Thread-forming Screws vs. Thread-cutting Screws: Key Differences and Choosing the Right Type
Fasteners are indispensable in manufacturing and assembly, providing the strength and reliability needed to hold components together. Among the many self-tapping screws, thread-forming screws and thread-cutting screws stand out as two mainly types for their versatility and specialized functions. While they serve similar purposes, the fundamental differences in their design and operational mechanics make them suited to distinct applications. Understanding these differences is essential for selecting the appropriate screw type to ensure optimal performance and longevity of an assembly.
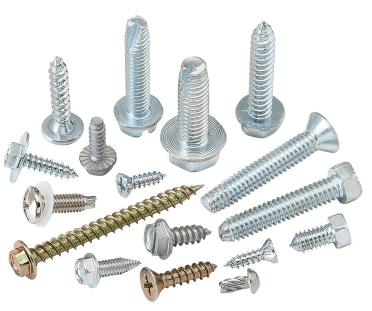
Table of Contents
What are Thread-forming Screws and Thread-cutting Screws
Thread-forming Screws
Thread-forming screws are specifically designed to create threads in materials by displacing the surrounding material rather than removing it. This displacement forms a tightly compressed region around the screw, resulting in a strong and secure fit. The nature of their operation makes them ideal for ductile materials, such as plastic, soft metals, and wood. By avoiding the removal of material, thread-forming screws minimize wear and tear on the substrate, making them particularly advantageous for applications requiring repeated assembly and disassembly. Additionally, their ability to prevent loosening under vibration adds to their reliability in dynamic environments.
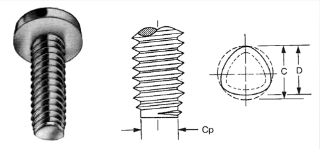
Thread-cutting Screws
Thread-cutting screws function by removing material to create threads. Equipped with sharp edges, they carve into the substrate as they are driven in, producing cleanly defined threads. This makes them highly effective for harder materials, including metals and dense composites. Since thread-cutting screws remove material, they generally require less torque during installation, which can save time and reduce wear on tools. However, the cutting process generates chips or debris, which can be problematic in applications where cleanliness is paramount. Despite this, their precision and efficiency in harder substrates make them indispensable in industries such as construction and metalworking.
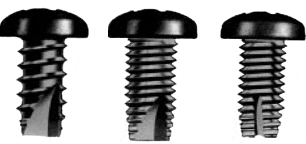
Key Differences Between Thread-forming Screws and Thread-cutting Screws
This chart highlights the primary differences between thread-forming screws and thread-cutting screw, aiding in the selection of the right option for specific applications.
Aspect | Thread-forming Screws | Thread-cutting Screws |
Thread Formation | Displaces material to form threads. | Cuts material to form threads. |
Material Compatibility | Best for ductile materials like plastic, soft metals, and wood. | Ideal for harder materials like metals and dense composites. |
Torque Requirement | Requires higher torque due to material displacement. | Requires lower torque due to cutting action. |
Debris Generation | No debris produced during installation. | Produces chips or debris as material is removed. |
Resistance to Vibration | Provides excellent resistance to loosening under vibration. | May loosen under vibration without additional locking measures. |
Installation Speed | Slower installation due to higher torque needs. | Faster installation with less effort. |
Reusable Threads | Threads can maintain their integrity after repeated use. | Threads may degrade with repeated use due to material removal. |
Typical Applications | Electronics, automotive, and appliances. | Construction, metalworking, and electrical enclosures. |
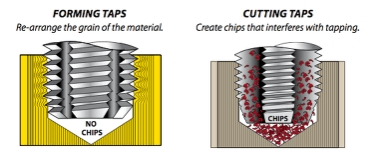
How to Choose Between Thread-forming Screws and Thread-cutting Screws
Selecting between thread-forming screws and thread-cutting screws requires a thorough understanding of the application requirements, the material being fastened, and the environmental conditions. Both types of screws offer unique advantages, and the choice largely depends on the specifics of the project.
1. Material Type
The properties of the screw material being fastened play a crucial role in the selection process. Thread-forming screws are ideal for ductile materials like plastic, wood, and soft metals. They displace material to create threads, maintaining the integrity of the substrate. In contrast, thread-cutting screws are better suited for harder materials, such as steel, aluminum, or dense composites, where their cutting action produces clean, well-defined threads.
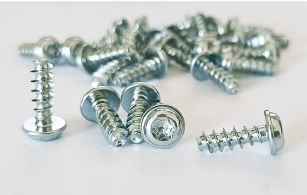
2. Resistance to Vibrations
For applications subject to frequent vibrations, such as in automotive or industrial machinery, thread-forming screws provide superior performance. The compressed material around their threads offers excellent resistance to loosening. Thread-cutting screws, while strong, may require additional locking mechanisms to maintain a secure hold in such conditions.
3. Debris Considerations
If cleanliness during assembly is critical, thread-forming screws are the preferred option, as they do not generate debris. Applications in electronics or precision assemblies benefit from this feature. On the other hand, thread-cutting screws produce chips as they remove material, which may pose challenges in environments requiring minimal contamination.
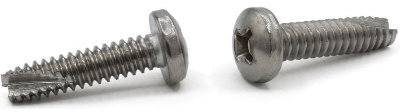
4. Ease of Installation
Thread-cutting screws require less torque during installation, making them easier and faster to drive into the material. This advantage is particularly significant in large-scale or high-speed assembly processes. Thread-forming screws, while offering a tighter fit, demand more effort and time due to their material-displacing action.
5. Reusable Threads
If the application involves frequent disassembly and reassembly, thread-forming screws are an excellent choice. They maintain the strength of the threads within the material, reducing wear over time. Conversely, thread-cutting screws may degrade the material with repeated use, as their cutting action removes material during installation.
6. Cost Efficiency
The overall cost of the project, including tools and labor, can influence the decision. Thread-cutting screws often provide a faster installation process, saving time and labor costs, especially in harder materials. However, for softer materials, thread-forming screws may offer better long-term value due to their durability and resistance to loosening.
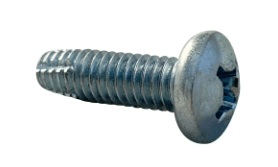
7. Application Requirements
Certain industries have specific needs that influence the choice of screws. For example:
- Thread-forming Screws: Widely used in electronics, automotive, and appliance assembly where durability and vibration resistance are critical.
- Thread-cutting Screws: Common in construction, metalworking, and electrical enclosures where precision and compatibility with harder materials are essential.
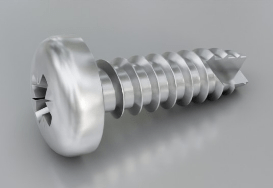
Final Thoughts
Both thread-forming and thread-cutting screws are essential tools in manufacturing and assembly, offering unique advantages based on the materials and requirements of the project. Selecting the right screw type requires careful assessment of the material, environmental factors, and the demands of the application. Through understanding their unique properties, engineers and manufacturers can ensure the reliability and longevity of their assemblies while optimizing efficiency and performance.