How to Improve the Corrosion Resistance of Washers?
Table of Contents
Washers play a vital role in numerous applications, providing load distribution, reducing wear, and preventing leakage in bolted connections. However, when exposed to harsh environments, washers can be prone to corrosion, which compromises their performance and longevity. Improving the corrosion resistance of washers is essential to ensure the reliability and durability of mechanical systems.
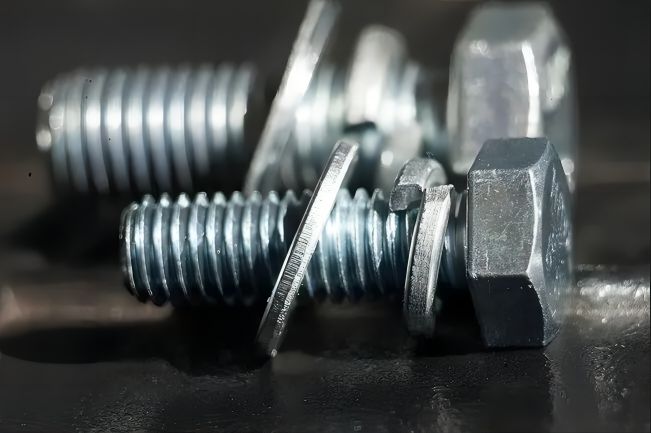
Why Need Improving the Corrosion Resistance of Washers
Here are key reasons why improving the corrosion resistance of washers is essential for ensuring long-term reliability and performance of washers in various applications.
- Extended Lifespan: Corrosion-resistant washers last longer, reducing the need for frequent replacements.
- Cost Savings: Prevents costly repairs, equipment downtime, and frequent washer replacements due to corrosion.
- Improved Safety: Reduces the risk of washer failure in critical applications, enhancing overall system safety.
- Maintains Structural Integrity: Corrosion can weaken washers, compromising the integrity of bolted connections in mechanical systems.
- Reduced Maintenance Requirements: Corrosion-resistant washers require less frequent inspections and upkeep, lowering maintenance costs.
- Ensures Reliability in Harsh Environments: Enhances performance in environments exposed to moisture, chemicals, or extreme weather conditions.
- Prevents System Contamination: Corroded washers can release particles or debris, potentially contaminating sensitive systems.
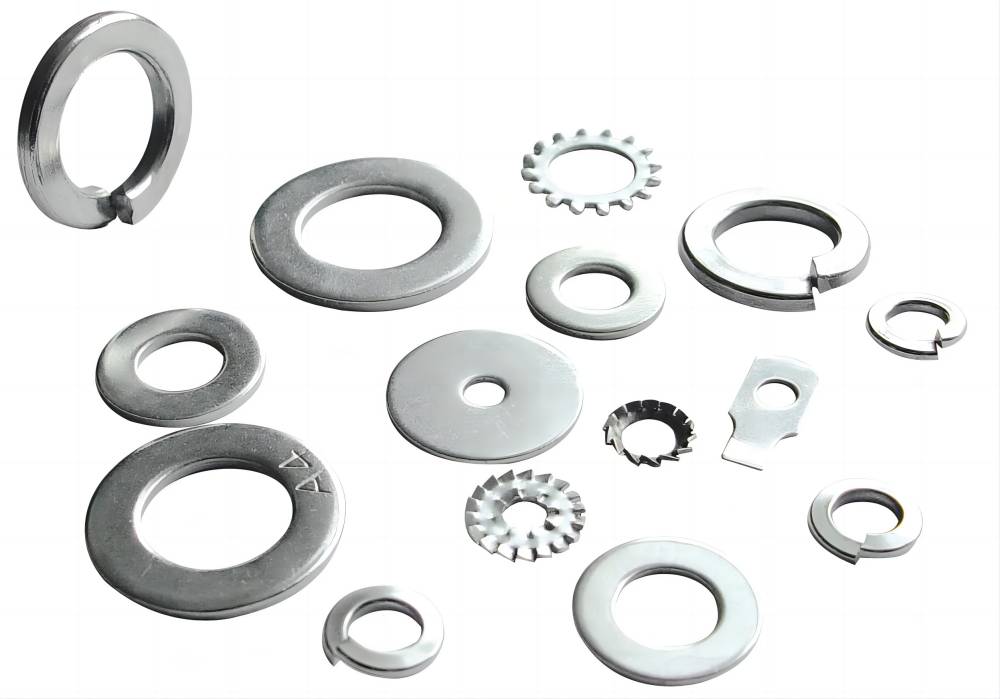
Effective Strategies to Improve the Corrosion Resistance of Washers
1. Material Selection
Choosing the right material for washers is the first and most critical step in improving corrosion resistance. Different materials offer varying levels of resistance to corrosion, depending on their chemical properties and the environment they are used in. Some common materials known for their excellent corrosion resistance include:
- Stainless Steel: Stainless steel washers, particularly those made from grades 304 and 316, are highly resistant to corrosion due to their chromium content. They form a passive oxide layer that protects the surface from further damage.
