When to Choose Compression Springs: Advantages and Disadvantages Analysis
Compression springs are one of the most commonly used elastic elements in mechanical systems. These helical-shaped springs are specifically designed to resist compressive forces and store mechanical energy. When a compressive load is applied, the spring compresses, and once the force is removed, it returns to its original length. This characteristic makes compression springs essential for applications requiring shock absorption, energy storage, force buffering, and even precision measurement. Given their widespread use in a variety of industries, it’s crucial to understand the advantages and limitations of these components. This article will explore both the benefits and drawbacks of compression springs, helping engineers and designers make informed choices in their applications.
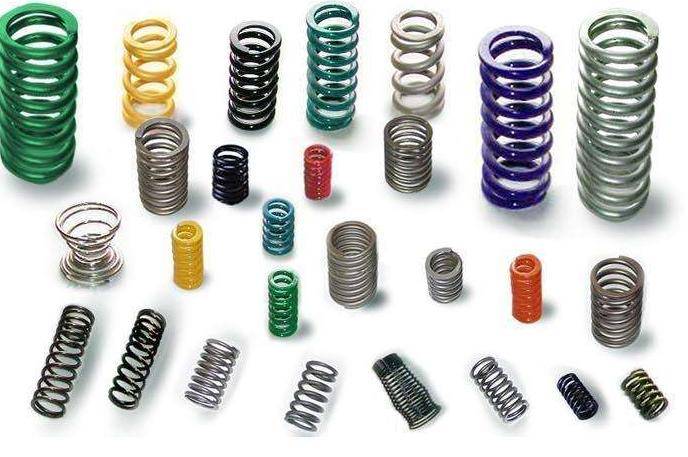
Advantages of Compression Springs
1. Excellent Elasticity
Compression springs offer exceptional elasticity, allowing them to absorb and endure substantial compressive forces without sustaining permanent deformation. Key points about their elasticity include:
- Energy Storage and Release: When compressed, these springs store mechanical energy. Once the force is removed, they return to their original shape, releasing the stored energy.
- Durability in Repeated Use: Their ability to maintain shape and function after continuous force absorption makes them ideal for systems requiring repetitive motion, such as shock absorbers.
- Application Flexibility: Compression springs are essential in vibration and impact reduction systems, including vehicle suspensions, mechanical tools, and industrial machinery.
2. Simple Structure
The structural simplicity of compression springs is a major advantage, making them both easy to produce and maintain. Specific benefits of their simple structure include:
- Ease of Manufacturing: Compression springs consist of a helical coil made from a uniform wire, making them cost-effective and easy to mass-produce.
- Low Maintenance and Installation: Their simplicity facilitates quick installation and maintenance, reducing downtime in industrial systems.
- Customization Potential: Their structure can easily be modified to meet specific requirements by adjusting diameter, length, and wire thickness, making them adaptable to various load and force needs.
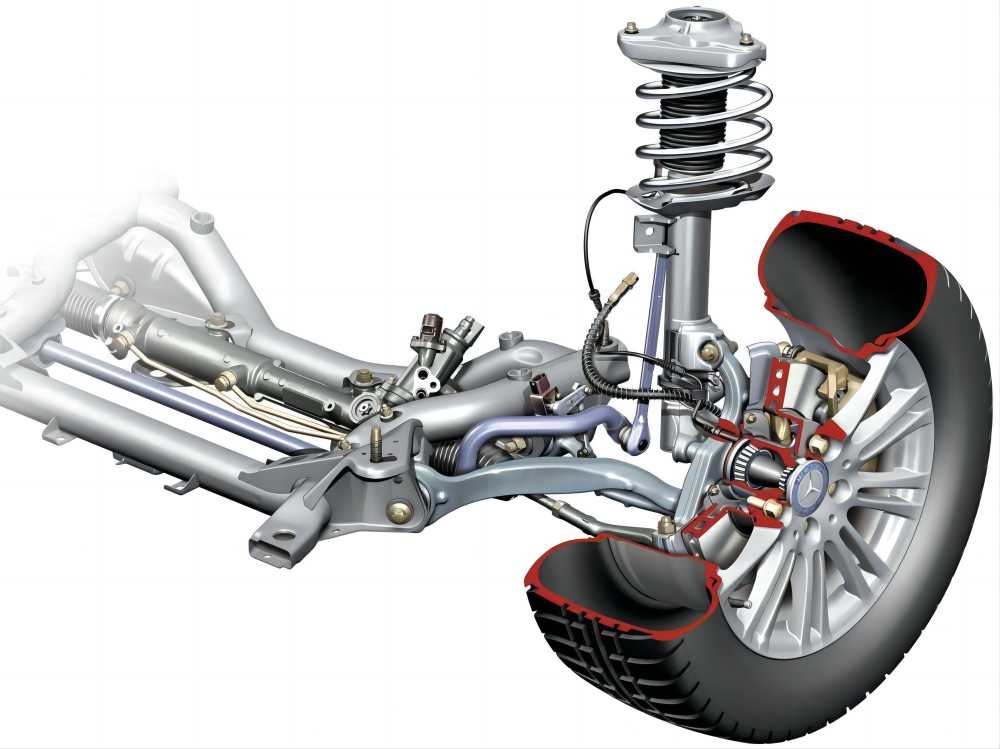
3. Wide Range of Applications
Compression springs are versatile, and their applications span various industries. Key uses include:
- Automotive Systems: In vehicles, compression springs are critical for absorbing shocks and maintaining stability.
