What is a Rivet Nut
In modern manufacturing and repair, the rivet nut is a small but mighty fastener. This product shines where traditional nuts just won’t cut it, making it ideal for thin materials or hard-to-reach areas. Whether you’re a pro engineer or a hands-on DIYer, knowing what is a rivet nut, how does it work, and how they’re installed — can seriously level up your projects. Let’s dive in and see what makes this “hidden hero” so powerful.
Part 1. Understanding the Functions of a Rivet Nut
A rivet nut, also known as a blind rivet nut, a threaded insert, or a rivet nut fastener, is a metal sleeve with internal threads, designed to provide strong, reliable fastening in thin materials or hollow sections like sheet metal or tubing.
Its biggest advantage lies in its blind installation feature, meaning it can be installed from one side of the material without needing access to the back—ideal for enclosed or hard-to-reach areas. During installation, a special tool expands the rivet nut, anchoring it firmly in place and creating a durable, load-bearing thread.
Made from materials like aluminum, carbon steel, or stainless steel, rivet nuts are used across industries such as automotive, electronics, appliances, aerospace, and furniture. They are a smart and efficient solution for adding threads to thin or fragile materials where traditional nuts can’t be used, making them a true “hidden hero” of modern fastening.
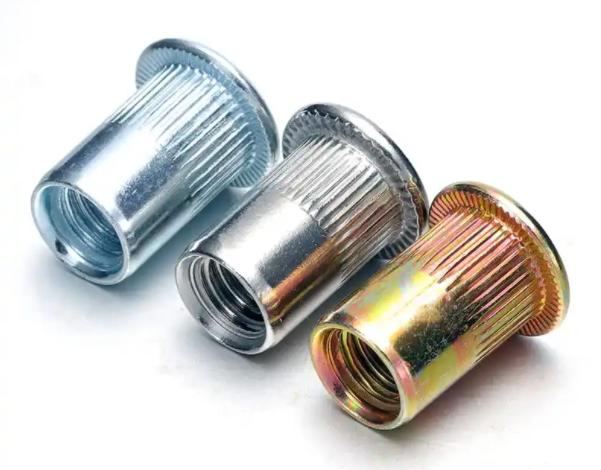
Part 2. Types of Rivet Nuts
Rivet nuts come in various shapes, head styles, and materials to meet different installation needs and performance requirements. Based on structure and material, they can be categorized as follows:
1. Round Body Rivet Nut
This is the most common and economical type. The smooth, cylindrical body makes it easy to install and suitable for general-purpose applications, especially in low to medium load scenarios. It’s widely used in industries like electronics, home appliances, and light-duty mechanical assemblies.
2. Hex Body Rivet Nut
Featuring a hexagonal outer shape, this type is designed to resist rotation after installation. Once inserted into a pre-punched hex hole, it locks firmly in place, making it ideal for high-torque or high-strength applications such as automotive components, heavy machinery, and structural frames.
3. Flat Head vs. Countersunk Head Rivet Nut
Flat-head rivet nuts sit on the surface of the material, providing a larger bearing area and strong grip. They’re suitable for most standard applications where the fastener can be visible.
Countersunk Head rivet nuts are designed to sit flush with the material’s surface after installation. These are often chosen for aesthetic or flush-mount applications, such as in consumer electronics or decorative panels.
4. Material Types
Carbon Steel Rivet Nuts: Known for their high strength and affordability, they’re suitable for most indoor and non-corrosive environments.
Stainless Steel Rivet Nuts: Offer excellent resistance to corrosion, making them ideal for outdoor, marine, or high-humidity environments. They are strong but more difficult to install and costlier.
Aluminum Rivet Nuts: Lightweight and easy to install, these are perfect for applications where reducing overall weight is important, such as aerospace or portable equipment.
