How to Extend the Lifespan of Tungsten Steel Milling Cutters
Tungsten steel milling cutters are essential tools in precision machining industries, known for their durability, hardness, and ability to cut through tough materials like steel, alloys, and high-temperature alloys. However, despite their robustness, improper usage, maintenance, and environmental factors can reduce their lifespan. To get the most out of these cutting tools and maximize their performance, it’s essential to follow best practices in handling, operation, and care.
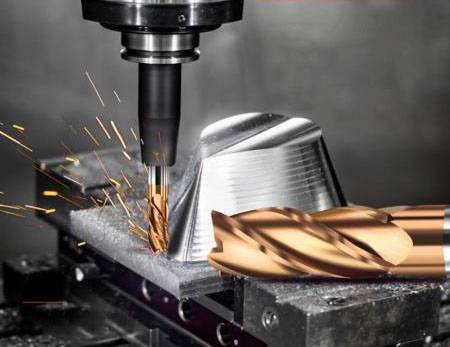
Understanding Tungsten Steel Milling Cutters
Tungsten steel milling cutters are high-performance cutting tools made from a tungsten carbide alloy. These cutters are commonly used in machining and milling operations to cut and shape various materials, including metals, alloys, and non-metals. Tungsten steel milling cutters offer superior durability, heat resistance, and sharpness, making them ideal for high-speed machining, and producing accurate and smooth finishes. Their robust performance extends tool life, enhancing productivity, and reducing the need for frequent tool changes in demanding industrial applications.
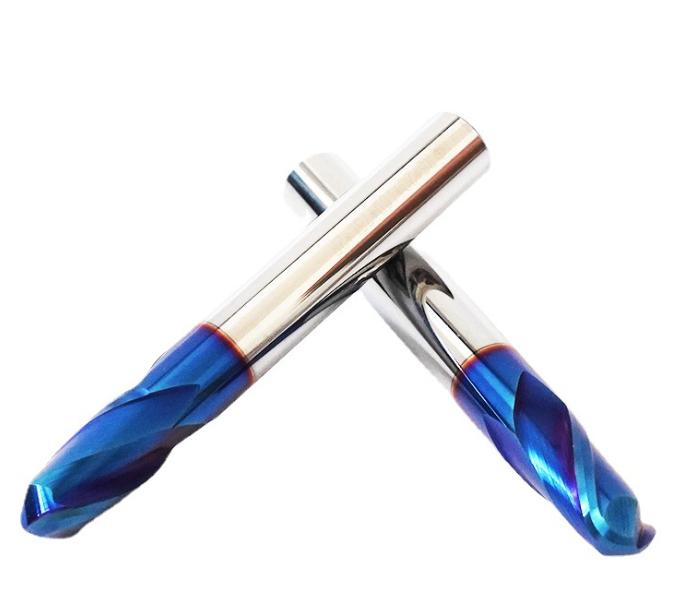
Key Factors Affecting the Life of Tungsten Steel Milling Cutters
This chart outlines the main factors that influence the durability and performance of tungsten steel milling cutters.
Factor | Description | Impact on Tool Life |
Cutting Speed & Feed Rate | Proper speed and feed are crucial for minimizing heat and tool wear. | Excessive speed causes overheating, while low speed reduces efficiency, both shortening tool lifespan. |
Material Compatibility | Using the correct tool coating and geometry for specific materials. | Increases tool efficiency and durability when matched properly; mismatching leads to faster wear. |
Lubrication & Cooling | Regular application of cutting fluids or air cooling. | Reduces heat buildup, preventing tool wear and extending the lifespan of the cutter. |
Tool Maintenance | Regular sharpening and inspection of the cutting edge for wear or chipping. | Keeps the tool in optimal condition; failure to maintain can result in faster tool degradation. |
Vibration & Runout | Ensuring proper machine alignment and tool holder stability to minimize vibration and runout. | Excessive vibration or tool runout leads to uneven wear and premature tool failure. |
Depth of Cut | Optimizing the depth of each pass to match material hardness and tool size. | Reducing excessive cuts decreases tool strain, improving its lifespan. |
Tool Storage | Proper storage to avoid corrosion and physical damage. | Prevents deterioration and accidental damage to the cutting edges, ensuring longer use. |
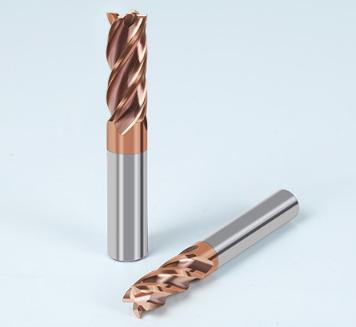
Key Strategies for Extending the Lifespan of Tungsten Steel Milling Cutters
1. Proper Tool Selection for the Job
The first step to extending the life of tungsten steel end mills is selecting the right tool for the specific application. Choosing a cutter with the appropriate cutting geometry, coating, and diameter based on the material being machined is essential for efficient performance.
