What are the Core Components of Galvanized Carriage Bolts
Galvanized carriage bolts, characterized by their round head with a square neck, are indispensable fasteners in construction, engineering, and various industrial applications. Their resilience to corrosion, a result of the zinc coating process, makes them particularly suitable for outdoor and demanding environments. This article delves into the core components of galvanized carriage bolts: their materials, strength grades, and the critical hot-dip galvanizing process. By understanding these factors, users can make informed decisions to select the optimal bolt for their specific needs.
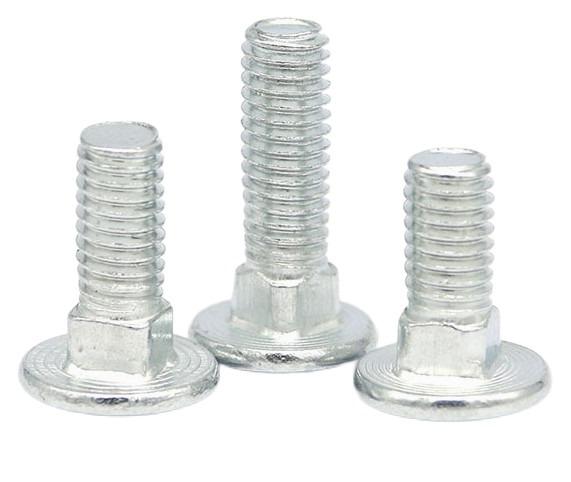
Materials Used in Galvanized Carriage Bolts
The primary materials used in manufacturing galvanized carriage bolts are carbon steel and alloy steel. The choice of material significantly influences the bolt’s performance, durability, and cost.
- Carbon Steel: This is the most common material due to its affordability and adequate strength for many applications. Carbon steel galvanized carriage bolts are suitable for general-purpose use in structures exposed to mild environmental conditions. However, they may not be ideal for highly corrosive environments or applications demanding exceptional strength.
- Alloy Steel: For enhanced strength, durability, and corrosion resistance, alloy steel is the preferred choice. It incorporates elements like chromium, nickel, or molybdenum to bolster the bolt’s mechanical properties. Alloy steel galvanized carriage bolts are often employed in critical structures, marine applications, and environments with severe weather conditions.
Strength Grades of Galvanized Carriage Bolts
Galvanized carriage bolts are classified into different strength grades according to standards set by organizations such as ASTM (American Society for Testing and Materials) or equivalent national standards. The most common strength grades are Grade 2, Grade 5, and Grade 8, each offering varying levels of tensile strength and suitability for different applications. Here is a table summarizing the key information about the grades of galvanized carriage bolts:
Grade | Material | Tensile Strength | Characteristics | Common Uses |
Grade 2 | Low carbon steel | Around 60,000 PSI | Standard quality, sufficient strength for general applications | Light-duty applications, furniture assembly, light construction |
Grade 5 | Medium carbon steel, quenched and tempered | Around 120,000 PSI | Higher strength than Grade 2, better load-carrying capacity | Moderate to heavy-duty applications, machinery, automotive components, structural assemblies |
Grade 8 | Medium carbon alloy steel, quenched and tempered | Around 150,000 PSI | Highest strength, excellent load-carrying capacity and durability | High-stress applications, heavy machinery, industrial equipment, critical structural connections |
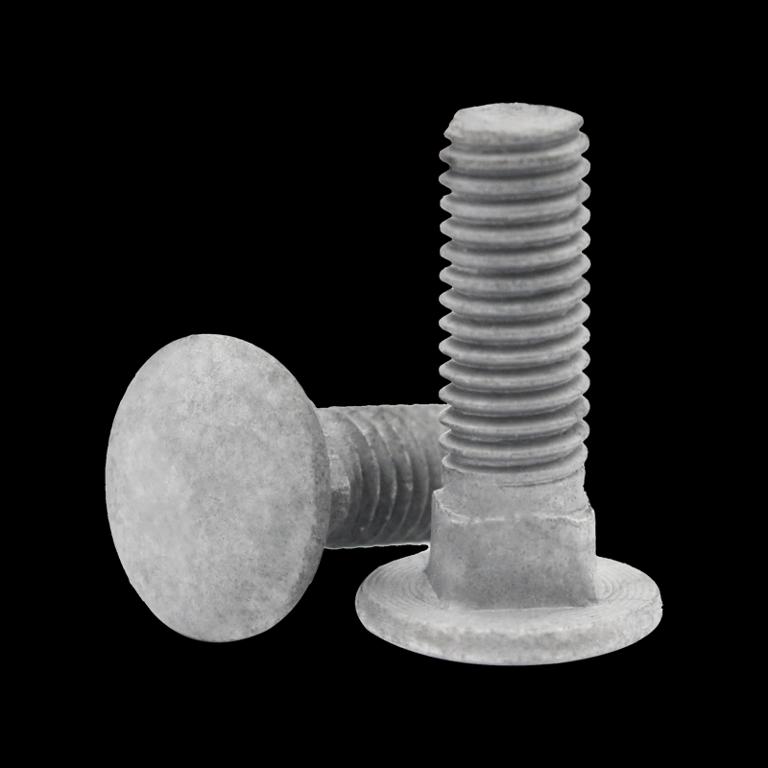
What are the Surface Treatments of Galvanized Carriage Bolts?
