The Role of Disc Springs in Extreme Temperature Environments
Disc springs, also known as Belleville washers, are a specialized type of spring designed to provide high force within a compact space. When it comes to extreme temperature environments, disc springs offer remarkable performance and reliability, making them essential components in critical systems.
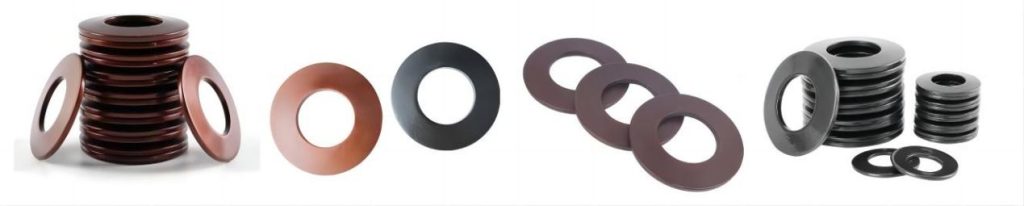
The Importance of Disc Springs in Extreme Temperature Environments
Extreme temperature environments present significant challenges for mechanical components, particularly those that must maintain precise force or load characteristics. Whether in extremely high or low temperatures, the performance of common used ordinary springs and mechanical components can degrade, leading to potential system failures.
Challenges of Extreme Temperature Environments
Extreme temperature environments pose significant challenges to mechanical components, including:
- Thermal Expansion and Contraction: Materials expand when heated and contract when cooled. This can lead to misalignment, increased stress, and potential failure of components if not properly managed.
- Material Property Degradation: The mechanical properties of materials, such as strength, elasticity, and fatigue resistance, can degrade at extreme temperatures. For example, some materials may become brittle at very low temperatures or lose their strength at high temperatures.
- Thermal Cycling: Repeated heating and cooling cycles can cause mechanical fatigue, leading to wear and eventual failure of components.
Disc springs are conically shaped washers that can be stacked in various configurations to achieve specific load and deflection characteristics. They are specifically engineered to handle these demanding conditions, ensuring consistent performance and longevity.
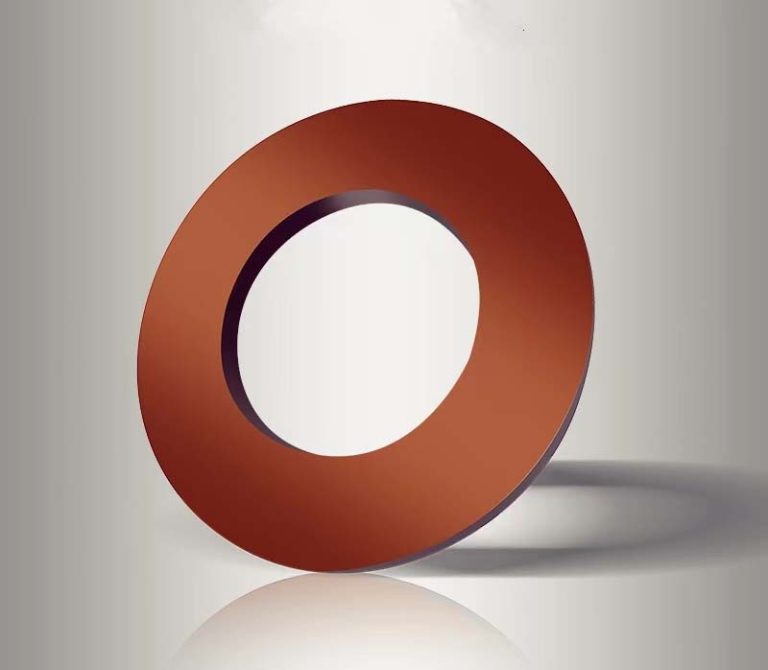
Key Advantages of Using Disc Springs in Extreme Temperature Environments
1. Material Versatility
Disc springs can be manufactured from a wide range of materials, each selected for its ability to perform under specific temperature conditions. This material versatility allows engineers to choose disc springs that maintain their mechanical properties, such as strength and elasticity, across extreme temperature ranges.
Stainless Steel
- Temperature Range: Typically -200°C to +300°C
- Applications: Stainless steel disc springs are used in environments where moderate to high temperatures are encountered. They offer good corrosion resistance and maintain their properties across a broad temperature range.
Inconel
- Temperature Range: Up to +700°C
- Applications: Inconel is a high-performance nickel-chromium alloy known for its excellent resistance to high temperatures and oxidation. Disc springs made from Inconel are ideal for applications in aerospace, power generation, and other high-temperature industries.
Hastelloy
- Temperature Range: Up to +800°C
- Applications: Hastelloy alloys are known for their exceptional corrosion resistance and high-temperature stability. Disc springs made from Hastelloy are often used in chemical processing and high-temperature corrosive environments.
Titanium
- Temperature Range: Up to +300°C
- Applications: Titanium disc springs are lightweight and offer excellent strength-to-weight ratios. They are used in aerospace and other applications where both temperature resistance and weight reduction are critical.
Phosphor Bronze
- Temperature Range: -40°C to +150°C
- Applications: Phosphor bronze offers good corrosion resistance and is often used in applications where the temperature is not excessively high but where electrical conductivity or corrosion resistance is required.
2. Consistent Force Delivery
In extreme temperature environments, maintaining a consistent force is crucial. Disc springs are designed to provide uniform force or load across a range of temperatures. This consistency is particularly important in applications requiring precise pressure or load, such as in clamping mechanisms or sealing systems. The ability of disc springs to maintain consistent performance ensures that systems operate reliably, even as temperatures fluctuate.
