The Role of Custom Screws in Unique Engineering Applications
Standard screws and fasteners simply don’t meet the unique requirements of complex engineering applications. This is where custom screws come into play. Tailor-made to exact specifications, custom screws are crucial for overcoming the challenges faced in various industries. They ensure a secure, reliable connection, and contribute to the overall functionality and safety of the final product.
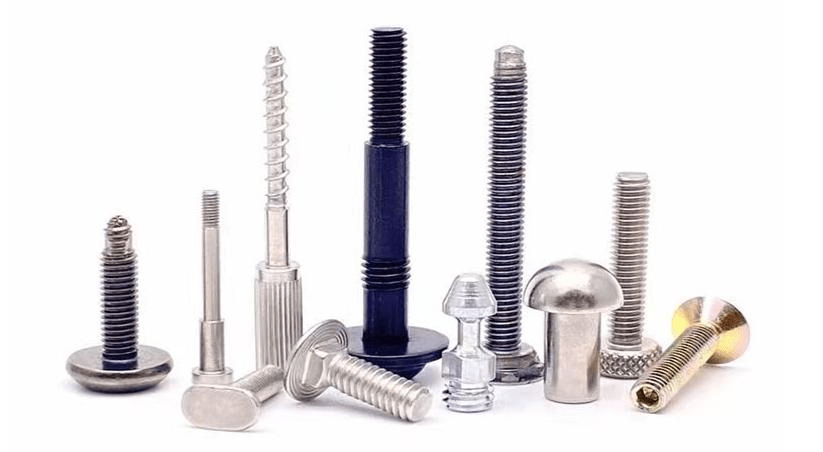
Table of Contents
Understanding Custom Screws
Custom screws are fasteners designed to meet specific technical requirements that standard commonly used screws cannot satisfy. Whether it’s the need for a particular material, size, thread type, or coating, custom screws are engineered to address the unique challenges posed by a particular application. The flexibility to adjust specifications makes them ideal for industries where standard fasteners may fall short.
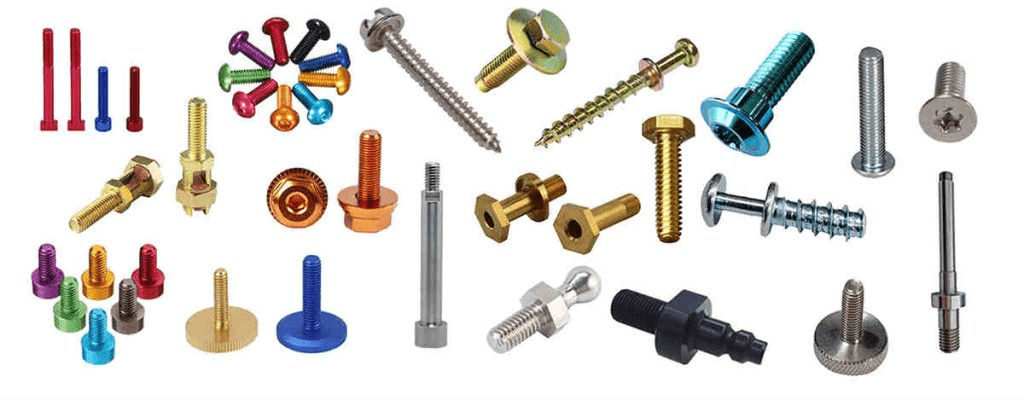
Benefits of Custom Screws for Unique Engineering Applications
1. Precision Fit for Unique Applications
One of the primary benefits of custom screws is their ability to fit precisely into unique designs. Standard screws may not meet the dimensional, threading, or material requirements of certain applications, leading to weak connections or improper functionality.
Custom screws are engineered to match the exact specifications of the application, ensuring a perfect fit that improves performance and reliability. Whether it’s a non-standard size, thread pitch, or shape, custom screws are designed to meet the exact needs of the assembly.
2. Enhanced Durability and Strength
Custom screws are designed to withstand the specific stresses, loads, and environmental conditions they will encounter. By selecting the appropriate materials, coatings, and design features, custom screws can be made stronger and more durable than standard fasteners.
For instance, screws used in high-vibration environments like automotive or aerospace applications may be designed with special thread patterns that increase their grip and resistance to loosening. Similarly, screws used in harsh chemical or marine environments can be made from corrosion-resistant materials like stainless steel or titanium to ensure long-lasting performance.