- Cutting Geometry: Opt for cutters with optimized cutting angles, helix designs, and tooth profiles for the material you are machining. Different materials, like stainless steel or titanium, require specific cutter designs to reduce stress on the tool.
- Coatings: Coated tungsten carbide milling cutters often outperform uncoated ones. Choose coatings like Titanium Nitride (TiN), Titanium Carbon Nitride (TiCN), or Aluminum Titanium Nitride (AlTiN), which can improve wear resistance, reduce friction, and extend tool life in high-heat applications.
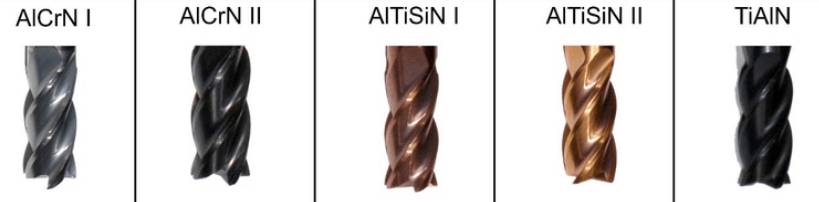
2. Use Appropriate Cutting Parameters
Using the correct cutting parameters is crucial in preserving the tool’s longevity. Incorrect speed, feed rate, or depth of cut can cause excessive wear, heat buildup, and even tool breakage.
- Cutting Speed: Lower cutting speeds generate less heat and minimize tool wear, particularly for hard materials. Use manufacturer-recommended speeds for the material being machined to avoid overheating the tool.
- Feed Rate: Excessive feed rates increase pressure on the tool, leading to chipping or breaking. Moderate feed rates provide balanced cutting forces and protect the tool.
- Depth of Cut: Avoid deep cuts that exert too much force on the milling cutter. Instead, take smaller incremental cuts that reduce the load on the tool and minimize stress.
3. Optimize Coolant Usage
Overheating is a major contributor to tool wear, especially in tungsten carbide milling cutters, which are sensitive to extreme temperatures. Proper cooling or lubrication is critical to avoid excessive heat buildup during cutting.
- Coolants: Use high-quality coolants or cutting fluids that are appropriate for the material being machined. Coolants not only prevent overheating but also flush chips away, reducing friction between the cutter and workpiece.
- Application: Ensure that coolants are applied directly to the cutting zone in sufficient quantities. Inadequate coolant flow can lead to thermal stress on the tool and shortened tool life.
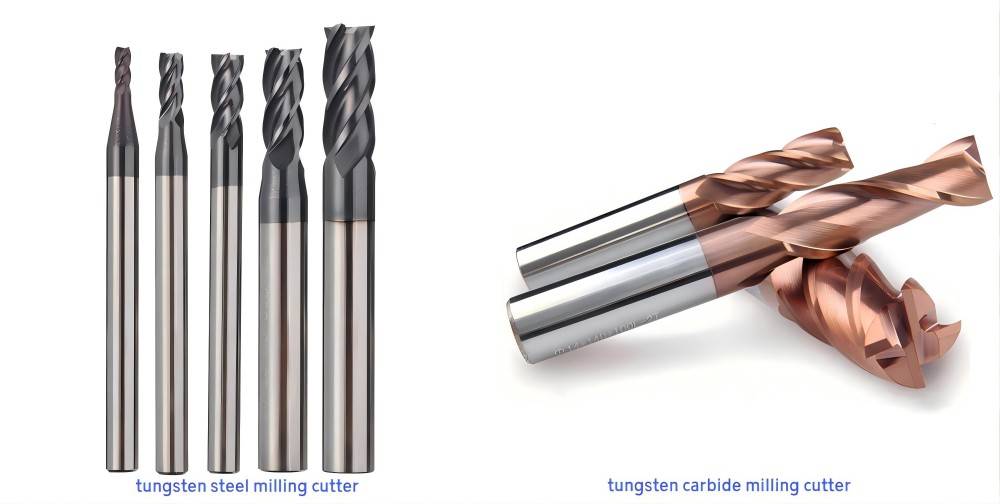
4. Regular Inspection and Tool Maintenance
Routine inspection and maintenance are key to identifying early signs of wear and preventing unexpected tool failure. Regular maintenance also ensures peak performance.