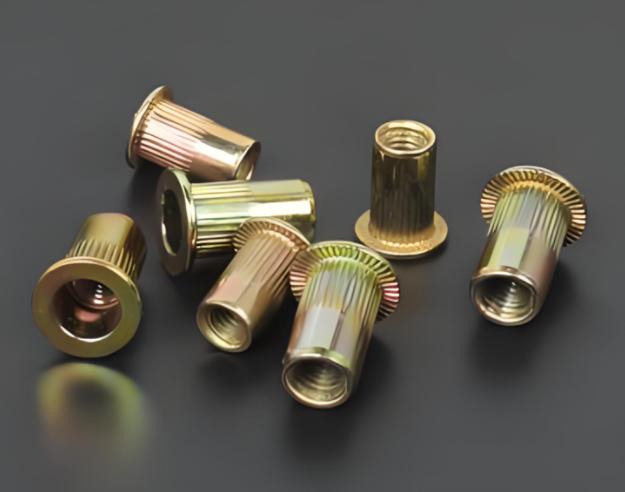
Part 3. How to Install Rivet Nut?
The rivet nut installation method provides a quick and efficient way to create strong, reliable threaded connections in thin or hard-to-reach materials using manual or power tools. Let’s see the detailed steps below.
Tools Required:
Manual Rivet Nut Tool: A hand-operated tool for individual installations or smaller batches.
Electric or Pneumatic Tools: These are more efficient for high-volume or industrial applications, as they provide faster, consistent installations.
Rivet Nut Installation Steps:
Step 1. Drill the Hole:
Start by drilling a hole in the material where the rivet nut will be installed. The hole diameter should match the outer diameter of the rivet nut, ensuring a snug fit. It’s important to ensure the hole is clean and smooth to prevent improper seating of the rivet nut.
Step 2. Insert the Rivet Nut into the Tool:
Once the hole is drilled, insert the rivet nut into the tool’s mandrel (the component that holds the rivet nut in place during installation). Ensure that the rivet nut is positioned correctly and is aligned with the hole in the material.
Step 3. Activate the Tool:
For manual tools, squeeze the handle to apply pressure. For electric or pneumatic tools, activate the device. The tool will pull the mandrel, causing the rivet nut to expand inside the hole. This action securely fastens the rivet nut to the material, creating a strong, stable threaded connection.
Step 4. Release the Tool:
Once the rivet nut has expanded fully and is securely fixed in place, release the tool. The rivet nut is now installed, and the tool can be removed.
Step 5. Efficiency and Suitability:
The installation process is quick and efficient, especially when using electric or pneumatic tools, making it ideal for batch production or large-scale projects. The rivet nut will remain firmly in place, providing a reliable threaded anchor for screws, bolts, or other fasteners, even in thin or hard-to-reach materials.
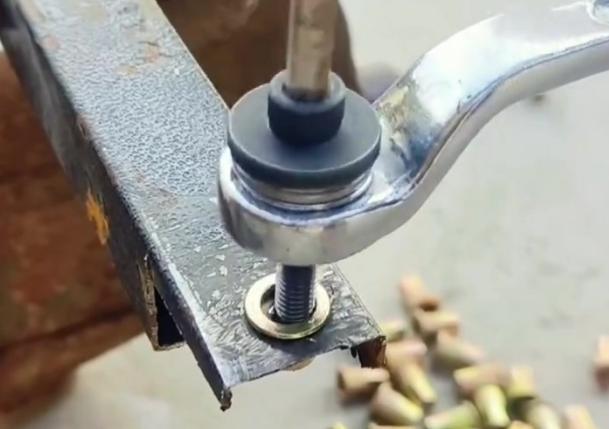
Part 4. Beneftis of Using Rivet Nuts
Using rivet nuts offers a range of benefits, including easy installation without backside access, compatibility with various materials, enhanced efficiency, and providing stable, reliable threaded connections. Let’s see their benefits below:
No Need for Backside Access
One of the key benefits of rivet nuts is their ability to be installed from a single side of the material, eliminating the need for access to the backside.
This makes them ideal for applications where the material is enclosed or when it’s difficult or impossible to reach the rear, such as in thin-walled panels or hollow structures.
Versatile Material Compatibility
Rivet nuts can be used in a wide range of materials, including steel, stainless steel, plastic, and aluminum. This versatility allows them to be used across many industries and applications, from automotive manufacturing to electronics and consumer goods, where different materials require different fastening solutions.
Enhanced Efficiency
Installing rivet nuts is a fast and standardized process, especially when using manual, electric, or pneumatic installation tools. This allows for high-speed, consistent assembly, making it ideal for both small-scale projects and large-volume production runs. The efficiency boosts overall productivity and saves time and labor costs.