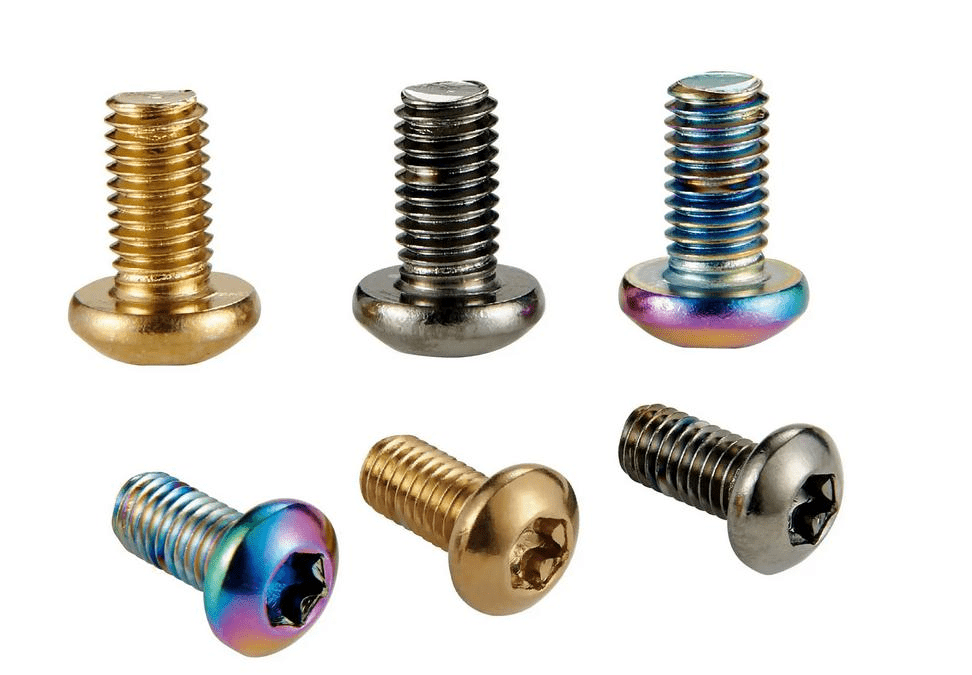
3. Optimized Performance in Specific Environments
Custom screws can be tailored to perform optimally in specific environmental conditions. For example, screws used in food processing equipment must meet hygiene standards, resist corrosion, and be easy to clean. In marine applications, screws may be coated with specialized coatings to resist saltwater corrosion and endure harsh environmental conditions. Custom screws can also be designed to operate in extreme temperatures, pressures, or high-moisture environments, ensuring reliability and minimizing the risk of failure.
4. Cost Efficiency in the Long Run
While custom screws may come with a higher initial cost than off-the-shelf alternatives, they can provide significant cost savings over the long term. By designing screws that perfectly match the requirements of the application, engineers can reduce the need for frequent repairs or replacements, resulting in lower maintenance costs.
Additionally, custom screws can improve the efficiency of the assembly process by reducing the likelihood of issues such as stripped threads or mismatched components, thus minimizing production downtime.
5. Increased Assembly Speed
Custom screws can be designed to improve the speed and ease of assembly. For instance, custom heads, drive systems, or self-tapping features can make the installation process quicker and more efficient. By eliminating the need for additional tools or lengthy adjustments during assembly, custom screws help streamline production processes, reduce labor time, and minimize the risk of human error. This benefit is particularly valuable in industries that rely on high-volume production, such as automotive manufacturing.
6. Improved Aesthetics and Branding
Custom screws can also be used to enhance the aesthetic appeal of a product or contribute to its branding. For example, screws used in consumer electronics, luxury goods, or high-end automotive parts can be designed with unique finishes or colors that align with the product’s overall look and feel. These custom screws can provide not only functionality but also an added element of design, setting the product apart from competitors in the market.
7. Tailored for Special Assembly Requirements
Certain applications, particularly in sensitive industries like electronics, may require screws designed for specific assembly needs. For example, screws used in devices that require grounding or those that need to resist electromagnetic interference (EMI) can be customized to meet these precise demands. Additionally, locking screws can prevent the screws from loosening or falling out during use, improving both safety and reliability.
