How to Use Self-Drilling Screws
Table of Contents
Self-drilling screws are an efficient and convenient fastening tool widely used in construction, home improvement, and industrial applications due to their ability to secure materials quickly without pre-drilling. In this post, we will provide a detailed guide on how to use self-drilling screws correctly and highlight other noteworthy features. Let’s explore what makes them unique!
Part 1. What is Self-Drilling Screws?
Self-drilling screws are specially designed fasteners with a tip shaped like a drill bit, allowing them to penetrate materials directly and create matching threads without the need for additional drilling or tapping.
These screws are suitable for various materials such as metal, wood, and plastic, and are commonly used for metal sheet connections, wood structure assembly, and lightweight fastening tasks in home improvement projects.
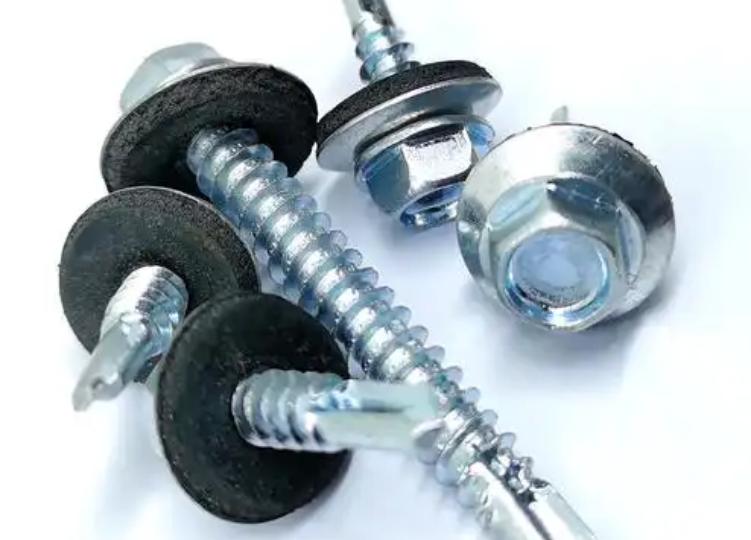
Part 2. Types of Self-Drilling Screws
Self-drilling screws come in various types, designed to meet specific requirements and applications.
1. Countersunk Self-Drilling Screws
With a countersunk head design, countersunk self-drilling screws sit flush or slightly below the surface of the material after installation, making them ideal for smooth surfaces, such as furniture assembly or decorative panel fixing.
2. Hex-Head Self-Drilling Screws
Hex-head self-drilling screws are compatible with power tools for quick tightening. They are commonly used in metal roofing, wall panels, and other applications that require anti-slip performance.
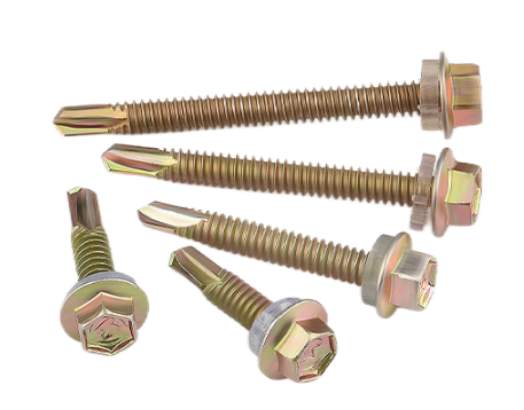
3. Coated Self-Drilling Screws
With special surface coatings, coated self-drilling screws offer superior corrosion resistance, suitable for chemical plants, coastal buildings, and similar environments.
4. Winged Self-Drilling Screws
Designed with small wings near the drill tip, winged self-drilling screws help enlarge the hole diameter, ensuring that softer materials are not damaged during penetration. They are commonly used for connecting metal and wood.
5. Pan-Head Self-Drilling Screws
Pan-head self-drilling screws have a pan-shaped head that provides a larger bearing surface, making them suitable for securing thin materials without pulling through the screw head.
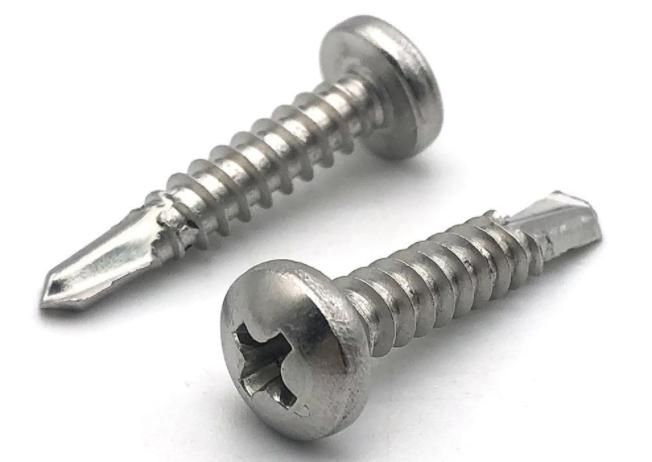
Part 3. Why Use Self-Drilling Screws?