- Brass: Brass washers are suitable for applications where exposure to water and moisture is prevalent. They exhibit strong resistance to corrosion, especially in marine environments.
- Copper Alloys: Copper alloys, like bronze, offer excellent resistance to corrosion in seawater, making them ideal for use in coastal or marine settings.
- Plastics and Composites: Non-metallic washers made from plastics such as nylon or PTFE (polytetrafluoroethylene) are also corrosion-resistant and are ideal for non-conductive applications.
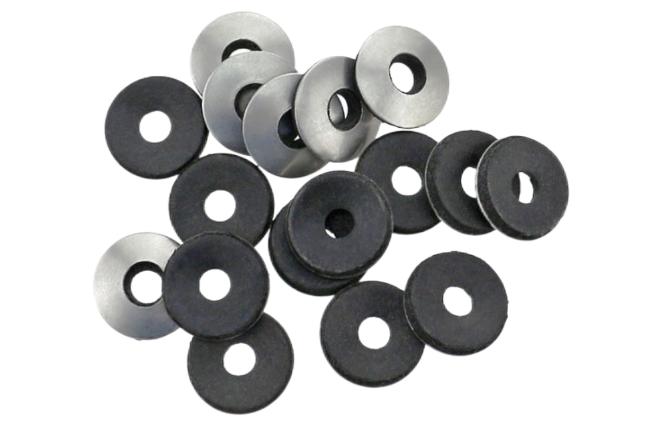
2. Protective Coatings
Applying protective coatings is an effective way to enhance the corrosion resistance of washers. These coatings act as a barrier, preventing the washer from coming into direct contact with corrosive elements.
This chart highlights the key coating techniques used to improve the corrosion resistance of washers, along with their advantages and typical applications.
Coating Technique | Description | Advantages | Applications |
Zinc Plating | A thin layer of zinc is electroplated onto the washer. | Sacrificial protection; cost-effective; provides basic corrosion resistance. | Automotive, construction, and general industrial use. |
Hot-Dip Galvanizing | Washers are dipped in molten zinc, forming a thick, durable zinc coating. | Excellent corrosion protection; ideal for outdoor and harsh environments. | Outdoor equipment, marine, and construction. |
Nickel Plating | Nickel is deposited onto the washer’s surface, forming a strong protective layer. | Offers strong corrosion resistance and improved hardness; aesthetically pleasing. | Aerospace, electronics, and chemical processing. |
Chrome Plating | A layer of chromium is electroplated onto the washer’s surface. | Provides excellent corrosion resistance, hardness, and a shiny finish. | Automotive, decorative applications, and high-wear parts. |
Phosphate Coating | A conversion coating that forms a protective layer of phosphate crystals. | Improves corrosion resistance and provides better adhesion for paints and lubricants. | Automotive parts, machinery components, and fasteners. |
Organic Coatings | Polymer-based coatings such as paints or epoxy are applied to the washer. | Highly versatile, resistant to chemicals, and enhances corrosion resistance in extreme conditions. | Industrial equipment, marine, and chemical industries. |
PTFE Coating | Polytetrafluoroethylene (PTFE) creates a non-stick and corrosion-resistant surface. | Excellent chemical resistance reduces friction and resists corrosive substances. | Food processing, medical devices, and chemical plants. |
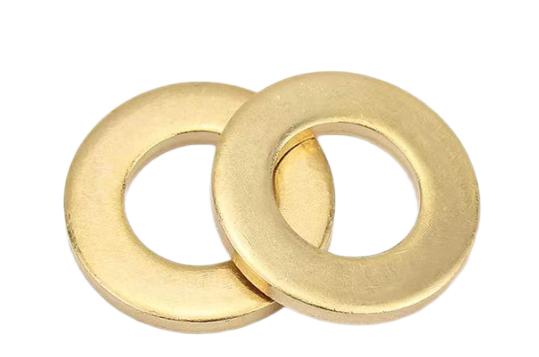
3. Heat Treatment
Heat treatment processes such as annealing and tempering can be used to modify the microstructure of the washer material. These processes help improve the mechanical properties of the washer, such as its resistance to corrosion cracking and stress corrosion. Heat-treated washers, especially those made from steel alloys, are more resilient against environmental degradation.
