Why Choose Rubber Injection Molding for Your Rubber Manufacturing Needs
Rubber injection molding is a highly versatile manufacturing process that has revolutionized the production of rubber products. This advanced technique allows for the creation of a wide range of rubber components, from simple gaskets to intricate seals and complex mechanical parts. In this article, we will delve into the world of rubber injection molding, exploring its benefits, and explaining why using a rubber injection molding machine is a smart choice for manufacturers.
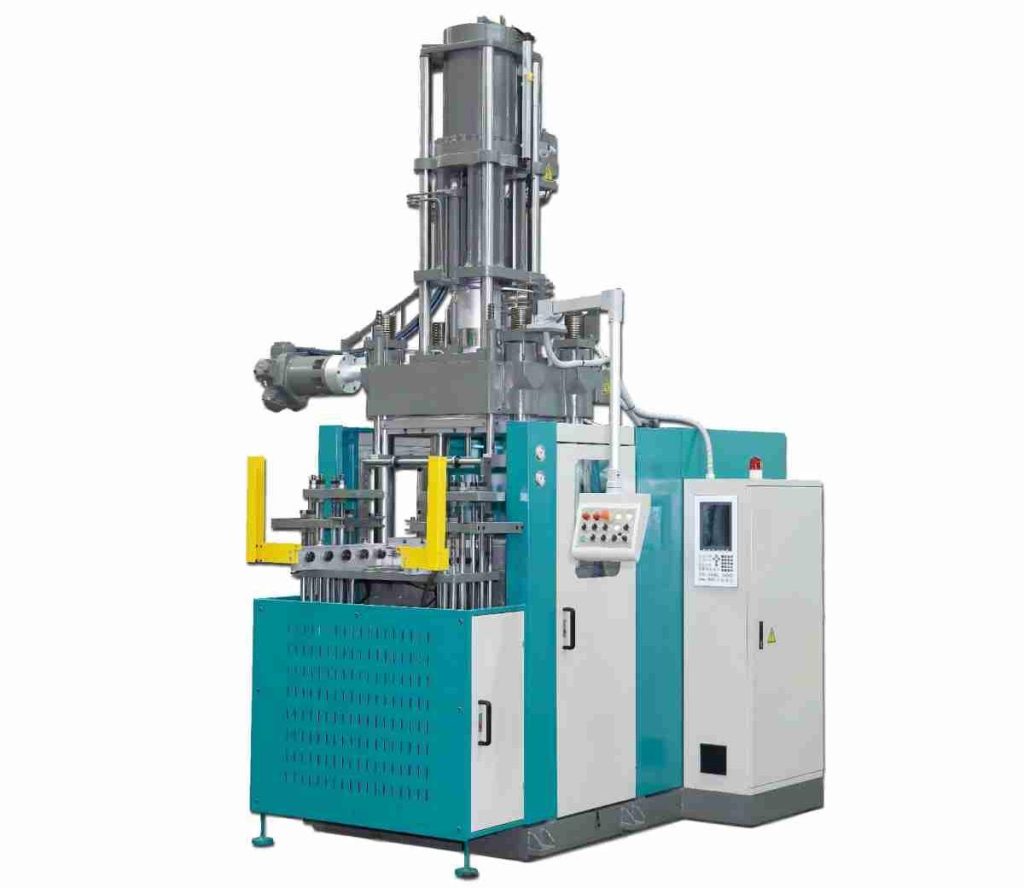
What is Rubber Injection Molding?
Rubber injection molding is a manufacturing process that involves injecting rubber material into a mold cavity, where it is heated, vulcanized, and solidified to create a final rubber product. This process stands out due to its precision, speed, and ability to produce consistent and high-quality parts.
What are the Benefits of Using Rubber Injection Molding
Rubber injection molding machines are used to produce a wide range of rubber products, from simple gaskets to complex seals and components. They offer a number of advantages over other rubber manufacturing processes, including:
1. Fast production cycle times
Rubber injection molding machines are very fast, with production cycle times that can be as short as a few seconds. This is because the rubber is injected into the mold cavity at a high pressure, which forces the rubber to fill all of the nooks and crannies of the mold quickly. Once the mold cavity is full, the rubber is allowed to cool and solidify quickly.