Self-drilling screws have become indispensable fastening tools in construction, home improvement, and industrial fields due to their unique design and broad applicability. Here are some reasons for choosing self-drilling screws:
1. No Need for Pre-Drilling, Saving Construction Time
The tip of a self-drilling screw is designed like a drill bit, allowing it to penetrate materials and create threads directly, eliminating the need for additional pre-drilling steps.
This all-in-one functionality simplifies the process significantly and greatly enhances construction efficiency, especially in large-scale projects.
2. Versatile and Suitable for Multiple Materials
Self-drilling screws are compatible with a variety of materials, including metal, wood, and plastic. They can perform tasks such as connecting metal sheets, assembling wooden structures, and fastening lightweight plastic. A single type of screw can meet multiple needs, reducing inventory complexity.
3. Easy Installation, Reducing Labor Intensity
Since self-drilling screws do not require tool changes or additional drilling equipment, users can secure them with electric or manual tools directly. This significantly simplifies and reduces construction complexity and labor intensity.
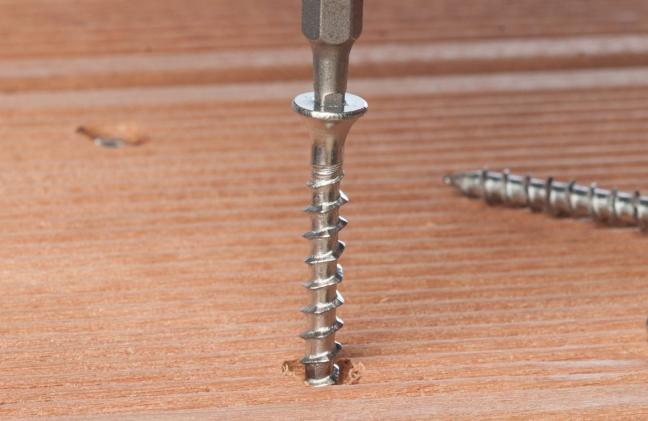
4. Stable Fastening Performance
The self-drilling screw thread design provides excellent grip, ensuring strong fastening for thin metal sheets or thick wood. Their unique anti-loosening properties also maintain stability in vibrating environments.
5. Durability in Various Environments
Many self-drilling screws undergo special surface treatments, such as galvanization, stainless steel, or coating processes, to withstand long-term use in humid, high-temperature, or chemically corrosive environments, extending their service life.
6. Diverse Designs to Meet Different Needs
Self-drilling screws come in various designs, including countersunk heads, hex heads, and winged types, to suit different installation scenarios. Users can select the most suitable screws based on specific requirements.
7. Cost-Effective and Economical
Compared to traditional screws that require pre-drilling, self-drilling screws reduce the need for additional tools and personnel while reducing construction time. This significantly reduces overall costs, making them particularly advantageous for large-scale projects that require bulk usage.
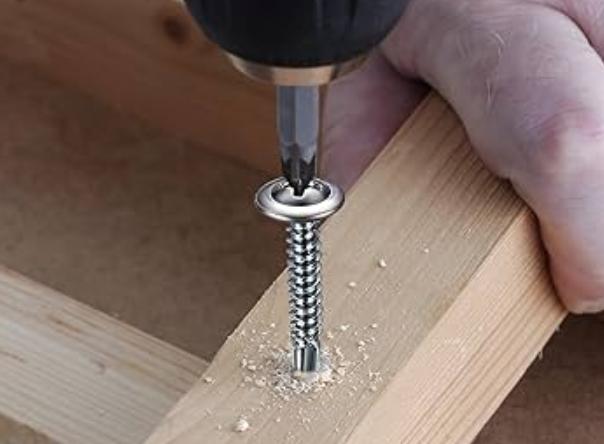
Part 4. How to Use Self-Drilling Screws?
When using self-drilling screws, follow these steps to ensure a secure connection:
Step 1. Choose Right Tools and Screws
The first step of using self-drilling screw is to select the appropriate length and diameter of self-drilling screws based on material thickness, and use a variable-speed drill or electric screwdriver for installation.
Step 2. Position Self-Drilling Screw
Then, you should ensure that the tip of the screw is parallel to the surface of the material to prevent slipping during drilling.
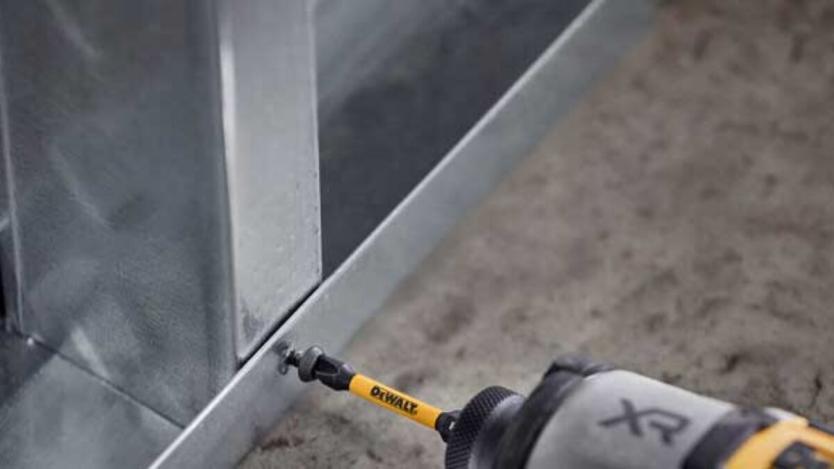
Step 3. Apply Slow Force to Start Drilling
In the initial stage, you should use low speed and moderate pressure to gradually allow the screw tip to penetrate the material.
