Metal Stamping vs Die Casting: Which One to Choose
In the field of metal parts manufacturing, Metal stamping and die casting are two widely used production processes. While both methods are capable of producing high-strength metal components, they differ significantly in terms of process flow, suitable materials, product precision, and cost control.
How to choose the process that best fits your project? Here, we will take you through everything about metal stamping vs die casting to help you make the right decision.
Table of Contents
Part 1. What is Metal Stamping?
Metal stamping is a manufacturing process that involves shaping flat sheet metal into desired forms using specialized dies and a mechanical press. Common operations in metal stamping include blanking, punching, bending, coining, embossing, and deep drawing.
The process typically uses coil or sheet materials, which are fed into a press where force is applied to form the metal into specific shapes.
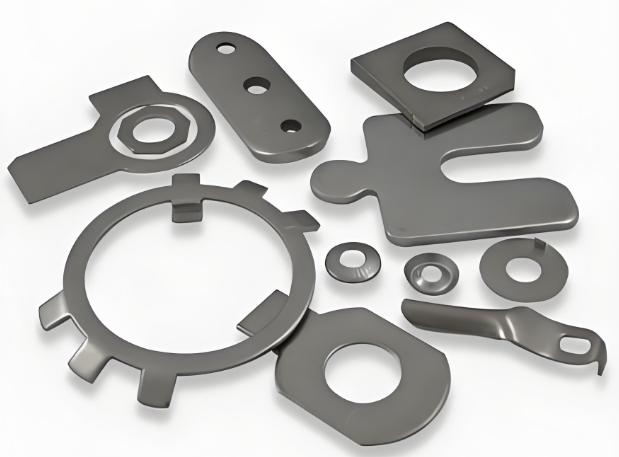
Key Features of Metal Stamping:
Material Requirements:
Metal stamping is best suited for thin sheet metals such as carbon steel, stainless steel, aluminum, brass, and copper. The metal must have good ductility to deform without cracking.
High Production Speed:
Metal stamping is ideal for high-volume production. Once the die is set up, the process can be automated and run continuously, offering excellent efficiency.
Lower Per-Unit Cost:
While initial tooling costs (die and press setup) can be significant, the cost per part decreases substantially in large-scale production, making it highly economical for mass manufacturing.
Moderate Precision:
Stamping is well-suited for simple to moderately complex parts, with tolerances that meet the needs of most structural and functional components. More precise tolerances may require secondary operations.
Common Applications:
- Automotive Parts: Used extensively for body panels, door frames, brackets, fenders, and other structural components.
- Appliance Components: Found in washing machines, refrigerators, air conditioners, and other home appliances as internal structural supports or casings.
- Electrical and Hardware Components: Such as connectors, terminals, enclosures, and mounting plates.
- Metal Frames and Housings: Used in consumer electronics, office equipment, and industrial enclosures.
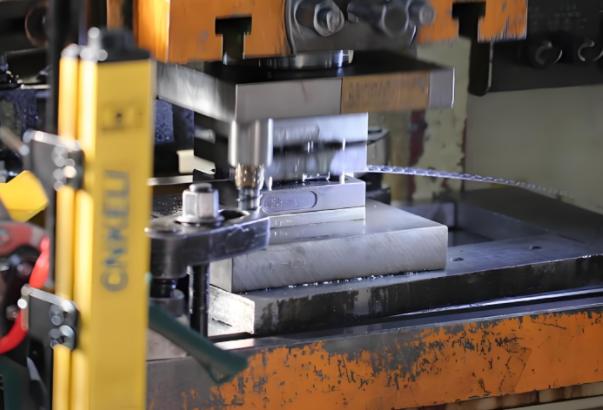
Part 2. What is Die Casting?
Die casting is a precision metal casting process in which molten metal, typically aluminum, zinc, or magnesium alloys, is injected under high pressure into a hardened steel mold (die). Once the metal fills the cavity, it rapidly cools and solidifies to form a net-shape or near-net-shape part with fine detail and excellent dimensional accuracy.
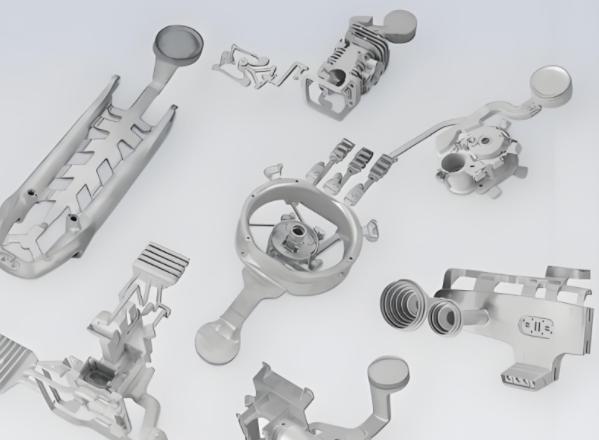
Key Features of Die Casting:
Ideal for Complex Designs:
Die casting enables the creation of parts with complex geometries, thin walls, and intricate features that would be difficult or costly to achieve through other methods. It supports integrated designs, reducing the need for multiple assembly parts.