Stable and Reliable Connections
Rivet nuts provide a secure and permanent threaded connection, ensuring long-lasting performance. The expanded body of the rivet nut grips tightly within the material, offering strong resistance to pull-out and torque forces.
This makes them perfect for applications that demand stable, reliable fastenings that can withstand mechanical stress over time.
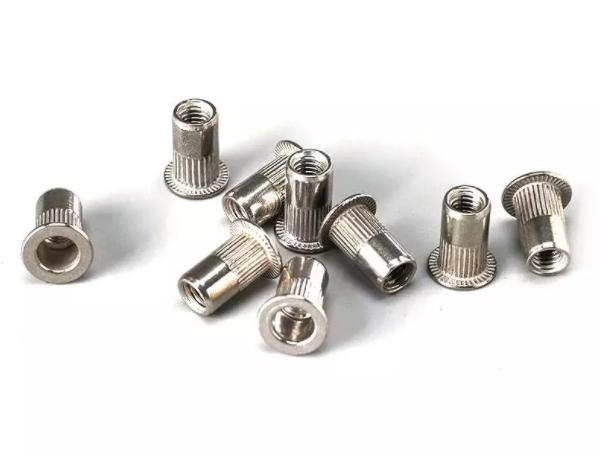
Part 5. How to Choose a Quality Rivet Nut Supplier?
When selecting a high-quality rivet nut supplier, it’s important to consider the following key factors:
Product Quality and Certification:
Ensure that the supplier offers rivet nuts that meet international standards (such as ISO, DIN, GB/T) and possesses relevant quality certifications to guarantee the reliability and consistency of the products.
Variety of Materials and Specifications:
A good supplier should offer rivet nuts in a variety of materials (such as stainless steel, aluminum alloy, carbon steel, copper, etc.) and specifications (such as M3 to M12) to meet different application requirements.
Customization and Services:
Look for a supplier that can provide customization options based on customer needs, including special sizes, surface treatments, and packaging requirements.
Production Capacity and Delivery Times:
The supplier should have a stable production capacity and be able to deliver products within agreed-upon timelines, ensuring stability in the supply chain.
Customer Reviews and Case Studies:
Check reviews and success stories from other customers to understand the supplier’s reputation and service quality.

KENENG – Reliable Rivet Nut Manufacturer
KENENG is a professional rivet nut manufacturer with over 10 years of industry experience.
Product Features:
Wide Material Options:
KENENG offers rivet nuts in a variety of materials, including stainless steel, aluminum alloy, carbon steel, iron, and copper, to meet different environmental and strength requirements.
Various Specifications and Surface Treatments:
Products range from M3 to M12 in size, with surface treatments including galvanization and passivation, ensuring good corrosion resistance and aesthetic appeal.
Custom Services:
KENENG supports OEM customization and can provide personalized rivet nut solutions based on customer CAD or 3D design files.
Strict Quality Control:
The company uses advanced technologies such as cold heading, lathe processing, and injection molding to ensure product accuracy and consistency.
Wide Application Fields:
Their products are widely used in industries like automotive, electronics, home appliances, and aerospace.
Selection Advice:
When choosing a rivet nut supplier, consider specialized manufacturers like KENENG, which offer advantages in product quality, customization capabilities, and customer service, ensuring reliable support for your projects.
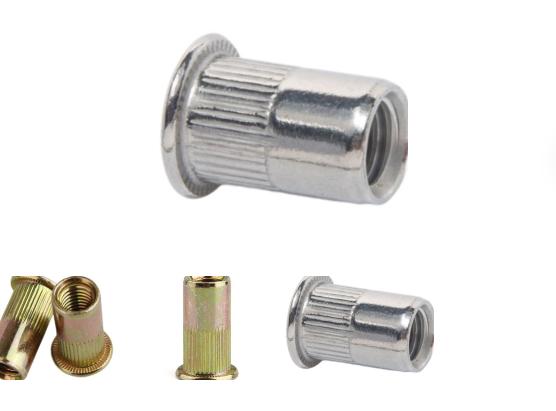
Summary
This article aims to give you a clear understanding of what rivet nuts are and their significant role in modern industries. Whether it’s in automotive, home appliances, machinery, or DIY projects, rivet nuts provide a convenient, efficient, and reliable solution for threaded connections.
If you’re looking for a professional rivet nut manufacturer or supplier, KENENG is a great option for you.