2. High-quality parts with consistent dimensions and tolerances
Rubber injection molding machines produce parts with high dimensional accuracy and repeatability. This is because the mold cavity is precisely controlled, and the rubber is injected into the mold at a consistent pressure and temperature. This ensures that all of the parts produced are exactly the same size and shape.
3. Low waste and emissions
Rubber injection molding is a relatively clean process, with minimal waste and emissions. This is because the rubber is injected directly into the mold cavity, and there is no need for a runner system. A runner system is a network of channels that is used to carry the molten rubber from the injection machine to the mold cavity. Runner systems can generate a lot of waste, but they are not necessary for rubber injection molding.
4. Versatile process that can be used to produce a wide range of rubber products
Rubber injection molding can be used to produce a wide variety of rubber products, from simple gaskets to complex seals and components. This is because the mold cavity can be designed to produce any shape or size of part. Rubber injection molding is also suitable for a wide range of rubber materials, including natural rubber, synthetic rubber, and blends of rubber and other materials.
5. Easy to operate and maintain
Rubber injection molding machines are relatively easy to operate and maintain. This is because they are typically automated, and the controls are relatively simple. The operator simply needs to load the rubber compound into the machine, select the mold cavity, and start the machine cycle. The machine will then automatically inject the rubber into the mold cavity, cool the rubber, and open the mold to release the part.
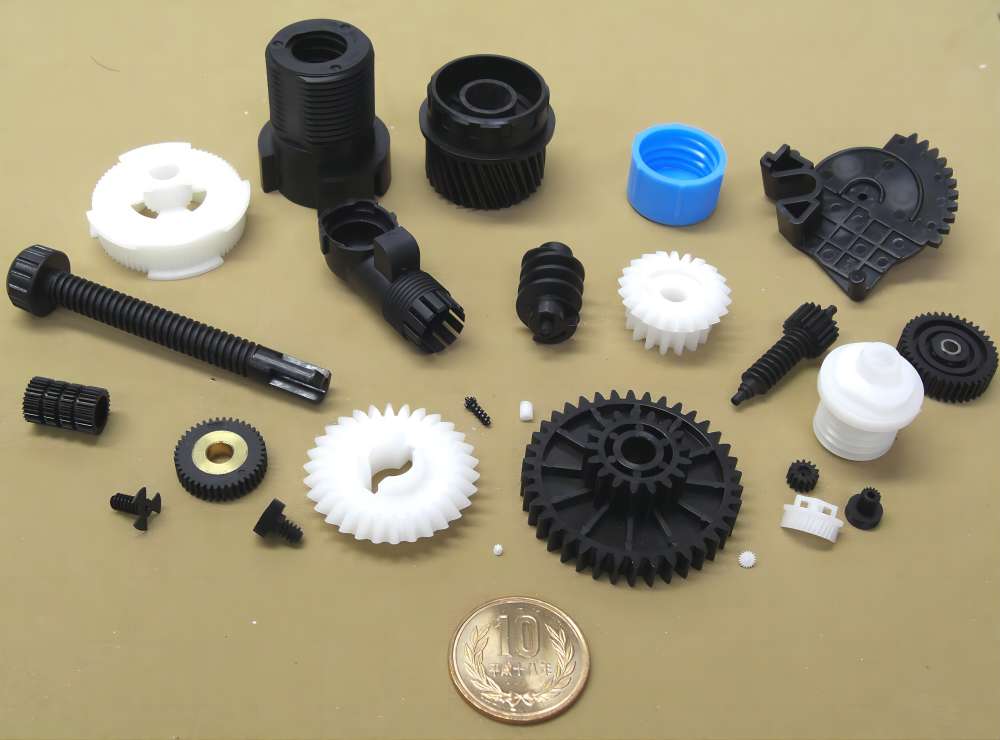
How Rubber Injection Molding Works?
The rubber injection molding process can be broken down into the following steps:
- Preparation of the rubber compound: The rubber compound is typically prepared in a mixer, where the different ingredients are blended together until a uniform mixture is obtained. The compound is then heated to a molten state in a rubber extruder. The extruder is a machine that has a rotating screw that forces the molten rubber through a heated barrel. The molten rubber is then injected into the mold cavity.