Galvanized carriage bolts are a versatile fastening solution, widely appreciated for their strength and corrosion resistance. The primary surface treatment for these bolts is hot-dip galvanizing, which significantly enhances their durability. However, to further elevate their performance and appearance, several additional treatments can be applied. Let’s delve into the specifics of these treatments and how they contribute to the overall quality of galvanized carriage bolts.
1. Hot-Dip Galvanizing
Hot-dip galvanizing is the cornerstone of surface treatment for galvanized carriage bolts. This process involves immersing the bolts into a bath of molten zinc at temperatures around 850°F (450°C). The high heat causes the zinc to react with the steel surface, creating a metallurgical bond that forms a multi-layered zinc coating. This coating is not only robust and uniform but also provides an effective barrier against environmental elements. The zinc layer sacrifices itself to protect the underlying metal from oxidation, ensuring that the bolts remain corrosion-free for extended periods.
2. Additional Treatments:
- Passivation: To further fortify the corrosion resistance provided by the zinc layer, galvanized carriage bolts can undergo passivation. This involves treating the bolts with a chemical solution that enhances the protective properties of the zinc coating. The passivation process results in the formation of a thin, transparent oxide film on the surface, which acts as an additional barrier against moisture and corrosive elements.
- Coloring: For applications where appearance is a critical factor, galvanized carriage bolts can be colored to match the aesthetic requirements of the project. Coloring treatments involve applying a colored coating over the zinc layer, which not only enhances the visual appeal but also provides an additional layer of protection. This can be particularly useful in architectural or decorative applications where the bolts are visible and contribute to the overall design.
- Coatings: In environments that are particularly harsh or corrosive, additional coatings can be applied to galvanized carriage bolts to provide extra protection. Epoxy or polyester coatings, for example, are often used in industrial or marine settings where the bolts are exposed to chemicals, saltwater, or extreme weather conditions. These coatings form a thick, durable barrier that shields the bolts from the elements, ensuring they maintain their integrity and performance over time.
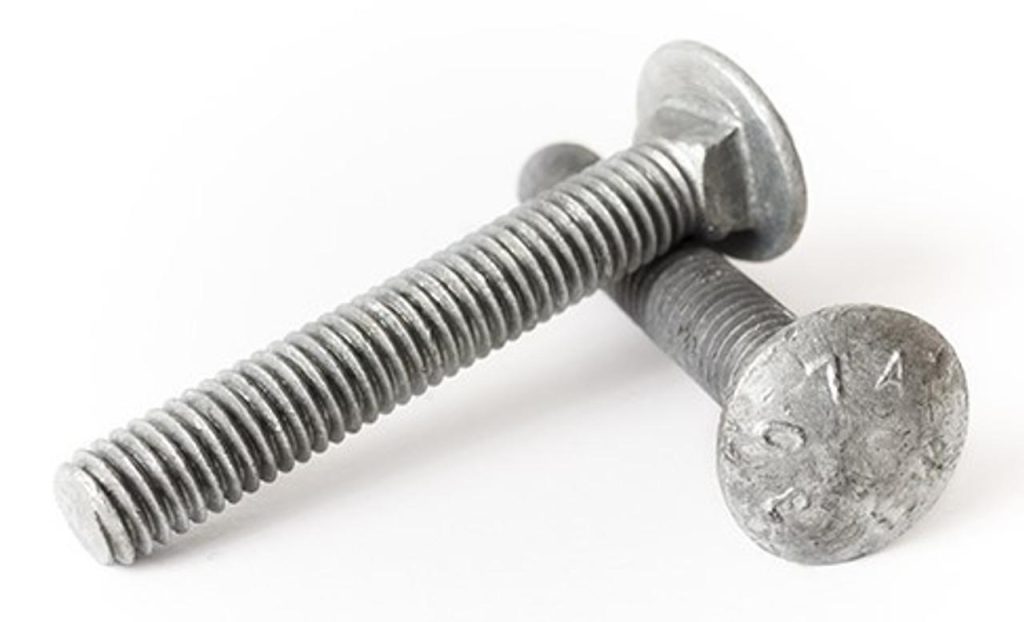
What is the Process of Hot-Dip Galvanizing?