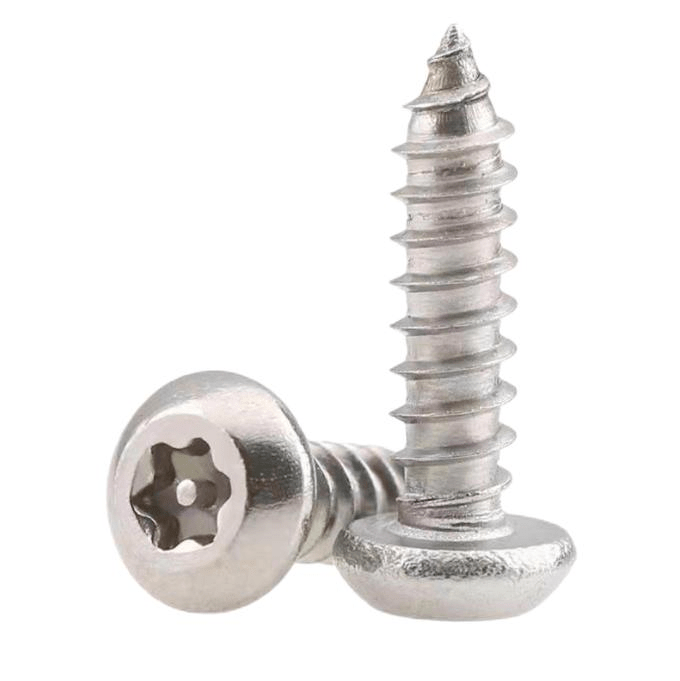
Applications of Custom Screws
1. Aerospace
In the aerospace industry, safety, strength, and reliability are paramount. Custom screws are used in the assembly of aircraft and spacecraft components, including engines, fuselages, landing gear, and control systems. These fasteners must be designed to withstand extreme pressures, high temperatures, and vibrations during flight, all while maintaining structural integrity. Materials like titanium and high-strength alloys are commonly used to ensure that custom screws provide the necessary strength-to-weight ratio and resist corrosion in challenging environments.
2. Automotive
Custom screws are widely used in automotive manufacturing, where they secure everything from engine parts to interior components. In high-performance vehicles, custom screws are required to endure high vibrations, extreme heat, and heavy mechanical stress.
Automotive manufacturers also use custom screws for electronic components, brake systems, chassis, and suspension systems, ensuring that all parts remain securely fastened under demanding driving conditions. Additionally, custom screws may be required for parts designed to reduce weight or enhance aerodynamics, like lightweight alloy screws in carbon fiber components.
3. Medical Devices and Implants
The medical industry relies on custom screws for a wide range of applications, including surgical implants, medical instruments, and diagnostic devices. These screws are designed to meet stringent biocompatibility and safety standards, ensuring that they do not cause adverse reactions within the human body. For instance, screws used in orthopedic implants must be made of materials like titanium or stainless steel to ensure they integrate properly with bone while providing the necessary strength and support for bone healing.
Custom screws in medical devices must also be designed for precision and ease of use in clinical settings. Features such as non-slip heads, easy insertion, and the ability to withstand sterilization processes are critical for medical screws used in surgical procedures and medical equipment.
4. Electronics
In the electronics industry, custom screws are used in everything from consumer electronics to critical components in communication systems, medical devices, and aerospace electronics. These screws are designed for lightweight, high-precision applications where ensuring a stable and secure connection is essential. Often, the screws must also resist electromagnetic interference (EMI) or provide grounding for electronic circuits.
Custom screws are often used in mounting circuit boards, securing battery compartments, and assembling enclosures that house sensitive components. Small, lightweight screws with fine threads are common in this industry, as they allow for tight and secure fastening in compact devices.
5. Marine
Marine applications require fasteners that can resist corrosion from saltwater, withstand high pressures, and perform reliably in harsh environmental conditions. Custom screws are used in various marine equipment, such as boats, ships, submarines, and offshore platforms. These stainless steel screws, captive screws or screws coated or made from special marine-grade alloys are used to ensure they last in salty, humid, and often high-pressure conditions.
In boat construction, custom screws are used to secure hulls, propulsion systems, and rigging. They must be designed to resist corrosion and maintain structural integrity even after years of exposure to harsh ocean conditions.
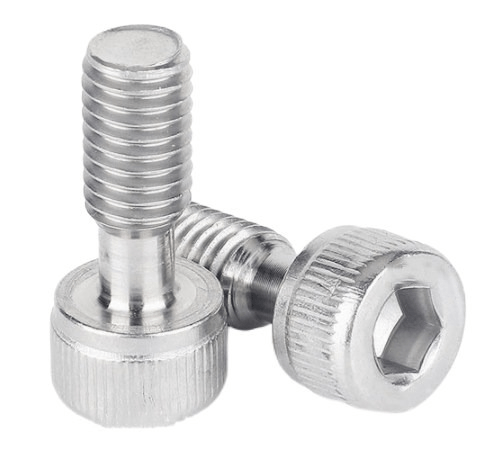
6. Construction and Heavy Machinery
In the construction and heavy machinery sectors, custom screws are used to fasten critical components, from steel frames to engine parts. These screws must be able to handle large loads, resist wear, and withstand exposure to harsh environments such as high temperatures, moisture, and vibration. Custom screws are essential for securing parts in cranes, bulldozers, excavators, and other industrial machinery, where standard screws might not provide the necessary durability or load-bearing capacity.