- Injection of the molten rubber into the mold cavity: The molten rubber is injected into the mold cavity through a nozzle. The nozzle is a small opening that is located at the end of the extruder barrel. The nozzle is inserted into the mold cavity, and the molten rubber is injected under high pressure. The high pressure forces the rubber to fill all of the nooks and crannies of the mold cavity.
- Cooling and solidification of the rubber: Once the mold cavity is full, the rubber is allowed to cool and solidify. The cooling time can vary depending on the size and thickness of the part. Smaller and thinner parts will cool and solidify faster than larger and thicker parts.
- Removal of the finished part from the mold: Once the rubber has solidified, the mold is opened and the part is removed. The mold is typically opened by hydraulic or pneumatic actuators. The part is then removed from the mold manually or by a robot.
Conclusion
In conclusion, rubber injection molding is a versatile and highly efficient manufacturing process that offers a myriad of benefits to companies across various industries. Its ability to produce high-quality parts with consistent dimensions and tolerances, along with its minimal waste and emissions, makes it a top choice for manufacturers looking to stay competitive in today’s fast-paced market.
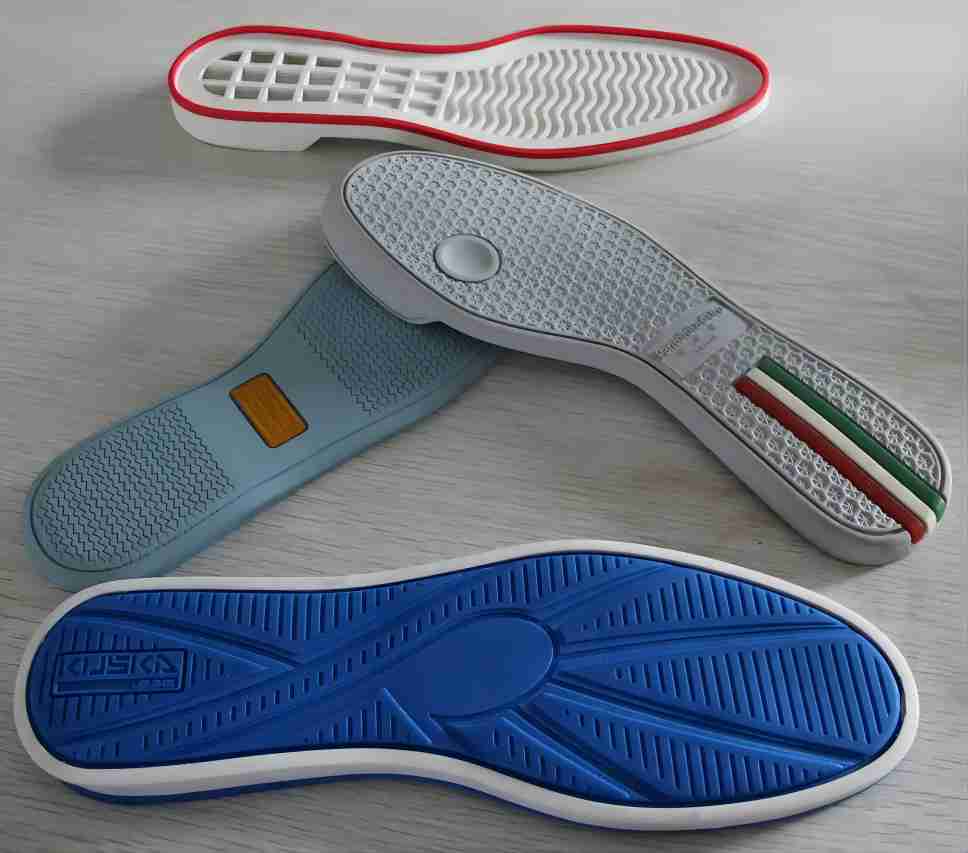
When considering rubber production methods, opting for a rubber injection molding machine is a wise decision. These machines are engineered for efficiency and ease of use, allowing manufacturers to produce top-notch rubber components quickly and consistently. If you’re in search of a manufacturing solution that combines precision, speed, and environmental responsibility, rubber injection molding is the right choice for you. Embrace this technology, and watch your rubber production capabilities soar to new heights.