3. Thermal Expansion Compensation
Temperature changes can cause materials to expand or contract, potentially leading to misalignment or mechanical failure. Disc springs can compensate for thermal expansion and contraction, helping to maintain the alignment and functionality of mechanical assemblies. This capability is essential in environments where temperature variations are significant, such as in power plants or aerospace applications.
4. Resistance to Creep and Relaxation
Creep (permanent deformation) and relaxation (loss of force over time) are common issues in high-temperature environments. Disc springs, especially those made from high-temperature alloys like Inconel, are resistant to these effects. This resistance ensures that the springs maintain their load-bearing capabilities over extended periods, even under extreme thermal stress. This durability reduces the need for frequent maintenance or replacement, enhancing the overall reliability of the system.
5. Compact Design for Space-Constrained Applications
The compact design of disc springs is a significant advantage in environments where space is limited, such as in aerospace, automotive, and power generation systems. Despite their small size, disc springs can generate a high force, making them ideal for applications where both space efficiency and performance are critical. Their ability to fit into tight spaces without compromising on load-bearing capacity is a key reason for their widespread use in extreme temperature environments.
6. Durability and Longevity
Disc springs are designed to endure harsh conditions, including exposure to extreme temperatures, without significant wear or degradation. Their robust construction and material selection ensure a long service life, even in the most demanding environments. This durability translates into fewer replacements, reduced downtime, and lower maintenance costs, making disc springs a cost-effective solution for long-term applications.
7. Vibration Damping
In extreme temperature environments, vibrations can be amplified due to thermal effects. Disc springs provide excellent vibration damping capabilities, helping to protect sensitive components from damage caused by oscillations. This feature is particularly important in high-stress applications such as in aerospace and automotive systems, where maintaining stability is critical.
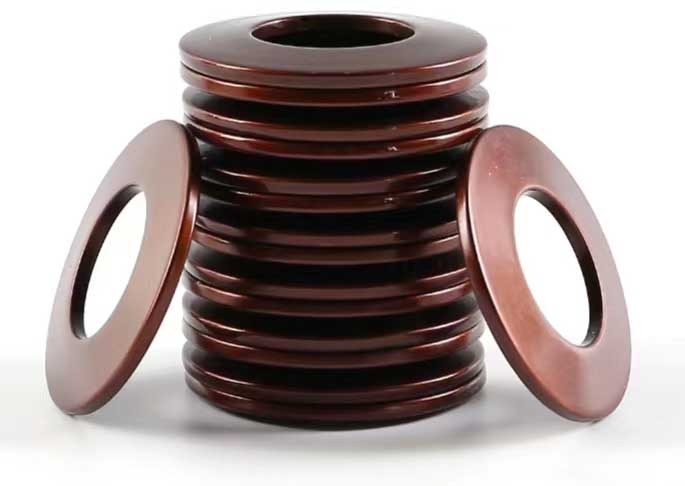
Common Applications of Disc Springs Used in Environments with Extreme Temperatures
Here’s a chart summarizing the key applications of disc springs in environments with extreme temperatures, demonstrating their versatility and robustness across different industries.
Application Area | Description | Temperature Range |
Aerospace | Used in jet engines, landing gear, and control systems where extreme temperature variations occur during flight and space missions. | -250°C to +700°C |
Power Generation | Employed in turbines, boilers, and other high-temperature equipment in power plants to maintain performance and alignment under heat. | Up to +1000°C |
Oil and Gas | Utilized in downhole tools, valves, and equipment in drilling and extraction, where they withstand high temperatures deep underground. | Up to +200°C |
Chemical Processing | Found in pumps, valves, and reactors in chemical plants, where they operate reliably under corrosive conditions and high temperatures. | Up to +800°C |
Automotive | Used in clutches, brakes, and suspension systems to handle temperature extremes and maintain performance in various driving conditions. | -40°C to +150°C |
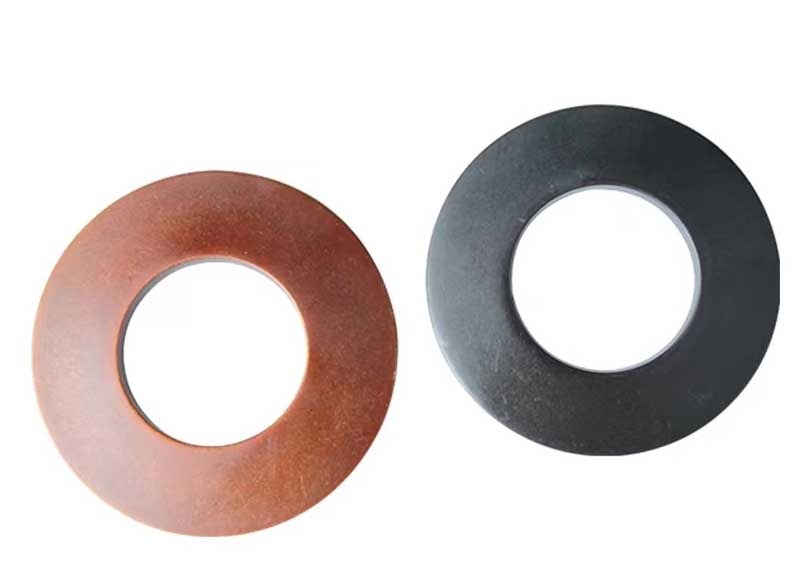
For more information and looking for a disc spring supplier in China, KENENG is a good choice for you. If you are interested in building business cooperation with us, please feel free to contact us.