Specialized screws may also be designed for use in high-stress areas such as structural beams or load-bearing parts of construction equipment. These custom fasteners ensure the longevity and safety of machinery that operates under challenging conditions.
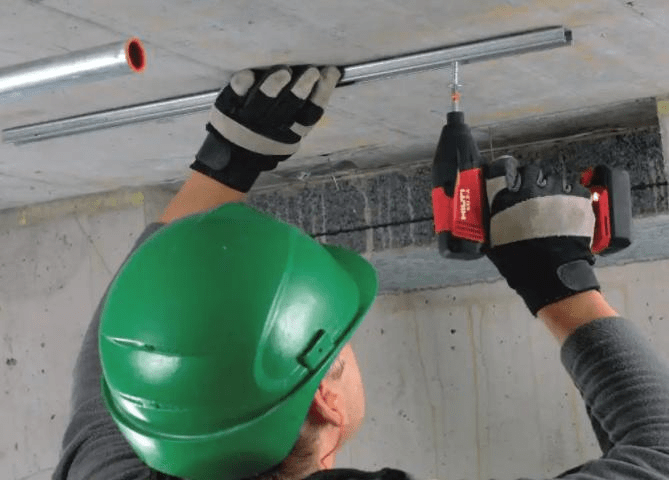
7. Renewable Energy
Custom screws are increasingly being used in renewable energy projects, particularly in wind, solar, and hydroelectric energy systems. In wind turbines, for example, custom screws are needed to secure blades, generators, and other critical components while ensuring resistance to extreme weather conditions and vibrations. In solar panel installations, custom screws are used to secure panels to their frames and mount them to rooftops or ground-mounted systems.
In hydropower plants, screws are used in the assembly of turbines and other infrastructure. These screws must be resistant to the elements, as they may be exposed to water, chemicals, and varying temperatures.
8. Food and Beverage
In the food and beverage industry, custom screws play an essential role in the assembly of equipment used for processing, packaging, and distribution. These screws need to meet hygiene and safety standards, being resistant to rust and corrosion while also being easy to clean. Stainless steel screws are often used in food processing plants where sanitation is critical.
Custom screws are also used in vending machines, refrigeration units, and production lines to ensure that all components remain securely fastened and operate efficiently.
9. Military and Defense
The military and defense industries rely on custom screws to assemble everything from armored vehicles and weapon systems to aircraft and communication equipment. These screws are designed to withstand extreme conditions, such as exposure to shock, vibration, high temperatures, and moisture. Custom screws must also meet military specifications for durability, reliability, and strength, ensuring that they can perform in critical situations where failure is not an option.
10. Railroad
In the railroad industry, custom screws are used in the assembly of trains, tracks, and signaling systems. These screws must be designed to handle high loads, resist wear, and endure exposure to weather and environmental elements. Custom screws are essential in ensuring the structural integrity of railroad components, such as the coupling of train cars, fastening of rail components, and securement of engine parts.
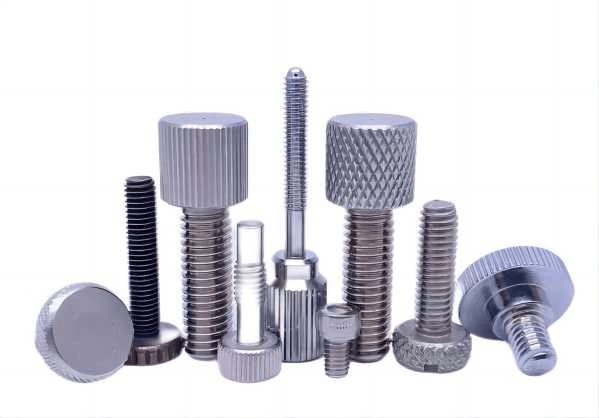
Key Considerations in Designing Custom Screws
These considerations help engineers customize screws for demanding applications, ensuring they meet both functional and environmental requirements.
