custom metal stamping. Parts must be designed for manufacturability, taking into account the capabilities of the manufacturing process and the materials being used. Designers must also consider the impact of quality control measures on the design, such as incorporating features that make inspection or testing easier or more effective.
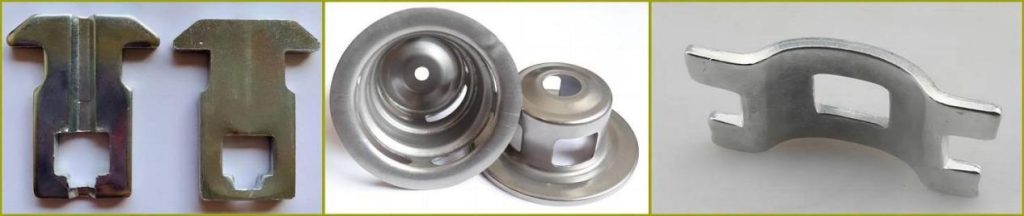
Best Practices For Metal Stamping Parts Quality Control
To ensure the best possible results in metal stamping parts quality control, a number of best practices can be implemented. These practices include implementing a quality management system, conducting regular audits and reviews, and investing in employee training and education.
Implementing a quality management system (QMS) is an essential component of metal stamping parts quality control. A QMS is a structured approach to managing quality, and involves establishing policies, procedures, and processes to ensure consistent quality across all aspects of the organization. A QMS can help ensure that quality control measures are being implemented effectively and consistently, and can also provide a framework for continuous improvement.
Conducting regular audits and reviews is also essential for metal stamping parts quality control. Regular audits can help identify areas for improvement and ensure that quality control measures are being implemented effectively. Reviews can also help ensure that the organization is meeting its quality objectives and that the QMS is functioning as intended.
Investing in employee training and education is another critical component of metal stamping parts quality control. By providing employees with the knowledge and skills they need to implement quality control measures effectively, stamping parts manufacturers can ensure that quality is built into every aspect of the manufacturing process. This can include training on inspection and testing techniques, as well as training on the QMS and other quality-related processes.
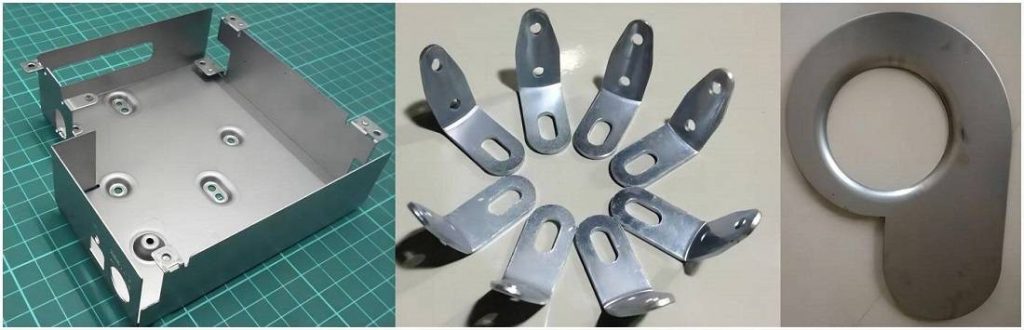
Case Studies and Success Stories Of Metal Stamping Parts Quality Control
There are many examples of companies that have successfully implemented metal stamping parts quality control methods and improved their products and processes. For example, automotive stamping parts supplier was able to reduce the number of quality issues in its stamping parts production by 50% through the implementation of a comprehensive quality management system. This included the use of statistical process control techniques and employee training and education programs.
Another success story comes from the aerospace industry, where a manufacturer was able to reduce the number of defects in its stamping parts production by 80% through the implementation of a rigorous quality control program. This included the use of advanced inspection and testing techniques, as well as the implementation of a QMS that emphasized continuous improvement.

Conclusion
In conclusion, metal stamping parts quality control is a critical aspect of ensuring the performance and reliability of these important components. By implementing a range of quality control measures, including inspection methods, testing methods, and certification and compliance requirements, metal stamping parts manufacturers can ensure that their products meet the required specifications and perform as intended. By considering factors such as material selection and characterization, manufacturing processes and equipment, and design considerations, stamping parts manufacturers can further improve the effectiveness of their quality control measures. By implementing best practices such as a quality management system, conducting regular audits and reviews, and investing in employee training and education, organizations can ensure that quality is built into every aspect of the manufacturing process. Through case studies and success stories, we can see the benefits of these practices in action, and how they can help stamping parts manufacturers improve their products and processes and stay competitive in today’s market.