- Electronic Devices: In electronics, they are used in battery contacts to ensure consistent electrical connections.
- Mechanical Tools: They provide resistance and control force in tools, making them integral to efficient operation.
- Adaptability to Extreme Conditions: Compression springs function in high-vibration and high-pressure systems, making them suitable for extreme environments.
4. Adjustability
One of the key advantages of compression springs is their ability to be finely tuned for specific applications. Some aspects of their adjustability include:
- Parameter Modification: By changing the diameter, wire thickness, number of coils, and material, engineers can adjust stiffness, load capacity, and overall performance.
- Application-Specific Design: For example, stiffer springs can be designed for heavier loads in automotive systems, while more delicate springs can be optimized for sensitive instruments requiring precise force control.
- Design Flexibility: This high level of customization allows engineers to optimize compression spring performance for a wide variety of uses.
5. High Reliability
Compression springs are highly reliable components, especially in safety-critical systems. Their reliability is demonstrated by:
- Longevity: When used within specified limits, compression springs offer a long service life, maintaining performance over time.
- Durable Materials: Typically made from stainless steel, carbon steel, or other durable alloys, compression springs resist wear and provide consistent performance even under repeated stress.
- Safety and Stability: In applications such as automotive brakes or industrial machinery, their consistent performance and durability are crucial for safety. They can withstand harsh conditions, such as high-vibration environments, without compromising structural integrity.
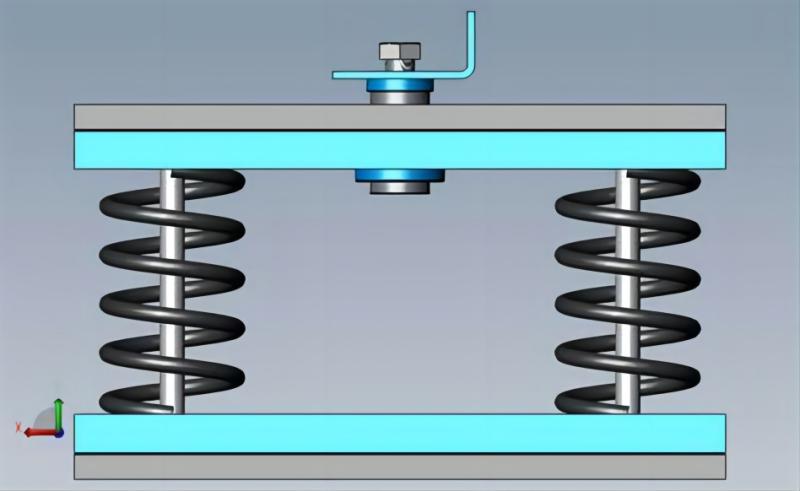
Disadvantages of Compression Springs
Despite their numerous benefits, compression springs also have some drawbacks that should be considered when selecting them for specific applications. Recognizing these limitations ensures that the spring’s performance and lifespan meet the system’s requirements.
1. Fatigue Issues
Fatigue is a major concern with compression springs, particularly when they are exposed to repetitive or continuous compressive forces. Over time, fatigue can lead to several problems:
- Loss of Elasticity: Prolonged exposure to stress weakens the spring material, reducing its ability to return to its original shape.
- Reduced Load-Bearing Capacity: The spring’s performance diminishes as fatigue sets in, leading to lower load-handling capabilities.
- Risk of Fracture: In extreme cases, fatigue can result in the spring breaking or failing altogether.
- Mitigation: Engineers may use specialized materials, surface treatments, or design modifications to reduce stress concentrations and extend the spring’s lifespan. Regular inspections can also help detect early signs of fatigue and prevent failure.