High Dimensional Stability:
Die-cast parts offer tight tolerances, consistent dimensions, and a smooth surface finish, often eliminating the need for secondary machining. This makes it ideal for applications where both form and function are critical.
High Initial Tooling Cost:
The development of high-precision steel dies requires a significant upfront investment. However, once the tooling is completed, each unit cost becomes very low, especially in medium to large production volumes.
Excellent Material Utilization:
Die casting is highly efficient, with minimal material waste. Many systems use recycled metal, and excess material from sprues or runners can often be reused.
Fast Production Cycles:
The rapid injection and cooling process allows for quick cycle times, making die casting suitable for mass production with high repeatability.
Common Applications:
- Precision Electronic Housings: Used in smartphones, laptops, telecom equipment, and LED lighting casings due to their compact yet robust structure.
- Mechanical Inner Structures: Such as mounting brackets, gearboxes, motor housings, and frames in industrial and consumer machinery.
- Automotive Components: Widely applied in parts like transmission housings, engine blocks, oil pans, and steering system components where both strength and precision are required.
- Aerospace Lightweight Parts: Utilized for structural elements, housings, and connectors made from magnesium or aluminum alloys where weight reduction is crucial without sacrificing strength.
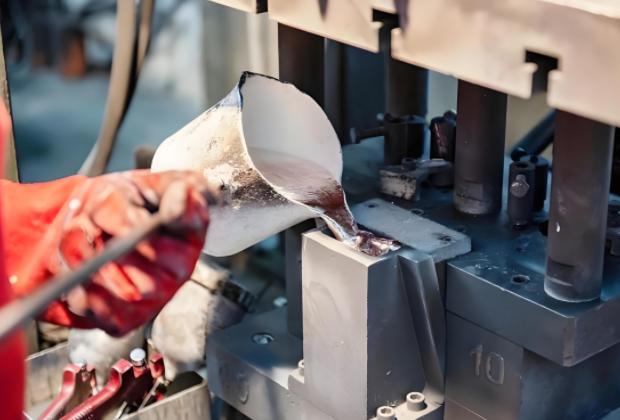
Part 3. Metal Stamping vs Die Casting: Key Differences
Choosing between metal stamping and die casting depends on your project’s specific requirements, including material type, design complexity, volume, and budget. Below is a closer look at the key differences between the two manufacturing processes:
Category | Metal Stamping | Die Casting |
Raw Material | Metal sheets (thin plates) | Molten metal (alloys) |
Process | Cold forming using stamping dies | Hot forming by injecting molten metal into dies |
Precision & Complexity | Moderate precision, suitable for simpler structures | High precision, ideal for complex geometries |
Unit Cost | Low (ideal for mass production) | Moderate (tooling cost amortized over volume) |
Initial Investment | Relatively low tooling cost | High tooling cost |
Production Volume Suitability | Medium to high volume | Medium to high volume (when high precision is needed) |
Finished Part Strength | Original sheet strength is mostly retained | Dense microstructure, high strength |
1. Raw Material
Metal Stamping: Utilizes thin sheets of metal, such as steel, aluminum, or stainless steel. These materials are typically cold-formed and available in coils or flat sheets.
Die Casting: Uses molten metal alloys like aluminum, zinc, or magnesium. The metal must be heated to a liquid state before being injected into the mold.
2. Process Type
Metal Stamping: A cold-working process where mechanical or hydraulic presses form the metal sheet through stamping dies. No melting is involved.
Die Casting: A hot-forming process that injects molten metal into a high-precision steel mold under high pressure. The part forms as the metal cools and solidifies.
3. Part Complexity & Precision
Metal Stamping: Best for simple or moderately complex shapes of metal stamping parts. Dimensional tolerances are acceptable but not as tight as die casting.
Die Casting: Suitable for parts with intricate details, thin walls, or tight tolerances. The process supports more complex geometries.
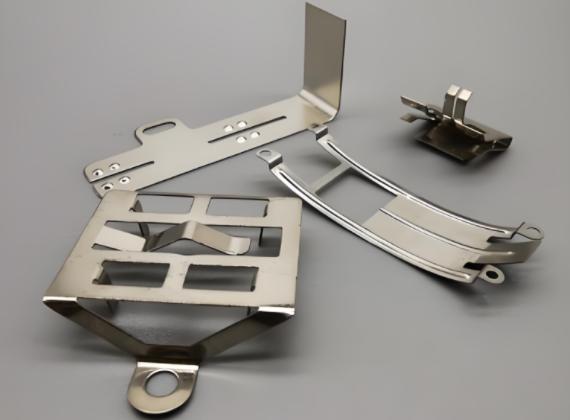
4. Tooling & Initial Investment
Stamping: Requires less complex dies, resulting in lower upfront tooling costs. Quicker and more affordable to get started.
Die Casting: Requires high-precision steel molds that are more expensive and time-consuming to produce. Ideal for long production runs.