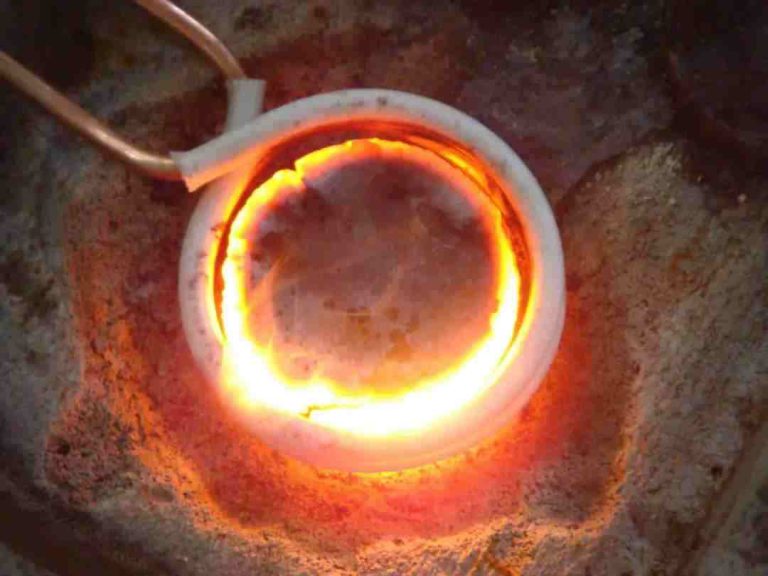
4. Corrosion-Resistant Alloys
For washers exposed to extreme conditions, opting for corrosion-resistant alloys can provide enhanced performance. Alloys such as Inconel, Hastelloy, and Monel offer high levels of corrosion resistance in aggressive chemical environments. These alloys are commonly used in washers for petrochemical, marine, and aerospace applications.
5. Surface Treatments
Surface treatments such as passivation, electro-polishing, or anodizing can improve corrosion resistance by modifying the washer’s surface properties.
This chart provides an overview of surface treatments designed to enhance the corrosion resistance of washers, their benefits, and typical applications across various industries.
Surface Treatment | Description | Advantages | Applications |
Passivation | A chemical process that removes free iron from the surface, enhancing the oxide layer. | Increases corrosion resistance of stainless steel; prevents rust formation. | Medical devices, aerospace, and food processing. |
Electro-polishing | A process that removes a thin layer of material from the washer’s surface, smoothing it. | Creates a smooth surface, reduces crevices where corrosion could start; improves aesthetic appearance. | Pharmaceutical, semiconductor, and food industries. |
Anodizing | An electrolytic process that thickens the oxide layer on aluminum washers. | Provides excellent corrosion resistance and wear protection; allows dyeing for color identification. | Aerospace, electronics, and architectural applications. |
Black Oxide Coating | A chemical conversion coating that forms a black oxide layer on steel surfaces. | Provides mild corrosion resistance; enhances appearance and reduces glare; offers slight wear resistance. | Tools, fasteners, and firearms. |
Nitriding | A heat treatment that diffuses nitrogen into the surface of washers, hardening them. | Improves wear resistance and fatigue strength; enhances corrosion resistance in certain environments. | Automotive, aerospace, and heavy machinery components. |
Carburizing | A heat treatment that introduces carbon into the washer’s surface to improve hardness. | Increases surface hardness and wear resistance; can help reduce corrosion when combined with coatings. | Gears, fasteners, and high-stress mechanical components. |
Plasma Electrolytic Oxidation (PEO) | An electrochemical surface treatment for metals, primarily aluminum and magnesium. | Produces a ceramic-like oxide coating, offering superior corrosion and wear resistance. | Aerospace, automotive, and marine industries. |
Shot Peening | A process that bombards the washer surface with small spheres to induce compressive stress. | Improves fatigue strength and corrosion resistance by creating a tougher surface. | Springs, gears, and high-stress components in engines. |
6. Environmental Control
The environment in which washers are used plays a significant role in their corrosion resistance. Controlling environmental factors can reduce the likelihood of corrosion. Here are some key considerations:
- Limiting Moisture Exposure: Storing washers in a dry environment and reducing exposure to water or high humidity levels can help minimize corrosion.
- Avoiding Contact with Dissimilar Metals: In applications where different types of metals are in contact, galvanic corrosion can occur. Insulating materials or washers made from compatible materials should be used to prevent this type of corrosion.
- Use of Corrosion Inhibitors: Applying corrosion inhibitors, such as lubricants or anti-corrosion sprays, can create an additional protective layer on washers used in corrosive environments.
7. Regular Inspection and Maintenance
Corrosion is a progressive process, and early detection can prevent significant damage. Regular inspection and maintenance of washers and fasteners can help identify signs of corrosion before it becomes a serious issue. Replacing corroded washers with corrosion-resistant alternatives ensures the ongoing performance of mechanical systems.
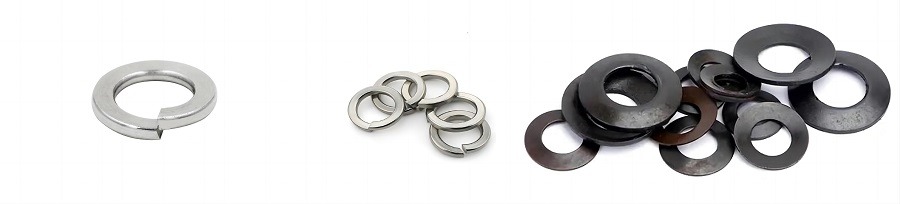
Through implementing these strategies, the lifespan and performance of washers in corrosive environments can be significantly enhanced, leading to more reliable and durable mechanical assemblies.