Consideration | Description | Impact on Design | Example Application |
Material Selection | Selecting screw materials based on strength, corrosion resistance, weight, and environmental factors | Ensures that the screw performs optimally in harsh or specialized conditions | Aerospace: Lightweight, high-strength titanium screws for structural components |
Screw Thread Type and Pitch | Customizing the thread profile (e.g., trapezoidal, square, or ACME threads) for specific load or torque needs | Affects the grip, force distribution, and ease of assembly | Heavy Machinery: Coarse threads for quick assembly under high torque |
Strength and Fatigue Resistance | Tailoring the screw for specific loading conditions, including tensile, shear, and impact forces | Ensures the screw can withstand operational stresses without failure | Wind Turbines: Screws designed to handle constant vibration and heavy loads |
Temperature Resistance | Designing screws for extreme temperature conditions, from cryogenic to high-temperature environments | Prevents screw material degradation and maintains integrity under thermal stress | Cryogenic Systems: Screws for tanks storing liquid gases that maintain performance at low temperatures |
Corrosion Resistance | Choosing coatings or materials that withstand exposure to moisture, chemicals, or saltwater | Extends the lifespan of the screw in corrosive environments | Marine Applications: Stainless steel screws with anti-corrosion coating for boat hull fittings |
Custom Head Design | Designing heads for specific tools, ergonomic handling, or visual appeal (e.g., hex, countersunk, or flanged) | Improves usability, aesthetic integration, and assembly precision | Consumer Electronics: Small, flat screws with custom heads for compact assembly in electronics |
Size and Load Capacity | Defining the screw’s dimensions and load-bearing capacity for proper fit and application | Ensures compatibility with components and supports required loads | Construction: Large, heavy-duty screws for securing steel beams in high-rise buildings |
Vibration Resistance | Designing screws to minimize loosening or wear under constant vibration or dynamic loading | Improves long-term stability and reduces maintenance needs | Automotive: Locking screws in engine components exposed to vibration |
Fatigue Life and Durability | Ensuring that screws perform reliably over prolonged use without degrading | Important for high-use applications that require longevity and reduced maintenance | Railway: Custom screws used in track assembly, which need to resist wear from constant movement |
Environmental Impact | Considering eco-friendly materials or designs that reduce waste or energy consumption in manufacturing | Meets sustainability goals and reduces environmental footprint | Renewable Energy: Screws designed for solar panels that are made from recyclable materials |
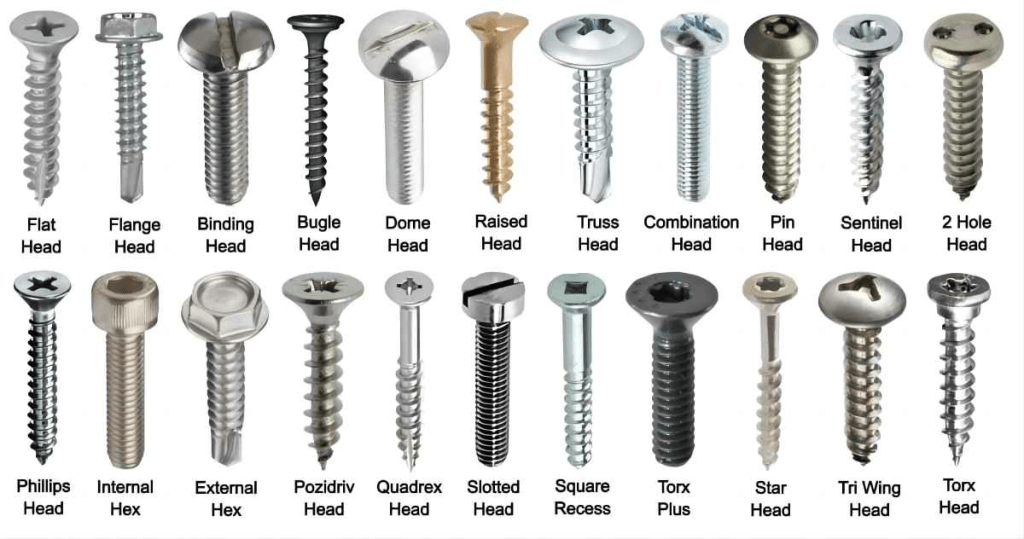
Summary
The ability of custom screws to be tailored to precise specifications allows engineers to solve problems that cannot be addressed with standard fasteners. From the selection of materials to the design of threads, sizes, and coatings, custom screws provide the flexibility and performance needed to ensure the success of demanding engineering projects. Whether it’s ensuring the safety of an aircraft, the durability of an automotive engine, or the reliability of medical devices, custom screws are essential to achieving the high standards required in modern engineering.