- Visual Inspection: Frequently inspect the cutting edges of the tool for signs of wear, chipping, or rounding. Replace cutters before they become severely worn to maintain optimal performance and avoid damaging the workpiece.
- Tool Sharpening: Sharpening the tool regularly can extend its life by restoring the cutting edge. Avoid over-sharpening, as removing too much material can weaken the tool.
- Proper Storage: Store tungsten steel end mills in a dry, clean environment, ideally in individual cases or holders to prevent chipping or dulling of cutting edges.
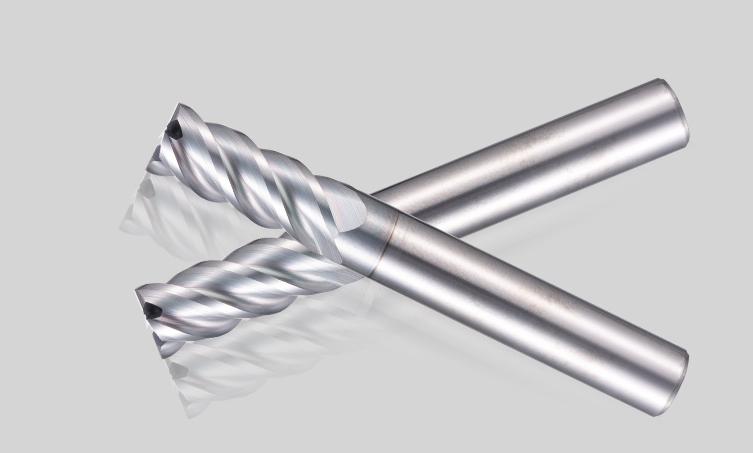
5. Minimize Vibration and Runout
Vibration and tool runout can significantly affect tool life by causing uneven wear on the cutter and negatively impacting machining precision.
- Machine Stability: Ensure that the machine being used for milling is well-maintained and stable, minimizing vibrations during operation.
- Tool Holder Quality: Use high-quality tool holders and ensure that the tool is properly secured to prevent runout, which can cause uneven wear and breakage.
- Balanced Operation: Employ balanced cutting strategies, such as climb milling, which reduces vibrations and promotes smoother cuts compared to conventional milling.
6. Use Advanced Monitoring Systems
Adopting modern monitoring systems can help detect tool wear in real-time, allowing operators to take corrective action before the tool is damaged beyond use.
- Tool Wear Sensors: Some advanced CNC machines are equipped with tool wear sensors that monitor the cutter’s performance, detecting changes in vibration, sound, or cutting force that indicate wear.
- Predictive Maintenance Software: Utilize predictive maintenance software that tracks tool usage and alerts operators when tools are nearing the end of their operational life, allowing for timely replacements and avoiding unexpected tool failure.
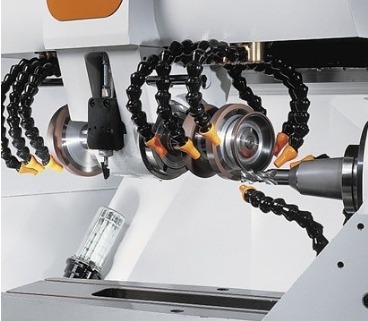
By following these best practices including maintaining optimal cutting speeds, using proper lubrication, conducting regular maintenance, and optimizing cutting conditions, manufacturers can significantly extend the lifespan of tungsten steel milling cutters. This not only reduces tool replacement costs but also improves machining efficiency and product quality.