2. Temperature Sensitivity
Compression springs can be sensitive to extreme temperatures, which can negatively impact their performance:
- High Temperatures: At elevated temperatures, the spring material may lose its elasticity, resulting in reduced load-bearing capacity and poorer performance.
- Low Temperatures: In very cold environments, some materials become brittle and more prone to fracture, limiting their reliability.
- Solution: Engineers often use high-temperature alloys or specialized polymers to ensure the spring retains its properties in extreme conditions. However, this can increase manufacturing costs and may still limit performance in the most demanding environments.
3. Corrosion Problems
Exposure to moisture, chemicals, or corrosive environments can lead to corrosion, which weakens compression springs over time:
- Material Degradation: Corrosion compromises the integrity of the spring, reducing its load-bearing capacity and leading to eventual failure.
- Common in Outdoor or Harsh Conditions: Springs in outdoor applications or chemical environments are particularly vulnerable to corrosion.
- Preventive Measures: Using corrosion-resistant materials like stainless steel or applying protective coatings (e.g., zinc plating, powder coatings) can help, but these solutions increase costs and may not eliminate corrosion entirely in highly corrosive conditions.
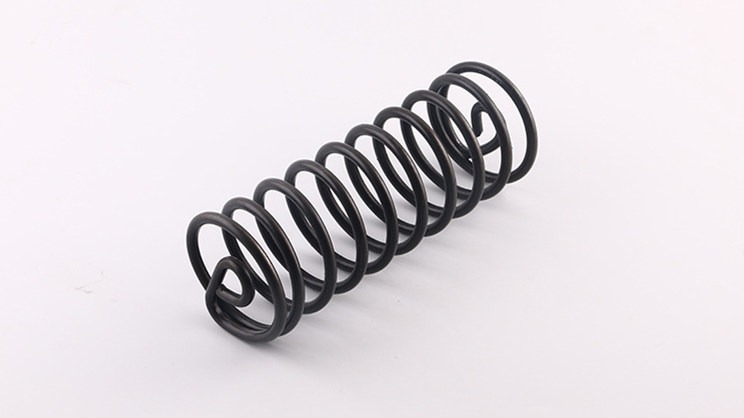
4. Space Occupancy
Compression springs sometimes require a significant amount of space to achieve the desired elasticity or load capacity:
- Size Constraints: To deliver large forces, the spring may need to be quite large, making it difficult to integrate into compact systems or devices.
- Limited Application in Tight Spaces: In environments with limited space, such as compact electronics or small machinery, the size of the spring can be a limiting factor.
- Impact on System Efficiency: Space constraints may also reduce the ability to use multiple springs or lead to design compromises that affect the overall functionality and performance of the system.
5. Non-Linearity
Compression springs do not always exhibit a perfectly linear relationship between force and compression, which can pose challenges in certain applications:
- Inconsistent Force: The force required to compress the spring doesn’t always increase at a constant rate, leading to non-linear behavior.
- Precision Limitations: This non-linearity can be a drawback in high-precision applications, where consistent and predictable force is essential, such as in sensitive measurement instruments or control systems.
- Design Adjustments: Although careful design and material selection can reduce non-linearity, it remains a limitation in applications that require high levels of precision.
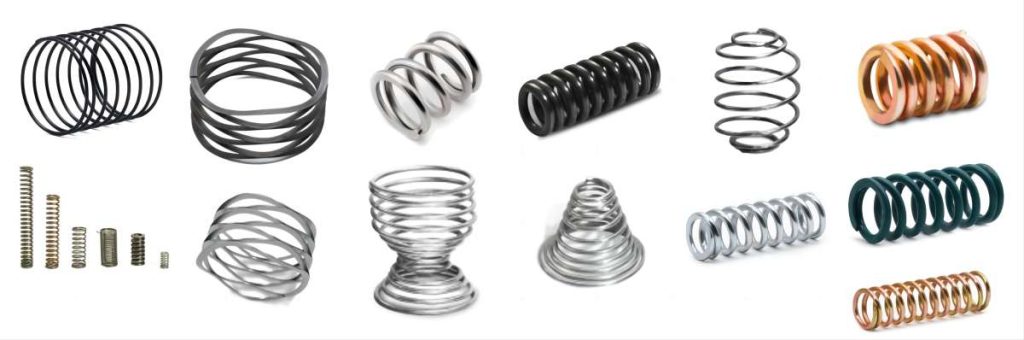
Compression springs are versatile, reliable, and cost-effective components used in a wide variety of mechanical and electronic systems, but engineers must weigh the advantages and disadvantages carefully when selecting compression springs for projects. By doing so, the full potential of compression springs can be harnessed to enhance the functionality and efficiency of various systems and devices.