Step 4. Gradually Increase Speed
Once the screw is fully inserted into the material, increase the speed to drill quickly, but avoid tightening as this could damage the threads.
Step 5. Check the Fastening Effect
Make sure the screw head is flush with or slightly embedded in the material to ensure a secure connection without damaging the material.
Part 5. Considerations When Using Self-Drilling Screws
1. Drill Bit Material
The performance of the self-drilling screw is directly impacted by the material of the drill bit. Choosing the right material is crucial.
- Stainless steel screws: Suitable for humid or corrosive environments and offer strong corrosion resistance.
- Carbon steel screws: More economical but require proper corrosion protection for use in damp conditions.
2. High-Temperature Stability
Due to friction, the drill bit generates high heat during prolonged use. Choosing screws with high-temperature stability for better performance in high-temperature environments can extend the screw’s lifespan. This is particularly important when fastening metal materials, as excessive heat can cause premature wear of the screw.
3. Drilling Temperature
It is essential to avoid drilling too quickly, which can cause materials to deform due to excessive heat, particularly for heat-sensitive materials like plastic. It is recommended to maintain a moderate speed and pressure to prevent damage to the material.
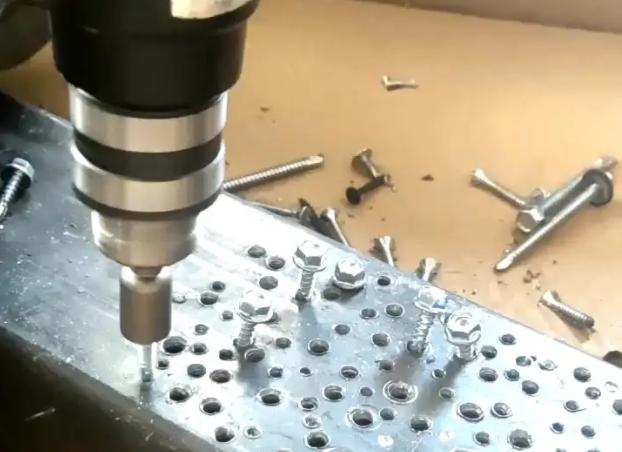
4. Applied Pressure
To ensure the screw is securely drilled, it’s important to use the appropriate pressure. Excessive pressure may damage the screw or material, while insufficient pressure could cause the screw to fail to fully drill or the drill bit to misalign. It is suggested to start with a lower speed and moderate pressure, gradually increasing the speed.
5. Revolutions Per Minute (RPM)
Different materials require different RPMs. The correct speed improves work efficiency and reduces the risk of screw damage.
- Metal materials: Use a lower speed (800-1200 RPM) to reduce excessive friction and screw damage.
- Wood or plastic: Higher speeds (above 1500 RPM) can be used to speed up the drilling process, without harming the material.
6. Choose the Right Screw Material
Selecting the appropriate screw material for the working environment is crucial for optimal performance.
- Stainless steel self-drilling screws: Ideal for use in humid or corrosive environments.
- Carbon steel screws: Suitable for indoor or dry environments, but requires additional corrosion protection.
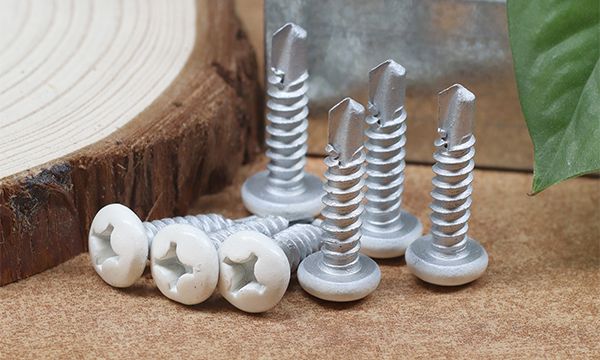
7. Avoid Over-tightening
Over-tightening screws can cause screw head breakage or material cracking. When installing, ensure the screw is tightened to the appropriate level, avoiding excessive force.
8. Consider Material Thickness
The thickness of the material affects screw selection. If the material is too thin, using a long screw could cause it to penetrate through the backside. For thin materials, choose shorter screws to ensure a secure installation.
9. Use Anti-Rust Coating
For screws exposed to outdoor environments, especially in humid or harsh conditions, it is recommended to choose screws with an anti-corrosion coating to enhance durability and prevent rust or corrosion.
Final Thoughts
We believe that through this post, you now have a better understanding of how to use self-drilling screws and other important information. By properly selecting the screw type, using the right tools, and paying attention to detail during construction, you can easily complete high-quality fastening tasks. If you need high-quality self-drilling screws, it is recommended to choose a reliable manufacturer and supplier, such as KENENG, to meet the needs of various applications.