5. Production Volume Suitability
Metal Stamping: Well-suited for high-volume production where speed and cost efficiency are priorities.
Die Casting: Also works well for medium to high volumes, especially when the parts require superior finish or complexity.
6. Per-Part Cost
Stamping: After tooling is complete, the cost per part is very low, making it economical for large quantities.
Die Casting: Higher per-part cost, especially at low volumes, but cost decreases as production volume increases.
7. Final Product Characteristics
Stamped Parts: Often lightweight and retain the strength of the original sheet metal. Good for structural components.
Die-Cast Parts: More solid and dense, with a smooth surface and high dimensional stability. Often used for visible or high-performance parts.
Part 4. Metal Stamping vs Die Casting: How to Choose?
When deciding whether to use metal stamping or die casting, several factors must be considered based on your project’s requirements. The following key aspects will help you make a more informed decision:
1. Product Structural Complexity
Simple, Symmetrical Structures: For parts with flat, bent, or uniformly patterned shapes, metal stamping is the preferred choice. It is quick and efficient for low-complexity parts that are produced in large quantities.
Complex, Hollow, or Uneven Wall Thickness: For parts with intricate details, such as ribs, deep depressions, or complex three-dimensional shapes, die casting is more suitable. The process allows for one-piece formation, which improves strength and reduces the need for further assembly or welding.
2. Precision and Surface Finish Requirements
High Precision and Surface Smoothness: For components requiring fine details, tight dimensional tolerances, and smooth surfaces (such as consumer electronics casings or mechanical parts), die casting is the better choice. The high-pressure injection process results in high-precision parts with excellent surface finish, minimizing the need for post-processing.
Moderate Precision and Cost Sensitivity: If the focus is on functional components with less stringent surface finish or dimensional requirements, metal stamping provides a more cost-effective solution, especially for parts with simpler geometries.
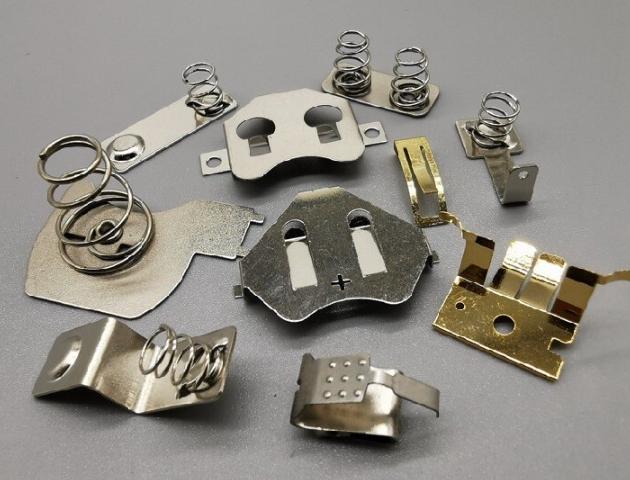
3. Production Volume and Budget Considerations
High Volume Production with Budget Constraints: Metal stamping offers very low per-part costs after the initial tooling setup. It is ideal for large-volume production, making it a cost-effective option for parts that require mass manufacturing.
High-Quality Requirements and Willingness to Invest in Tooling: Die casting involves a higher upfront tooling cost, but it provides consistent quality and precision. It is suitable for medium to high-volume production runs, especially when high-performance parts with superior surface quality are required.
4. Material Availability
Specific Metal Alloys (e.g., Zinc, Aluminum): For products that require specific alloys that need to be melted and injected into a mold, die casting is the only feasible option. This is often the case with lightweight alloys like zinc or aluminum used in precision small parts.
Need for Steel, Stainless Steel, or Other High-Strength Metals: If the product must be made from steel or stainless steel, metal stamping is the appropriate choice, as these metals have high melting points and are not suitable for die casting.
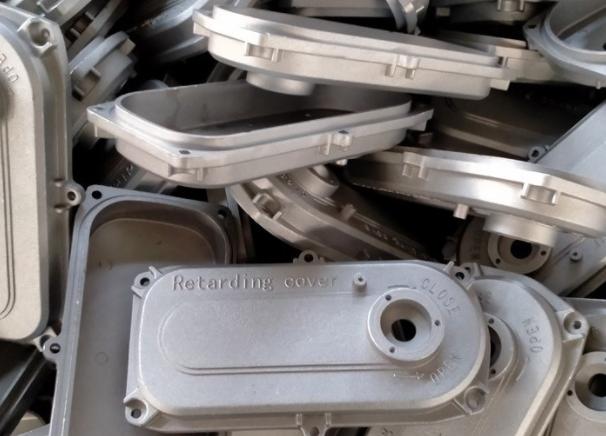
Final Words
Whether you’re a product designer, a procurement manager, or a factory supervisor, understanding the fundamental differences between metal stamping and die casting will help you better control costs, improve efficiency, and optimize quality.
If you are looking for a metal stamping service, don’t hesitate to contact KENENG, it’s a professional metal stamping service supplier that can provide you with expert advice and tailored solutions.