The hot-dip galvanizing process is a critical step in enhancing the performance and longevity of carriage bolts. The process typically includes the following steps:
- Pre-treatment: Before galvanizing, the bolts must be thoroughly cleaned to remove any oil, rust, and impurities. This step is crucial for ensuring the zinc layer adheres properly to the bolt surface. Pre-treatment methods include alkaline cleaning to remove grease, acid pickling to eliminate rust, and phosphating to improve zinc adhesion.
- Drying: After cleaning, the bolts are dried completely to prevent any moisture from causing defects during the galvanizing process. Proper drying ensures a smooth and uniform zinc coating.
- Galvanizing: The dried bolts are then immersed in a bath of molten zinc heated to temperatures between 450°C and 500°C. The high temperature causes a metallurgical reaction between the zinc and the iron in the steel, forming a series of zinc-iron alloy layers. A pure zinc layer is then deposited on top of these alloy layers.
- Cooling: Once the bolts are coated with zinc, they are slowly cooled to reduce stress and ensure the uniformity and adhesion of the zinc layer. Cooling can be done naturally in the air or controlled in water or other media.
- Post-treatment: The final steps may include trimming any excess zinc, removing zinc dross, and performing a quality inspection to ensure the bolts meet the required standards.
Benefits of Hot-Dip Galvanizing for Carriage Bolts
Hot-dip galvanizing offers numerous benefits that enhance the performance and longevity of carriage bolts:
- Enhanced Corrosion Resistance: The zinc layer provides a protective barrier that shields the bolt from moisture, oxygen, and other corrosive elements, significantly extending its lifespan.
- Improved Adhesion: The zinc-iron alloy layers formed during galvanizing create a strong bond with the bolt surface, preventing the zinc layer from peeling or flaking off.
- Uniform Coating: Hot-dip galvanizing ensures a consistent and uniform zinc layer, improving the bolt’s aesthetic appearance and providing even protection across the entire surface.
- Cost-Effectiveness: While the initial cost of hot-dip galvanizing may be higher than other treatments, its long-term benefits in terms of durability and reduced maintenance make it a cost-effective solution.
- Comprehensive Protection: The galvanizing process ensures that all parts of the bolt, including recesses, corners, and hidden areas, receive adequate protection.
- Ease of Installation: Galvanized bolts are ready to use without the need for additional on-site corrosion protection, saving time and effort during installation.
- Durability: In suitable environments, galvanized bolts can last for decades without the need for maintenance, providing exceptional durability.
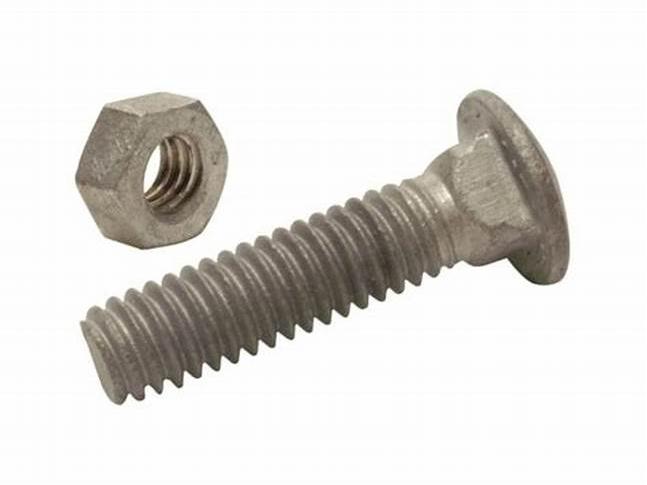
Factors Influencing Corrosion Resistance
Several factors influence the corrosion resistance of galvanized carriage bolts:
- Thickness of Zinc Layer: The thickness of the zinc layer directly impacts the level of protection. Thicker layers provide more robust corrosion resistance.
- Type of Galvanizing: Hot-dip galvanizing generally offers better protection compared to electro-galvanizing due to its thicker and more uniform zinc layer.
- Quality of Base Material: High-quality carbon or alloy steel that has been properly pre-treated ensures better adhesion and protection of the zinc layer.
- Environmental Factors: The environment in which the bolts are used plays a significant role. High humidity, temperature variations, and the presence of corrosive substances can affect the bolts’ longevity.
- Usage and Maintenance: Proper installation and regular maintenance can significantly extend the lifespan of galvanized bolts. Inspecting bolts for damage and reapplying protective coatings when necessary helps maintain their integrity.
Conclusion
In summary, the choice of material and strength grade is crucial in determining the performance and durability of galvanized carriage bolts. Hot-dip galvanizing is a vital process that significantly enhances the corrosion resistance and longevity of these bolts, making them suitable for a wide range of applications. By understanding the benefits and factors influencing corrosion resistance, users can make informed decisions to select the right galvanized carriage bolts for their specific needs. The superior protection offered by hot-dip galvanizing ensures that these bolts can withstand harsh environments and provide reliable performance over extended periods, contributing to the safety and integrity of various structures and installations.